106.20 Reporting
106.20.1 AASHTOWARE Project (AWP)
MoDOT implemented AASHTOWARE Project (AWP) as the data recording/handling instrument. It makes electronic reports available to designated construction project personnel who are using AWP as the project tool. The same information is also available electronically to authorized individuals who wish to access the AWP program, including supervisory personnel. Summary reports have been developed in Cognos. There are still many uses for hard copy reports for such areas as Maintenance, General Services, non-AWP projects and others, where Materials has the responsibility of making an official statement about a material for the purposes of authorizing use or payment. As the use of AWP advances, every effort should be made to utilize the Free Form abilities of it to generate reports. This will provide an electronic history file of the report for future reference. For all hard copies, the distributions as listed in this article should continue to be noted within the report body. The hard copy may be the only way the interested parties will have access to the information. In the event that there is some question with AWP as to who should be notified, these distributions may also be informative. It is not necessary to make hard copies for the State Construction and Materials Engineer except when requested or when so stated in this article. At the present time, hard copies to a specific project are not required by any district.
106.20.1.1 Automation Section
Useful Links |
Quick Reference Guides |
Sample Record General Information |
Guidelines for using AASHTOWARE AWP are located in the Quick Reference Guides.
Automation is a tool to facilitate the accumulation of data related to sampling, testing and inspection procedures. When automation services are not available to record data, alternate means must be used so the sampling, testing and inspection processes can continue. Any alternate means must be a permanent record, even if the data is subsequently transferred into the automation system.
106.20.1.2 AWP Data
AWP data will be retained on the active database for a minimum of nine years after being entered. The files will then be transferred electronically to an archival database and held indefinitely or until changes in technology make the archived files inaccessible.
106.20.1.3 Quality Management AWP Reporting
Refer to EPG 150 Quality Management for guidance.
106.20.2 Determination of Significant Digits
These procedures are intended to establish uniform methods of indicating the number of places of figures in an observed value or a calculated value to be considered significant for purposes of determining conformance with specifications. ASTM E 29 is the basis for these procedures and describes two methods identified as the Absolute Method and the Rounding Off Method. The term "test values" as used herein is intended to mean test results, and may be either "observed values" or "calculated values".
The Absolute Method applies where it is the intent that all digits in a test value are to be considered significant for purposes of determining conformance with specifications. Under these conditions, the specified limits are referred to as absolute limits. Test values with a plus and/or minus tolerance or a maximum and/or minimum are considered to be absolute values and are not to be rounded-off unless otherwise specified in this section. Reported values that are an average of two or more test values are to be rounded-off to the same number of significant digits as the individual test value even though the specification requirements are considered absolute. Test values and reported values using the absolute method are to be the same and are to show the same number of significant figures allowed by the accuracy of the test procedure and the equipment being used.
The Rounding Off Method applies where it is the intent that a limited number of places of figures in a test value are to be considered significant for purposes of determining conformance with specifications. The rounding off procedure will apply where the specified limits are not absolute and as otherwise specified in this section. Test values should be rounded off to the same number of significant places as shown in the specification for the material, except where the specification refers to a standard test method which states the number of significant places to which the results are to be reported. In such cases, report as the standard test method prescribes. As a general practice, test values are to be observed or calculated to only one place beyond the last place to be retained, and then rounded off to the number of places to be reported.
The rounding off procedure shall be as follows:
- a) When the figure next beyond the last place to be retained is less than 5, retain unchanged the figure in the last place retained.
- b) When the figure next beyond the last place to be retained is greater than 5, increase by 1 the figure in the last place retained.
- c) When the figure next beyond the last place to be retained is 5, increase by 1 the figure in the last place retained, if it is odd; leave the figure unchanged if it is even. This rounding off procedure may be restated simply as follows: When rounding off a number to one having a specified number of significant places, choose that which is nearest. If two choices are possible, as when the digit to be dropped is the numeral 5, choose the one ending in an even digit. The rounding off value should be obtained in one step by direct rounding off of the most precise value available and not in two or more steps of successive roundings.
Some examples of the rounding off of test values are as follows:
Table 106.20.2.1 Examples of Rounding off of Test Values
Observed of Calculated Value | Rounded to Nearest | Rounded-off (Reported Value) |
---|---|---|
59,940 | 100 | 59,900 |
59,950 | 100 | 60,000 |
59,960 | 100 | 60,000 |
56.4 | 1 | 56 |
56.5 | 1 | 56 |
56.6 | 1 | 57 |
0.54 | 0.1 | 0.5 |
0.55 | 0.1 | 0.6 |
0.56 | 0.1 | 0.6 |
Acceptance or rejection of material is to be based on comparison of the reported value to the specified value. Observed and calculated test values for the following materials are to be rounded as shown, even though the specification requirements have absolute limits.
a) Aggregates. Aggregate gradations performed on a passing basis are to be reported to the same number of significant places as shown in the specifications. Note that the minus No. 200 (75 μm) material in Portland Cement Concrete aggregates is specified to 0.1 percent. All gradations performed on a passing retained basis are to be reported to one decimal place, except, if a top size sieve is specified as a percent passing that part of the gradation is to be rounded and reported to the nearest whole number.
An example of applying these rules to a "passing" gradation is as follows:
Table 106.20.2.2 Examples of Rounding off “Passing” Gradations
Sec 1005 | Calculated Gradation | Reported Gradation |
---|---|---|
Pass 1 in. sieve | 99.5 | 100 |
Pass 3/4 in. sieve | 94.5 | 94 |
Pass 3/8 in. sieve | 34.6 | 35 |
Pass No. 4 sieve | 4.5 | 4 |
Pass No. 200 sieve (deleterious) | 1.57 | 1.6 |
SI Units | ||
Sec 1005 | Calculated Gradation | Reported Gradation |
Pass 25.0 mm. sieve | 99.5 | 100 |
Pass 19 mm sieve | 94.5 | 94 |
Pass 9.5 mm sieve | 34.6 | 35 |
Pass 4.75 mm sieve | 4.5 | 4 |
Pass 75μm sieve (deleterious) | 1.57 | 1.6 |
Individual deleterious substances for all aggregates are to be reported to the same number of places as shown in the specifications. The specified sum of all deleterious substances should be assumed to contain the same number of significant places as the individual deleterious substances.
The following is an example of how to compare the sum of the individual deleterious substances with the specified total of all deleterious substances.
Table 106.20.2.3 Examples of Comparing Sums of Individual with Specified Total of Deleterious Substances
Individual Reported | Value | Specified Value |
---|---|---|
Deleterious Rock | 5.2 | 6.0 |
Shale | 0.6 | 1.0 |
Chert in Limestone | 0.0 | 4.0 |
Other Foreign Material | 0.1 | 0.5 |
Sum of Percentages | 5.9 | 6.0 (Assume 6.0) |
b) Plasticity Index of Soils and Bases. Plasticity index is to be reported to the nearest whole number. To achieve this, the liquid limit and plastic limit are each calculated to one decimal place and then rounded off to a whole number. The plasticity index is the difference between these two whole numbers.
c) Standard Compaction Test (For Determination of Field and Laboratory Compaction Standard). The optimum moisture content, percent, is to be calculated to one decimal place and then rounded off to a whole number. The maximum density, pounds per cu. ft. (kg/m3), is to be calculated and rounded off in the same manner.
d) Percent Compaction. Percent compaction of embankments, bases, and bituminous mixtures, when required, shall be determined to one decimal place and rounded off to a whole number for reporting. Only the end result (actual percent compaction) of the field density test is to be rounded. The in-place weight per cubic foot, moisture content, etc., are to be determined and reported as shown in the Engineering Policy Guide.
e) Concrete. The consistency (slump) of concrete shall be measured and reported to the nearest 1/4 in. (5 mm) in compliance with AASHTO T 119. The maximum slump specified for classes B, B-1 and seal concrete is a whole number and A-1, B-2, and pavement are specified to 1/2 in. (13 mm), however, the standard test method designates a measurement to the nearest 1/4 in. (6 mm) and this would be the only rounding off performed on the measurement. Air content of Portland Cement Concrete is to be reported to the nearest 0.1 percent.
f) Steel. The following procedures for steel items will be followed unless the specifications require a greater degree of accuracy or more significant places for a particular property, in which case the number of places required by the specifications are to govern.
Table 106.20.2.4 Rounding for Steel Items
Property | Yield and Tensile Strengths | Round and Report to the Nearest |
---|---|---|
Calculated yield and tensile strength | up to 50 ksi, excl | 100 psi |
50 ksi to 100 ksi, excl | 500 psi | |
100 ksi and above | 1000 psi | |
Percent elongation and reduction in area | 0 to 10 percent, excl | 0.5 % |
10 percent and above | 1 % | |
Percent weight variation | - | 0.1 % |
SI Units | ||
Calculated yield and tensile strength | up to 345 MPa, excl | 690 kPa |
345 MPa to 690 MPa, excl | 3400 kPa | |
690 MPa and above | 6900 kPa | |
Percent elongation and reduction in area | 0 to 10 percent, excl | 0.5 % |
10 percent and above | 1 % | |
Percent mass variation | - | 0.1 % |
106.20.3 Remarks
Test reports issued after the testing of a material has been completed require remarks to indicate the status of the material. Remarks should be used to indicate acceptance, qualified acceptance, rejection, sampling condition or any other item of importance regarding the material. Standard remarks are printed by AWP based on the “Sample Status”. Specific details on failed samples should be included in General Remarks.
106.20.4 Field Reports
Acceptance or rejection of a material is based on either field testing or field testing and fabricator, manufacturer, or supplier's certifications. If a certification is used as the basis for acceptance, the AWP report shall show Acceptance Method as "CERT" (Certification Review) or "CETE" (Certification and Testing) indicating the certification and the material has been examined and it is believed that the certification is applicable and that the material conforms to contract requirements.
106.20.5 Laboratory Reports
Acceptance or rejection of a material is based on Laboratory and/or field tests or Laboratory and/or field tests and certifications. If a certification is used as a basis for acceptance, this shall be reported under Acceptance Method as "CETE", indicating that, based on the certification and test results, the material represented conforms to contract requirements. Upon request, a Laboratory report form, showing the results obtained on a sample, can be printed from AWP and distributed to those members of MoDOT who are concerned with the use of the material. The Laboratory report forms are intended only for interdepartmental use, and test results are not reported on these forms to persons outside MoDOT. When necessary, test results will be reported by letter to persons outside MoDOT.
All inquires concerning test results of samples being tested or previously tested; whether from producers, contractors, or highway personnel from other sections within the department; should be directed to the Laboratory through the district Construction and Materials office or Construction and Materials.
When printed using AWP, test results on a sample are reported in the body of the Laboratory report form. The status, regarding acceptance, rejection, or use of the material represented, will be found on the lower part of the report form under "Standard Remarks" provided the appropriate Sample Status was indicated in the report.
106.20.6 Material Transfer Reports
When there is an excess of material reported to one contract that needs to be reported to a different contract(s), the contractor must submit a “Material Transfer Request” form to the district responsible for the original contract. Once received, personnel should evaluate the request to ensure the quantity requested to transfer is available. After the request is verified and approved, transfer actions shall be documented by the following steps:
- a. The pertinent sample record(s) should be unauthorized and Remark Type “Materials Transfer” selected. In the Remarks, add the current date, userid of the user responsible for making the changes and a description of the transfer. (E.g. “20200629 – userid - 203 lbs. transferred from 190112-A10 to 190529-A15. Transfer request form stored in eProjects under J1P2209”.)
- b. Modify the sample record “Contract tab” by reducing the quantity reported to original contract and adding the same amount to the new contract added on the same record.
- c. If the transfer request involves a contract outside of the district responsible for the original contract, communication must occur between all districts involved before action is taken.
- d. If the originating contract is closed and locked in AWP, a request to reopen the contract must be sent to redev@modot.mo.gov before the record can be unauthorized. A follow-up email once the sample record has been adjusted and the record reauthorized must also be sent to let them know the contract can be reclosed.
- e. File the original Transfer Request form in eProjects.
106.20.7 Corrected Reports
A corrected report shall be issued for any report that has been printed and distributed and shows incorrect or incomplete sample identification, test results or remarks. The corrected report will:
a) Have the term “corrected report” hand-written or stamped on the report.
b) Explain in the remarks why the corrected report was issued and what correction was made.
c) Be distributed in the same manner as the original.
AWP reports with errors and not yet authorized can be immediately corrected in AWP, making the necessary change and recording the reason under “remarks”. Authorized reports must be corrected with the assistance of Construction and Materials.
106.20.8 Rejected Reports
Reports shall be marked rejected in accordance with Sample Record General Information. If material is rejected and it affects another district, it is important the inspector notify that district of the rejection by telephone or fax. The AWP report shall be marked Status Rejected/Fail. The reason for rejection of the material should be indicated in the Free From Test. If a new sample record is to be made to report the replacement material, the Copy Sample function located under the Services pull down menu can to be used.
106.20.9 Certifications
For reports to "General Construction" in the past, certifications were required to be attached to samples submitted to the laboratory. With the change to reporting electronically via AWP, it is not required to attach these certifications to the sample ID except for emulsions and cutbacks. The certifications should be examined for compliance, initialed and dated in the upper right corner, and a copy sent to the Chemical Laboratory. The copy sent to the Chemical Laboratory may be included with the sample, sent by mail or faxed. This does not change the method of acceptance as required or required monthly reports. If part of the basis of sampling/inspection is by a certification, that certification is to be examined for compliance by the inspector, approved and attached to the original sample ID/report document or marked with the sample ID number, and kept on file in the district. The ID sheet/report document must indicate the physical location of the certification, e.g., "Certification on file in the District # Operation's office." This certification must be readily identifiable and retrievable upon request.
106.20.10 Marking Material
106.20.10.1 Stamps and Markings
When required, the “MoDOT OK” stamp or other marks to be made by MoDOT shall be applied to materials that are inspected and approved in the field. Such marks shall be applied using permanent ink or paint. The circular stamp shall have a 1.5 (±0.25) in. diameter. The impression shall include the outline of the State of Missouri with the word “OK” and the district number included within the outline. The word “MoDOT” shall also be on the stamp and located beneath the outline of the state. Existing district stamps that are serviceable, whether or not they comply, may be used until such time as new stamps are purchased. When stamping is not required for a particular material but the material has been inspected and approved and the material has a surface suitable for stamping, stamping or placing the sample ID on the material in accordance with these instructions is encouraged unless otherwise restricted by the instructions for the particular material. While the presence of the stamp indicates the material has been approved, the absence of the stamp does not indicate anything. The material may have been inspected and approved and it may not have been stamped for a variety of reasons, or the stamp may have weathered away. In these instances, approval of the material should be confirmed by reviewing the available documentation.
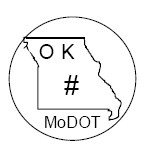
106.20.10.2 Marking Location
All materials that are to be stamped "MoDOT OK" or otherwise marked will be marked at the location designated in the applicable section of the Engineering Policy Guide. If no location is designated, the material will be stamped as indicated below, which are listed in order of preference:
a) Adjacent to any required markings placed by the manufacturer. Far right upper edge of the material as most likely to be viewed by subsequent inspectors.
b) Any obvious location accessible for marking.
106.20.10.3 Obliteration of Mark
When necessary, a MoDOT stamp or marking is to be obliterated using orange paint. Paint use will be limited to that required to clearly indicate that the stamp or marking is considered invalid. When obliterating a MoDOT mark a reasonable effort should be made to avoid defacing the manufacturer's product any more than necessary to indicate to subsequent inspectors that the material is deemed unacceptable for MoDOT use. A small, filled circle of orange paint at the location designated for the MoDOT stamp or other marking indicates that the material did not meet specifications and is rejected, or not acceptable for use.
106.20.11 Internal Material Records
Since it is not always practical to capture all details of a project or inspection in AWP, written documentation of some form may be necessary in addition to capturing data in AWP.
106.20.11.1 Material Diaries
Field personnel shall maintain individual diaries. Diaries shall be in a bound book such as a field book and may be maintained in offices or plants to record significant items for specific types of material. In no case may a diary be kept in loose-leaf form. If an error occurs, it is not to be erased. It shall be corrected by drawing a line through the entry and entering the correct information elsewhere. Explanation of the correction must be shown. All diary entries shall be signed. However, if all entries are made by the same individual, a note at the front of the diary so stating will be acceptable, providing each individual entry is initialed. Completed diaries shall be maintained as a permanent record for at least 11 years. An individual diary shall show the inspector's day-to-day activities and all significant items relating to the inspection performed that day. The diary shall contain the necessary information to support routine reports and provide assurance that the items inspected comply or do not comply with specification requirements. Basic figures needed to compute test results for an item, except those entered in plant diaries or on standard MoDOT forms, such as aggregate workbooks, shall be entered in the inspector's diary. Any pertinent information affecting or influencing the inspection shall be recorded. In some cases, it is advisable to establish diaries pertaining to a particular plant or a particular type of inspection. Information to be entered will be as required by the particular item being inspected or tested.
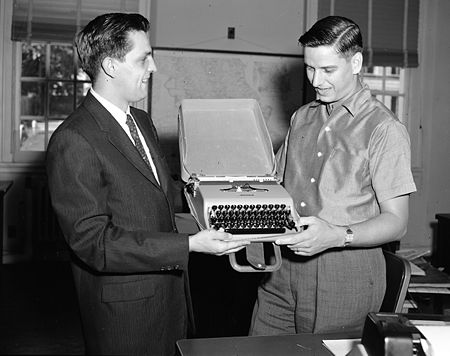
106.20.11.2 Laboratory Workbooks
Laboratory workbooks are to be maintained by Laboratory personnel, as required, to provide support information of all analytical data and calculations, except those entered on prepared MoDOT forms. These workbooks may be individual or office items depending on the materials to be tested. All workbooks shall be identified by either the name of the individual or the type of material involved. This information will be collected and filed annually and maintained for at least 10 years.
106.20.11.3 Laboratory Workcards
Laboratory workcards have been designed to facilitate the recording of test data, computations, and results not recorded in AWP. These forms shall be used where applicable, and the individual performing the testing shall initial the form. When additional sheets are required, they shall be securely attached to the form and considered as an integral portion of the form. After the materials have been reported, the workcards will be filed and maintained in the Laboratory for three years and then transferred to Central Office archives for a period of five years.
106.20.11.4 Material File Retention
Project-specific material files will be maintained in the eProjects Record Center. The files stored in eProjects are archived for a total of 11 years following final acceptance of the job.
106.20.11.5 Important Correspondence
All important correspondences, including circular letters, are to be retained indefinitely or until the information is available by an alternate means (e.g. it has been included in the Engineering Policy Guidelines). All other correspondence may be discarded after the retention period deemed necessary by its measure of importance.
106.20.11.6 Materials Survey and Soil Survey
Materials Survey and Soil Survey records are to be retained indefinitely.