606.1 Guardrail: Difference between revisions
mNo edit summary |
→606.1.3.2 End Terminals, Crash Cushions and Anchors: updated per RR3931 |
||
(39 intermediate revisions by 5 users not shown) | |||
Line 17: | Line 17: | ||
===29 in. NCHRP 350 Guardrail System=== | ===29 in. NCHRP 350 Guardrail System=== | ||
<html> | |||
<a style="display:block" href="https://epg.modot.org/files/0/02/606.1.3.1_Guardrail_Length_of_Need_Calculator_Jul_2021.xlsx"> | |||
<div style="float: right; margin-top: 5px; margin-left: 5px; width:300px; background-color: #f5f5f5; border-radius:5px; padding: 0.3em; border: 1px solid #cccccc; text-align:left;"> | |||
<b><u><center>Guardrail Length of Need Calculator</center></u></b> | |||
This file is not compatible with Microsoft Online. You will need to right-click on the link and save the file. | |||
</div> | |||
</a> | |||
</html> | |||
:'''Type A Guardrail''' - single W beam rail with 6 ft. 3 in. post spacing. | :'''Type A Guardrail''' - single W beam rail with 6 ft. 3 in. post spacing. | ||
Line 39: | Line 44: | ||
'''Embedded End Anchor -''' an end anchorage system for guardrail whereby the rail is embedded in a concrete block and buried in the backslope. | '''Embedded End Anchor -''' an end anchorage system for guardrail whereby the rail is embedded in a concrete block and buried in the backslope. | ||
'''MASH –''' AASHTO ''Manual for Assessing Safety Hardware'' ( | '''MASH 2016 –''' AASHTO ''Manual for Assessing Safety Hardware'' (2016), or newer. | ||
'''MASH End Terminal –''' Crashworthy End Terminals that have been approved using the MASH testing requirements. | '''MASH 2016 End Terminal –''' Crashworthy End Terminals that have been approved using the MASH 2016 testing requirements. | ||
'''MGS Guardrail –''' Midwest Guardrail System (MGS) a non-proprietary MASH approved guardrail system. | '''MGS Guardrail –''' Midwest Guardrail System (MGS) a non-proprietary MASH 2016 approved guardrail system. | ||
'''Non-350 Guardrail -''' Existing guardrail that does not meet NCHRP 350 testing requirements. Existing Type A guardrail that is either less than 27 ¾ in. tall, uses steel blockouts, or uses blockouts that are less than 8 in. deep is considered to be Non-350 Guardrail. | '''Non-350 Guardrail -''' Existing guardrail that does not meet NCHRP 350 testing requirements. Existing Type A guardrail that is either less than 27 ¾ in. tall, uses steel blockouts, or uses blockouts that are less than 8 in. deep is considered to be Non-350 Guardrail. | ||
Line 78: | Line 83: | ||
==606.1.3 Guardrail Systems== | ==606.1.3 Guardrail Systems== | ||
Beam guardrail systems are shown in [ | Beam guardrail systems are shown in [https://www.modot.org/media/16856 Std. Plan 606.00] and other standard plans. Strong post W-beam guardrail (MGS, Type A and Type B) and thrie beam guardrail (Type E) are semirigid barriers used predominantly on roadsides. Installed correctly, W-beam laps the rail splices in the direction of the traffic flow, crashworthy end terminals are used and the rail is blocked away from the strong posts. Placement of curb at guardrail installations also requires careful consideration. | ||
The Midwest Guardrail System (MGS) is mounted at a 31 in. rail height, requires blockouts that are 12 in. deep (measured from the rail to the post) and includes rail elements that are spliced between guardrail posts. | The Midwest Guardrail System (MGS) is mounted at a 31 in. rail height, requires blockouts that are 12 in. deep (measured from the rail to the post) and includes rail elements that are spliced between guardrail posts. | ||
Line 104: | Line 109: | ||
:* When it is necessary to replace more than 50% of an existing length of guardrail as a result of slides or extensive damage, the entire length of guardrail is to be removed and replaced with MGS at 31 inches. | :* When it is necessary to replace more than 50% of an existing length of guardrail as a result of slides or extensive damage, the entire length of guardrail is to be removed and replaced with MGS at 31 inches. | ||
:* Some 31 in. proprietary guardrail systems that do not incorporate the use of blockouts have been successfully crash-tested for MASH. The use of this type of system may be appropriate for some applications. Contact the Design Division for further details. | :* Some 31 in. proprietary guardrail systems that do not incorporate the use of blockouts have been successfully crash-tested for MASH 2016. The use of this type of system may be appropriate for some applications. Contact the Design Division for further details. | ||
:* Criteria for guardrail use on [[232.5 Freeways|outer roadways]] are the same as for other roads except for the shoulder side adjacent to a through lane. Guardrail is specified along outer roadways where the outer roadway is 10 ft. or more above the main roadway, and the shoulder of the outer roadway is less than 25 ft. from the top of the roadway backslope. Sometimes it is more economical to move the outer roadway back sufficiently to eliminate the requirement for guardrail. Guardrail along outer roadways is installed with the face of the rail toward the outer roadway. Double faced MGS may be required if the guardrail is within the limits of the clear zone for the through lanes. | :* Criteria for guardrail use on [[232.5 Freeways|outer roadways]] are the same as for other roads except for the shoulder side adjacent to a through lane. Guardrail is specified along outer roadways where the outer roadway is 10 ft. or more above the main roadway, and the shoulder of the outer roadway is less than 25 ft. from the top of the roadway backslope. Sometimes it is more economical to move the outer roadway back sufficiently to eliminate the requirement for guardrail. Guardrail along outer roadways is installed with the face of the rail toward the outer roadway. Double faced MGS may be required if the guardrail is within the limits of the clear zone for the through lanes. | ||
Line 120: | Line 125: | ||
:* On projects where no roadway widening is proposed and the minimum 2 ft. shoulder widening behind the barrier is not practicable, the 8 ft. MGS long post design should be used. A cost analysis should be conducted to determine whether to add the 2 ft. shoulder widening or use 8 ft. MGS long post design. For fill slopes steeper than 1V:2H (2:1), the use of special designs are necessary. Contact the Design Division for further details. | :* On projects where no roadway widening is proposed and the minimum 2 ft. shoulder widening behind the barrier is not practicable, the 8 ft. MGS long post design should be used. A cost analysis should be conducted to determine whether to add the 2 ft. shoulder widening or use 8 ft. MGS long post design. For fill slopes steeper than 1V:2H (2:1), the use of special designs are necessary. Contact the Design Division for further details. | ||
:* MASH end terminals at 31 in. height will require a height and lateral transition for connection to existing non-MGS guardrail. The plans will need to include a 25 ft. MGS Transition Section between the MASH end terminal and the existing or modified guardrail. | :* MASH 2016 end terminals at 31 in. height will require a height and lateral transition for connection to existing non-MGS guardrail. The plans will need to include a 25 ft. MGS Transition Section between the MASH 2016 end terminal and the existing or modified guardrail. | ||
:* Adjustment of guardrail height should be performed in accordance with the guidance provided in the [ | :* Adjustment of guardrail height should be performed in accordance with the guidance provided in the [https://epg.modot.org/files/2/27/606_Adjusting_Low_Guradrail.pdf Assessment of Existing G4(1S) Strong Post Guardrail (Rail)]. The minimum guardrail height after adjusting/replacing blocks is 27 ¾ inches. If the 27 ¾ in. height will not be achieved, the guardrail must be replaced with MGS. A non-standard job special provision for height adjustment is available. | ||
:* In areas of a roadway cut section, or where the road is transitioning from cut to fill, designers may consider the application of an embedded terminal. Often this can be accomplished by extending the guardrail beyond the length of need to tie the guardrail into the backslope. When properly designed and located, this type of anchor provides full shielding for the identified hazard, eliminates the possibility of an end-on impact with the terminal, and minimizes the likelihood of the vehicle passing behind the rail. | :* In areas of a roadway cut section, or where the road is transitioning from cut to fill, designers may consider the application of an embedded terminal. Often this can be accomplished by extending the guardrail beyond the length of need to tie the guardrail into the backslope. When properly designed and located, this type of anchor provides full shielding for the identified hazard, eliminates the possibility of an end-on impact with the terminal, and minimizes the likelihood of the vehicle passing behind the rail. | ||
Line 130: | Line 135: | ||
:* The use of curb in conjunction with guardrail is discouraged. When used in conjunction with MGS, an acceptable option is to place up to a 6 in. high curb at a maximum 6 in. offset outside the face of the rail at any posted speed. Where barrier curb is used, guardrail is placed with the guardrail face located at the face of the curb and the top of the rail is located 31 in. above the pavement elevation at the curb face. Where mountable curb is used, guardrail is placed with the face at the edge of the usable shoulder and the top of the rail is located 31 in. above the shoulder elevation. Where curb and gutter is used, guardrail is placed with the guardrail face at the face of curb and the top of the rail at 31 in. above the gutter flow line. | :* The use of curb in conjunction with guardrail is discouraged. When used in conjunction with MGS, an acceptable option is to place up to a 6 in. high curb at a maximum 6 in. offset outside the face of the rail at any posted speed. Where barrier curb is used, guardrail is placed with the guardrail face located at the face of the curb and the top of the rail is located 31 in. above the pavement elevation at the curb face. Where mountable curb is used, guardrail is placed with the face at the edge of the usable shoulder and the top of the rail is located 31 in. above the shoulder elevation. Where curb and gutter is used, guardrail is placed with the guardrail face at the face of curb and the top of the rail at 31 in. above the gutter flow line. | ||
:* When an obstacle such as a culvert headwall is located close to the shoulder line, the MGS long-span section can be used to span up to 25 feet. | :* When an obstacle such as a culvert headwall is located close to the shoulder line, the MGS long-span section can be used to span up to 25 feet. When obstacles are to be marked with a [[903.17 Delineation and Object Markers|Type 3 Object Marker]], it shall be in accordance with [[903.17 Delineation and Object Markers#903.17.4 Object Markers for Obstructions Adjacent to the Roadway (MUTCD Section 2C.65)|EPG 903.17.4 Object Markers for Obstructions Adjacent to the Roadway]]. | ||
:* Guardrail should be used to protect traffic from non-breakaway signposts, sign trusses and bridge piers within the clear zone. Typical treatments are indicated in the standard plans. Bridge piers located close to the roadway are marked with a Type 2 Object Marker. | :* Guardrail should be used to protect traffic from non-breakaway signposts, sign trusses and bridge piers within the clear zone. Typical treatments are indicated in the standard plans. Bridge piers located close to the roadway are marked with a Type 2 Object Marker. | ||
Line 136: | Line 141: | ||
:* Guardrail is usually galvanized and has a silver color. It can also be provided in weathering steel that has a brown or rust color. Along Scenic Byways, at scenic overlooks, state highways through national forests, or other designated areas where aesthetic guardrail is needed, consider using weathering steel guardrail, colored terminals (powder-coated galvanized steel), colored steel posts (galvanized weathering steel or powder-coated galvanized steel) or wood posts to minimize the barrier’s visual impact. Funding for the increased cost of aesthetic guardrail should come from the local public agency or other outside sources. If a specific appearance is deemed appropriate in order to coordinate with existing facilities or some other aspect of the scenic location, the designer is to specify the system desired with a job special provision. | :* Guardrail is usually galvanized and has a silver color. It can also be provided in weathering steel that has a brown or rust color. Along Scenic Byways, at scenic overlooks, state highways through national forests, or other designated areas where aesthetic guardrail is needed, consider using weathering steel guardrail, colored terminals (powder-coated galvanized steel), colored steel posts (galvanized weathering steel or powder-coated galvanized steel) or wood posts to minimize the barrier’s visual impact. Funding for the increased cost of aesthetic guardrail should come from the local public agency or other outside sources. If a specific appearance is deemed appropriate in order to coordinate with existing facilities or some other aspect of the scenic location, the designer is to specify the system desired with a job special provision. | ||
Guardrail details and typical locations for installation are shown in the standard plans. Guardrail is shown by proper legend on the plan sheets and the station location and quantities are tabulated on the 2B sheets. Quantities are tabulated in 12 ft. 6 in. increments. Curved sections of guardrail are to be installed on curves with a radius of 150 ft. or less. The plans specify the lengths of curved guardrail and the radius of curvature. Curved guardrail is not tabulated separately on the plans. Examples of [ | Guardrail details and typical locations for installation are shown in the standard plans. Guardrail is shown by proper legend on the plan sheets and the station location and quantities are tabulated on the 2B sheets. Quantities are tabulated in 12 ft. 6 in. increments. Curved sections of guardrail are to be installed on curves with a radius of 150 ft. or less. The plans specify the lengths of curved guardrail and the radius of curvature. Curved guardrail is not tabulated separately on the plans. Examples of [https://epg.modot.org/index.php?title=620.5_Delineators_%28MUTCD_Chapter_3F%29#620.5.5_Guardrail_Delineation guardrail delineation] and tabulation are shown in [https://epg.modot.org/files/0/0a/235_Sample_Preliminary_Plans.pdf Sample Plans]. | ||
'''Fill Slopes''' | '''Fill Slopes''' | ||
Line 156: | Line 161: | ||
:* W-beam guardrail barrier | :* W-beam guardrail barrier | ||
:* Concrete barrier. | :* Concrete barrier. | ||
<div id="Length of Need"></div> | |||
'''Length of Need''' | '''Length of Need''' | ||
<html> | |||
<a style="display:block" href="https://epg.modot.org/files/0/02/606.1.3.1_Guardrail_Length_of_Need_Calculator_Jul_2021.xlsx"> | |||
<div style="float: right; margin-top: 5px; margin-left: 5px; width:300px; background-color: #f5f5f5; border-radius:5px; padding: 0.3em; border: 1px solid #cccccc; text-align:left;"> | |||
<b><u><center>Guardrail Length of Need Calculator</center></u></b> | |||
The length of guardrail needed to shield a fixed feature (length of need) is dependent on the location and geometrics of the object, direction(s) of traffic, posted speed, traffic volume, and type and location of traffic barrier. The length of need and the flare rate of the guardrail shall be determined in accordance with the procedures contained in | This file is not compatible with Microsoft Online. You will need to right-click on the link and save the file. | ||
</div> | |||
</a> | |||
</html> | |||
The length of guardrail needed to shield a fixed feature (length of need) is dependent on the location and geometrics of the object, direction(s) of traffic, posted speed, traffic volume, and type and location of traffic barrier. The length of need and the flare rate of the guardrail shall be determined in accordance with the procedures contained in Sections 5.6.3 and 5.6.4 of the ''AASHTO Roadside Design Guide''. The general geometric data covering the length of need are illustrated on Figure 5.39 of the Roadside Design Guide. | |||
Guardrail protection for fixed objects such as trees or utility poles may be necessary. If this protection is required, the protection is determined from the near lane on one-direction roadways and from both lanes on a two-direction roadway. Guardrail is warranted in advance of any fixed object located within the clear zone provided the object is potentially more damaging than the guardrail if struck by a vehicle and the object cannot be economically removed, relocated, or made crashworthy by means of breakaway type construction. When designing a barrier for a fill slope, the length of need begins at the point where the need for barrier is recommended. | Guardrail protection for fixed objects such as trees or utility poles may be necessary. If this protection is required, the protection is determined from the near lane on one-direction roadways and from both lanes on a two-direction roadway. Guardrail is warranted in advance of any fixed object located within the clear zone provided the object is potentially more damaging than the guardrail if struck by a vehicle and the object cannot be economically removed, relocated, or made crashworthy by means of breakaway type construction. When designing a barrier for a fill slope, the length of need begins at the point where the need for barrier is recommended. | ||
Line 224: | Line 235: | ||
<div id="During the project development process"></div> | <div id="During the project development process"></div> | ||
During the project development process, use the following guidance to determine the guardrail improvements for your project. | During the project development process, use the following guidance to determine the guardrail improvements for your project. | ||
:* Use MASH crashworthy end terminals for exposed ends of all new runs of guardrail on all routes | :* Use MASH 2016 crashworthy end terminals for exposed ends of all new runs of guardrail on all routes. | ||
:::* On dual lane facilities, guardrail end terminals are to be upgraded with MASH 2016 crashworthy end terminals in both directions even if the project covers only rehabilitation of the roadway in one direction. | |||
:::* On dual lane facilities, guardrail end terminals are to be upgraded with MASH crashworthy end terminals in both directions even if the project covers only rehabilitation of the roadway in one direction. | |||
:* On major routes, replace all existing Pre-350 and 350 end terminals with MASH crashworthy end terminals. | :* On major routes, replace all existing Pre-350 and 350 end terminals with MASH crashworthy end terminals. | ||
:::* Downstream Pre-350 and 350 end terminals outside of the major route clear zone may remain in place as long as the terminal provides sufficient anchorage to the guardrail system. | :::* Downstream Pre-350 and 350 end terminals outside of the major route clear zone may remain in place as long as the terminal provides sufficient anchorage to the guardrail system. | ||
:::* End terminals within the limits of ramps will be upgraded to MASH crashworthy end terminals. Improvements to existing guardrail that extends beyond the limits of the ramp onto the crossing route will be up to the judgment of the engineer of record. | :::* End terminals within the limits of ramps will be upgraded to MASH 2016 crashworthy end terminals. Improvements to existing guardrail that extends beyond the limits of the ramp onto the crossing route will be up to the judgment of the engineer of record. | ||
:* On major routes, guardrail or concrete barrier blunt ends located on either side of a two-way roadway or on the guardrail approach end of dual lane facilities must be replaced with a MASH crashworthy end terminal even if the project covers only rehabilitation of the roadway in one direction. | :* On major routes, guardrail or concrete barrier blunt ends located on either side of a two-way roadway or on the guardrail approach end of dual lane facilities must be replaced with a MASH 2016 crashworthy end terminal even if the project covers only rehabilitation of the roadway in one direction. | ||
:* Median Pier Protection: All undamaged bullnose systems may remain in place. Any Pre-350 and 350 end terminals (not protected by guard cable) and Non-350 Guardrail on median pier protection systems shall be replaced with MASH approved end terminals and MGS guardrail. | :* Median Pier Protection: All undamaged bullnose systems may remain in place. Any Pre-350 and 350 end terminals (not protected by guard cable) and Non-350 Guardrail on median pier protection systems shall be replaced with MASH 2016 approved end terminals and MGS guardrail. | ||
:* On minor routes, damaged end terminals shall be replaced with MASH crashworthy end terminals. | :* On minor routes, damaged end terminals shall be replaced with MASH 2016 crashworthy end terminals. | ||
:* On minor routes, existing end terminals (in serviceable condition) may be left in place. Engineering judgment in accordance with AASHTO’s Roadside Design Guide and crash history should be used to determine guardrail improvements for each project. | :* On minor routes, existing end terminals (in serviceable condition) may be left in place. Engineering judgment in accordance with AASHTO’s Roadside Design Guide and crash history should be used to determine guardrail improvements for each project. | ||
'''Grading for New Roadway Construction.''' When an end terminal falls within the limits of an area that includes construction of a new roadbed, provide the needed embankment (cut/fill) quantities to construct the Standard Grading Limits shown in [https://www.modot.org/media/16869 Standard Plan 606.81] and include that volume in the model. Indicate in the Summary of Quantities for Crashworthy End Terminals that “Standard Grading Limits” are required and that payment is included in the embankment quantities. | |||
See ''Roadside Design Guide 4th Edition 2011'', Chap. 8.3.3 (pages 8-4, 5, 6 and 7), for further information on grading. On projects without earthwork pay items, Class III shaping slopes shall be used to provide the flat recovery area. | |||
'''Grading for Existing Roadbeds.''' When end terminals are to be installed on an existing roadway, an evaluation of each location should be made to determine if an existing platform is already in place that meets the Standard Grading Limits shown in [https://www.modot.org/media/16869 Std. Plan 606.81]. If a sufficient platform does exist, indicate in the Summary of Quantities for Crashworthy End Terminals that no grading is necessary. | |||
If an existing platform does not exist, or is insufficient, evaluate the existing terrain and determine whether the Standard Grading Limits can reasonably be constructed with Shaping Slopes Class III without creating an excessively steep in-slope or blocking the ditch with fill (that is, project scope generally does not include purchasing new right of way and/or making significant alterations to the existing in-slopes/back-slopes/ditches). For most existing locations, retrofitting the terrain to meet the Standard Grading Limits is not feasible, but if it is, indicate in the Summary of Quantities for Crashworthy End Terminals that Standard Grading Limits are required and include the necessary quantities for Shaping Slopes Class III. | |||
If it is not practical to construct the Standard Grading Limits but Alternate Grading Limits can reasonably be constructed, indicate in the Summary of Quantities for Crashworthy End Terminals that “Alternate Grading Limits” are required and include the necessary quantities for Shaping Slopes Class III. This is the most common option for existing roadways. | |||
Shaping Slopes Class III should not be used if the existing terrain requires significant quantities of fill. When significant grading is required, other grading pay items should be used with specific volumetric quantities to provide the flat recovery area. | |||
If the existing terrain is such that Alternate Grading Limits cannot be reasonably constructed within the project scope, a design exception may be necessary. | |||
See ''Roadside Design Guide 4th Edition 2011'', Chap. 8.3.3 (pages 8-4, 5, 6 and 7), for further information on grading. | |||
'''Bridge End Treatment''' | '''Bridge End Treatment''' | ||
Line 251: | Line 277: | ||
An embedded terminal is designed to terminate the guardrail by burying the end in a backslope. The embedded terminal is the preferred terminal because it eliminates the exposed end of the guardrail. The embedded terminal uses a concrete block anchor or embedded steel post to develop the tensile strength in the guardrail. The backslope needed to install an embedded terminal is to be 1V:3H (3:1) or steeper and at least 4 ft. above the roadway. The entire embedded terminal can be used within the length of need for backslopes of 1V:1H (1:1) or steeper if the barrier remains at full height in relation to the roadway shoulder to the point where the barrier enters the backslope. For backslopes between 1V:1H (1:1) and 1V:3H (3:1), design the length of need beginning at the point where the W-beam remains at full height in relation to the roadway shoulder usually beginning at the point where the barrier crosses the ditch line. If the backslope is flatter than 1:1, provide a minimum 20-ft. wide by 75 ft. long distance behind the barrier and between the beginning length of need point at the terminal end to the mitigated object to be protected. | An embedded terminal is designed to terminate the guardrail by burying the end in a backslope. The embedded terminal is the preferred terminal because it eliminates the exposed end of the guardrail. The embedded terminal uses a concrete block anchor or embedded steel post to develop the tensile strength in the guardrail. The backslope needed to install an embedded terminal is to be 1V:3H (3:1) or steeper and at least 4 ft. above the roadway. The entire embedded terminal can be used within the length of need for backslopes of 1V:1H (1:1) or steeper if the barrier remains at full height in relation to the roadway shoulder to the point where the barrier enters the backslope. For backslopes between 1V:1H (1:1) and 1V:3H (3:1), design the length of need beginning at the point where the W-beam remains at full height in relation to the roadway shoulder usually beginning at the point where the barrier crosses the ditch line. If the backslope is flatter than 1:1, provide a minimum 20-ft. wide by 75 ft. long distance behind the barrier and between the beginning length of need point at the terminal end to the mitigated object to be protected. | ||
For new installations, flare the guardrail to the foreslope/backslope intersection using a flare rate that meets the criteria in [ | For new installations, flare the guardrail to the foreslope/backslope intersection using a flare rate that meets the criteria in [https://www.modot.org/media/16860 Standard Plan 606.30] and or [https://www.modot.org/media/16868 Standard Plan 606.80]. Provide a 1V:4H (4:1) or flatter foreslope into the face of the guardrail and maintain the full guardrail height to the foreslope/backslope intersection in relation to a 1V:10H (10:1) line extending from edge of shoulder breakpoint. | ||
For rock cuts with a smooth face, a rock face guardrail anchor is the preferred terminal. This option should not be used on rock cuts with a rough face that might cause vehicle snagging rather than providing relatively smooth redirection. | For rock cuts with a smooth face, a rock face guardrail anchor is the preferred terminal. This option should not be used on rock cuts with a rough face that might cause vehicle snagging rather than providing relatively smooth redirection. | ||
Line 257: | Line 283: | ||
'''Crashworthy End Terminals and Crash Cushions''' | '''Crashworthy End Terminals and Crash Cushions''' | ||
If an embedded terminal or rock face anchor cannot be installed, consider a crashworthy end terminal and crash | If an embedded terminal or rock face anchor cannot be installed, consider installing a crashworthy end terminal and/or crash cushion. Crashworthy end terminals and crash cushions are devices used to provide an acceptable level of safety to the end of a roadside barrier or fixed object. Such treatment is required because of the serious consequences that may result from a vehicle impacting an unprotected barrier or object. An unprotected barrier or object can cause an impacting vehicle to abruptly stop, become unstable or roll; it can even penetrate the passenger compartment, all of which increase the risk of injury to the vehicle’s occupants. | ||
End terminals or crash cushions that have met the safety requirements contained in MASH 2016 are deemed crashworthy and must be listed as eligible for use on the [https://epg.modot.org/index.php/Category:123_Federal-Aid_Highway_Program#123.1.1_FHWA_Oversight_-_National_Highway_System NHS] by FHWA. MoDOT then reviews these items and makes a determination of their use on Missouri’s state-owned roadways. Refer to [http://www.modot.org/business/standards_and_specs/endterminals.htm MoDOT’s End Terminals, Crash Cushions and Barrier Systems website] for more information on approved crashworthy end terminals. | |||
While crashworthy end terminals do not | While crashworthy end terminals do not require an offset at the end, a flare is recommended so the end piece does not protrude into the shoulder. These terminals may have a 2 ft. offset to the first post. Four feet of widening is needed at the end posts to properly anchor the system. When widening includes an embankment, fill material will be necessary for optimum terminal performance. (See Standard Plan 606.30 for widening details.) When the entire barrier run is located farther than 12 ft. beyond the shoulder break point and the slopes are greater than 1V:10H (10:1) and 1V:6H (6:1) or flatter, additional embankment at the terminal is not needed. Crashworthy end terminals located within 10 ft. of the edgeline will be delineated with a Type 3 Modified Object Marker. | ||
Currently, there is not a MASH 2016 approved flared-end terminal system. However, if a flared-end terminal is needed, there are NCRHP 350 systems available. These designs include an anchor for developing the tensile strength of the guardrail. The length of need begins at the third post for two approved flared terminals. When a flared terminal is specified, it is critical the embankment quantity also be specified so the area around the terminal can be constructed as shown in the standard plans. | |||
{|style="padding: 0.3em; margin-left:7px; border:2px solid #a9a9a9; text-align:left; font-size: 95%; background:#f5f5f5" width="340px" align="right" | {|style="padding: 0.3em; margin-left:7px; border:2px solid #a9a9a9; text-align:left; font-size: 95%; background:#f5f5f5" width="340px" align="right" | ||
Line 269: | Line 295: | ||
|align="center"|'''Additional information on crashworthy end terminals and internet links to approved terminals''' | |align="center"|'''Additional information on crashworthy end terminals and internet links to approved terminals''' | ||
|- | |- | ||
|align="center"|[ | |align="center"|[https://www.modot.org/end-terminals-crash-cushions-and-barrier-systems MoDOT's end terminal website] | ||
|- | |- | ||
|align="center"|[[:Category:1040 Guardrail, End Terminals, One-Strand Access Restraint Cable and Three-Strand Guard Cable Material#1040.4 Crashworthy End Terminal and Qualified Plastic Guardrail Block|EPG 1040.4 Crashworthy End Terminal and Qualified Plastic Guardrail Block]] | |align="center"|[[:Category:1040 Guardrail, End Terminals, One-Strand Access Restraint Cable and Three-Strand Guard Cable Material#1040.4 Crashworthy End Terminal and Qualified Plastic Guardrail Block|EPG 1040.4 Crashworthy End Terminal and Qualified Plastic Guardrail Block]] | ||
|} | |} | ||
There are five distinct types of end terminals and crash cushions | There are five distinct types of end terminals and crash cushions; Type A, B, C, D and E. This classification aids in the designers’ selection of the appropriate treatment for a given context. It is important to note each of these treatments reduces driver risk to equally acceptable levels and the classifications are based merely on the benefit/cost associated with replacement or repair. | ||
Each type is classified as follows: | |||
'''End Terminals''' | '''End Terminals''' | ||
'''Type A.''' | '''Type A.''' Type A end terminals are treatments used for one-sided barriers such as roadside guardrail or roadside concrete barrier. These devices can also be used on one-sided barriers in [[231.1 Median Width|the median]], provided sufficient clear space is available behind the system to allow opposite direction traffic to recover from an errant path. | ||
'''Crash Cushions''' | '''Crash Cushions''' | ||
'''Type B.''' | '''Type B.''' Type B crash cushions are end treatments used for double-sided barriers, most often in the median. These devices can safely be impacted from several angles including the opposite direction. Type B crash cushions cannot be installed in paved surface locations unless the installation is temporary and the paved area will be resurfaced after the system’s removal. | ||
[[image:606.3.2 Type C.jpg|left|225px||thumb|<center>'''A Type C | [[image:606.3.2 Type C.jpg|left|225px||thumb|<center>'''A Type C Crash Cushion'''</center>]] | ||
'''Type C.''' | '''Type C.''' Type C crash cushions are an end treatment used for double-sided barriers, in gore areas and in the median. Like the Type B, this device can safely be impacted from several angles usually ranging from head-on to the opposite direction. Type C crash cushions, however, may be installed in both paved and unpaved surface locations, but must be installed on an asphalt or concrete pad in non-paved areas. After impact, these crash cushions are usually damaged beyond repair and as such, should be used only in areas where low, annual-impact frequencies are expected. | ||
'''Type D.''' | '''Type D.''' Type D crash cushions have all of the installation and performance parameters of the Type C, but must be at least 80% reusable and have the ability to be reset manually with a moderate amount of repair. Type D crash cushions should be used in gore areas or medians with moderate traffic volumes and where high-impact frequencies are expected. | ||
'''Type E.''' | '''Type E.''' Type E crash cushions have all of the installation and performance parameters of the Type C but must have the ability to reset with little or no manual intervention and have an average cost of repair under $250 per event. Type E crash cushions should be used in gore areas or medians with high traffic volumes and where high-impact frequencies are expected. | ||
Use the following decision matrix to help determine the appropriate end treatment for a given context, not to determine whether or not a barrier or object should be protected. The expected crashes per year are on an average basis: | |||
{| border="1" class="wikitable" style="margin: 1em auto 1em auto" style="text-align:center" | {| border="1" class="wikitable" style="margin: 1em auto 1em auto" style="text-align:center" | ||
Line 309: | Line 325: | ||
!colspan="2"|One-Sided Protection Required!!colspan="6"|Two-Sided Protection Required | !colspan="2"|One-Sided Protection Required!!colspan="6"|Two-Sided Protection Required | ||
|- | |- | ||
|rowspan="2"|Non- | |rowspan="2"|Non-traversable Terrain Beyond the Terminal||rowspan="2"|Traversable Terrain Beyond the Terminal||colspan="2"|Fewer than 0.5 Crashes Per Year Expected||colspan="4"|0.5 or More Crashes Per Year Expected | ||
|- | |- | ||
|Unpaved||Paved or Unpaved||Major ADT <75,000||Minor ADT <30,000||Major ADT ≥75,000||Minor ADT ≥30,000 | |Unpaved||Paved or Unpaved||Major ADT <75,000||Minor ADT <30,000||Major ADT ≥75,000||Minor ADT ≥30,000 | ||
Line 316: | Line 332: | ||
|} | |} | ||
Sand barrels are a crash cushioning system most often used to shield fixed objects that cannot be removed or relocated. | Sand barrels are a crash cushioning system most often used to shield fixed objects that cannot be removed or relocated. Sand barrels are recommended for temporary usage such as in work zones. Conduct a benefit/cost analysis before sand barrels are installed in a permanent application and consult with Maintenance staff. For more information, refer to [[:category:612 Impact Attenuators#612.2 Sand-Filled Impact Attenuators (Sand Barrels)|EPG 612.2 Sand-Filled Impact Attenuators (Sand Barrels)]]. | ||
'''Other Anchor Applications''' | '''Other Anchor Applications''' | ||
End anchors are used to develop the tensile strength of the guardrail at the end of guardrail runs where a crashworthy end terminal is not needed. | |||
====606.1.3.2.1 Crashworthy End Terminals with Curb==== | |||
When curb is present in front of and parallel to a crashworthy end terminal (CET), the potential exists the CET will not perform as designed (i.e. will not redirect the vehicle). When installing CETs, for new construction and roadway upgrades, the need for the curb and the curb height at the location of the CET shall be considered. See [[:Category:749 Hydrologic Analysis|EPG 749 Hydrologic Analysis]] and [[640.1 Pavement Drainage|EPG 640.1 Pavement Drainage]] to calculate the drainage needs in and around CETs. Gutters might be able to be spread out or curb heights reduced in the vicinity of the CET while still accommodating drainage needs and the installation of the CET. Drainage calculations shall be documented in eProjects. | |||
When curb is present in front of and parallel to the CET, the project file should have documentation regarding the design selected and considered in the following priority order: | |||
:1. Eliminate the curb or do not install new curb for the entire length of the CET with an additional 30’-50’ of curb removed upstream of the CET. | |||
:2. Reduce the curb or install new curb to a height of two (2) inches for the entire length of the CET with an additional 30’-50’ upstream of the CET. | |||
:3. Reduce the curb or install new curb to a height of four (4) inches for the entire length of the CET with an additional 30’-50’ upstream of the CET. | |||
If a two-inch curb is not adequate for the drainage needs, a four-inch curb may be installed but is the maximum curb height allowed when installing a CET. | |||
===606.1.3.3 Transitions and Connections=== | ===606.1.3.3 Transitions and Connections=== | ||
Line 328: | Line 354: | ||
'''Bridge Connections''' | '''Bridge Connections''' | ||
Guardrail is placed at bridge ends in accordance with typical locations shown in the standard plans. Guardrail placed for bridge end protection is anchored to the bridge end by | Guardrail is placed at bridge ends in accordance with typical locations shown in the standard plans. Guardrail placed for bridge end protection is anchored to the bridge end by a vertical barrier transition section. Existing bridge end connections that do not conform to current standards are to be considered for replacement or modification. In order to determine the appropriate solution for the specific non-standard bridge end connection, the Bridge Division Liaison Engineer is to be consulted. Where guardrail at the downstream end of a one-way bridge is necessary because of a high fill or other condition, the guardrail is connected to the vertical transition section. | ||
The post spacing for MGS vertical bridge transitions varies from the previous bridge transition sections for Type A guardrail. If an existing bridge anchor section is replaced, an evaluation of the impact to drain basins should be conducted. | The post spacing for MGS vertical bridge transitions varies from the previous bridge transition sections for Type A guardrail. If an existing bridge anchor section is replaced, an evaluation of the impact to drain basins should be conducted. | ||
Line 336: | Line 362: | ||
|<center>'''Additional Information'''</center> | |<center>'''Additional Information'''</center> | ||
|- | |- | ||
|align="center"|[[751.1 Preliminary Design#Common Bridge | |align="center"|[[751.1 Preliminary Design#Common Bridge Barrier and Railing (for Rehabilitations)|Common Bridge Barrier and Railing (for Rehabilitations)]] Table | ||
|} | |} | ||
===606.1.3.4 Median Barrier Selection and Placement === | ===606.1.3.4 Median Barrier Selection and Placement === | ||
Line 348: | Line 375: | ||
In wider medians, the selection of barrier might depend on the slopes in the median. At locations where the median slopes are relatively flat (1V:10H [10:1] or flatter), unrestrained precast concrete barrier, beam guardrail and cable barrier can be used depending on the available deflection distance. At these locations, position the barrier as close to the center as possible so that the recovery distance can be maximized for both directions. There may be a need to offset the barrier from the flow line to avoid impacts to the drainage flow. | In wider medians, the selection of barrier might depend on the slopes in the median. At locations where the median slopes are relatively flat (1V:10H [10:1] or flatter), unrestrained precast concrete barrier, beam guardrail and cable barrier can be used depending on the available deflection distance. At these locations, position the barrier as close to the center as possible so that the recovery distance can be maximized for both directions. There may be a need to offset the barrier from the flow line to avoid impacts to the drainage flow. | ||
In general, cable barrier is recommended with medians that are 30 ft. wide or wider. However, cable barrier may be appropriate for narrower medians if adequate deflection distance exists. Refer to [[606.2 Guard Cable#606.2. | In general, cable barrier is recommended with medians that are 30 ft. wide or wider. However, cable barrier may be appropriate for narrower medians if adequate deflection distance exists. Refer to [[606.2 Guard Cable#606.2.3 Design and Installation Guidelines|EPG 606.2.3 Design and Installation Guidelines]] for design and installation guidelines for cable barriers. Do not use concrete barrier at locations where the foreslope into the face of the barrier is steeper than 1V:10H (10:1). | ||
At locations where the roadways are on independent alignments and there is a difference in elevation between the roadways, the slope from the upper roadway might be steeper than 1V:6H (6:1). In these locations, position the median barrier along the upper roadway and provide deflection and offset distance as discussed previously. Barrier is generally not needed along the lower roadway except where there are fixed features in the median. When W-beam barrier is placed in a median as a countermeasure for cross-median crashes, design the barrier to be struck from either direction of travel. For example, the installation of beam guardrail might be double-sided. | At locations where the roadways are on independent alignments and there is a difference in elevation between the roadways, the slope from the upper roadway might be steeper than 1V:6H (6:1). In these locations, position the median barrier along the upper roadway and provide deflection and offset distance as discussed previously. Barrier is generally not needed along the lower roadway except where there are fixed features in the median. When W-beam barrier is placed in a median as a countermeasure for cross-median crashes, design the barrier to be struck from either direction of travel. For example, the installation of beam guardrail might be double-sided. | ||
Line 360: | Line 387: | ||
'''Bullnose Guardrail System''' | '''Bullnose Guardrail System''' | ||
[[image:606.1.3.3.jpg|right|280px]] | [[image:606.1.3.3.jpg|right|280px]] | ||
The bullnose guardrail system may be used in the medians of expressways or freeways to shield drivers from hazards, such as bridge piers and other obstacles. It is not a crashworthy end terminal, but is rather a non-gating barrier principally constructed of Type E guardrail. As long as the median’s vertical differences are minimal or can be minimized through grading, the bullnose guardrail system is an appropriate treatment for new construction. This system requires at least 15 ft. of median width for its construction. The bullnose guardrail system is not to be erected between twin bridges. Alternatives are available for twin bridge protection in [ | The bullnose guardrail system may be used in the medians of expressways or freeways to shield drivers from hazards, such as bridge piers and other obstacles. It is not a crashworthy end terminal, but is rather a non-gating barrier principally constructed of Type E guardrail. As long as the median’s vertical differences are minimal or can be minimized through grading, the bullnose guardrail system is an appropriate treatment for new construction. This system requires at least 15 ft. of median width for its construction. The bullnose guardrail system is not to be erected between twin bridges. Alternatives are available for twin bridge protection in [https://www.modot.org/media/16857 Standard Plan 606.01]. Consult [https://www.modot.org/media/16860 Standard Plan 606.30] for grading requirements and other important details. | ||
===606.1.3.5 Closures of Existing Streets, Roads, Bridges or Non-Traversable Roads=== | ===606.1.3.5 Closures of Existing Streets, Roads, Bridges or Non-Traversable Roads=== | ||
====606.1.3.5.1 Closures of Existing Streets and Roads==== | ====606.1.3.5.1 Closures of Existing Streets and Roads==== | ||
When closing a street or road, either Type 4 Object Markers only or a combination of Type 4 Object Markers and Type D guardrail | When closing a street or road, use either Type 4 Object Markers only or a combination of Type 4 Object Markers and Type D guardrail as shown in Figs. 606.1.3.5.1.1 and 606.1.3.5.1.2. Where no hazard exists beyond the end of the closed street or road for a reasonable distance, Type 4 Object Markers are sufficient for delineation. Where a hazard exists beyond the end of the closed street or road that is considered equal to or greater than that created by the use of guardrail (for example a removed bridge or culvert, or a structurally deficient bridge), a combination of both Type 4 Object Markers and Type D guardrail is specified. Refer to [https://www.modot.org/media/16856 Standard Plan 606.00 Guardrail] and [https://www.modot.org/media/16921 Standard Plan 903.03 Sign Mounting Details]. | ||
[[image:606.1.3.10.1.jpg|center|700px]] | [[image:606.1.3.10.1.jpg|center|700px]] | ||
Line 373: | Line 400: | ||
|} | |} | ||
Additional emphasis of a sign barricade may be required for horizontal and vertical alignment of the roadway and at tee intersections as shown in Fig. 606.1.3.5.1.3. Location and installation guidelines for sign barricades are located in [[903.6 Warning Signs#903.6. | Additional emphasis of a sign barricade may be required for horizontal and vertical alignment of the roadway and at tee intersections as shown in Fig. 606.1.3.5.1.3. Location and installation guidelines for sign barricades are located in [[903.6 Warning Signs#903.6.53 Sign Barricades (MUTCD Section 2B.67)|EPG 903.6.53 Sign Barricades]], and [https://www.modot.org/media/16920 Standard Plan 903.02 Highway Signing Structure Signs]. | ||
[[image:606.1.3.10.3.jpg|center|350px]] | [[image:606.1.3.10.3.jpg|center|350px]] | ||
Line 386: | Line 413: | ||
Restoration of the bridges and roadways may be delayed due to scheduling constraints or budget costs of projects. District personnel and Central Office Bridge Division personnel should discuss the schedule to repair the bridge. District personnel and Central Office Construction/Material Geotechnical personnel should discuss the schedule to repair the roadway. Based on the repair schedule, the district will determine the type of closure needed for the bridge or roadway. | Restoration of the bridges and roadways may be delayed due to scheduling constraints or budget costs of projects. District personnel and Central Office Bridge Division personnel should discuss the schedule to repair the bridge. District personnel and Central Office Construction/Material Geotechnical personnel should discuss the schedule to repair the roadway. Based on the repair schedule, the district will determine the type of closure needed for the bridge or roadway. | ||
For bridge and/or roadway closures, bridge/roadways shall be closed according to [[616.8 Typical Applications (MUTCD 6H)#616.8.1 Listing of Typical Applications|typical application]] EPG 616.8.8 (TA-8) Highway Closure – MT, EPG 616.8.8 (TA-8) Highway Closure – DE/CM, EPG 616.8.8a (TA-8a) Closure of Existing Bridges or Non-Traversable Roads, [ | For bridge and/or roadway closures, bridge/roadways shall be closed according to [[616.8 Typical Applications (MUTCD 6H)#616.8.1 Listing of Typical Applications|typical application]] EPG 616.8.8 (TA-8) Highway Closure – MT, EPG 616.8.8 (TA-8) Highway Closure – DE/CM, EPG 616.8.8a (TA-8a) Closure of Existing Bridges or Non-Traversable Roads, [https://www.modot.org/media/16856 Standard Plan 606.00 Guardrail] and [https://www.modot.org/media/16921 Standard Plan 903.03 Sign Mounting Details]. | ||
Figs. 606.1.3.5.2.1 and 606.1.3.5.2.2 are examples of the recommended installation of the bridge/roadway closures based on EPG 616.8.8a Closure of Existing Bridges or Non-Traversable Roads. | Figs. 606.1.3.5.2.1 and 606.1.3.5.2.2 are examples of the recommended installation of the bridge/roadway closures based on EPG 616.8.8a Closure of Existing Bridges or Non-Traversable Roads. | ||
Line 412: | Line 439: | ||
==606.1.4 Maintenance Planning Guidelines for Guardrail== | ==606.1.4 Maintenance Planning Guidelines for Guardrail== | ||
'''Printable''' [ | '''Printable''' [https://epg.modot.org/forms/general_files/MT/R227_update-guardrails.pdf '''Maintenance Planning Guideline for Guardrail''']. | ||
Index of all [[:Category:170 Maintenance Activity Planning Guidelines#Index of Printable Planning Guides|Maintenance Planning Guidelines]]. | Index of all [[:Category:170 Maintenance Activity Planning Guidelines#Index of Printable Planning Guides|Maintenance Planning Guidelines]]. |
Revision as of 15:05, 6 September 2024
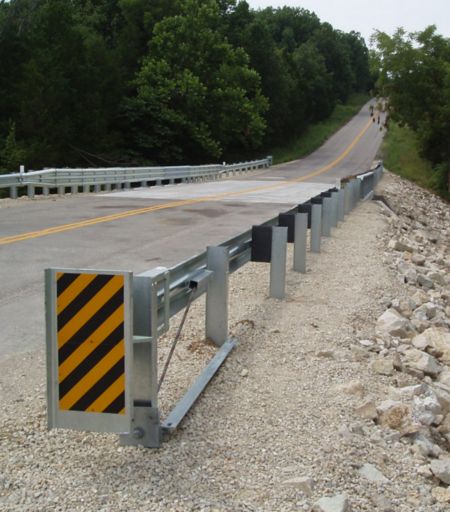
606.1.1 Types of Guardrail
31 in. Midwest Guardrail System
- MGS Guardrail 6 ft. Posts - single W beam rail with 6 ft. 3 in. post spacing.
- MGS Guardrail 8 ft. Posts - single W beam rail with 6 ft. 3 in. post spacing.
- MGS Double Faced Guardrail - double W beam rail (single beam on each side of post) with 6 ft. 3in. post spacing, generally for use in median.
- MGS Guardrail 6 ft. Post, 3 ft. 1-½ in. spacing - single W beam rail with 3 ft. 1-1/2 in. post spacing.
- MGS Guardrail 6 ft. Post, 1 ft. 6-¾ in. spacing - single W beam rail with 1 ft. 6-3/4 in. post spacing.
- MGS Long Span 6 ft. Posts – a single W beam rail system with modifications to omit certain posts at drainage culverts and small bridges.
29 in. NCHRP 350 Guardrail System
- Type A Guardrail - single W beam rail with 6 ft. 3 in. post spacing.
- Type B Guardrail - double W beam rail (single beam on each side of post) with 6 ft. 3in. post spacing, generally for use in median.
- Type D Guardrail - single W beam rail with 12 ft. 6 in. post spacing for use at end of road or street.
- Type E Guardrail - single thrie beam rail with 3 ft. 1-½ in. post spacing.
606.1.2 Guardrail Terms
Blockout – a spacer block to separate the guardrail beam from the post used on most types of guardrail.
Bullnose Guardrail System – an enclosed guardrail design that wraps a semi-rigid guardrail around a hazard.
End Anchor - a guardrail end device without a buffer end to develop the full strength of the rail system.
Embedded End Anchor - an end anchorage system for guardrail whereby the rail is embedded in a concrete block and buried in the backslope.
MASH 2016 – AASHTO Manual for Assessing Safety Hardware (2016), or newer.
MASH 2016 End Terminal – Crashworthy End Terminals that have been approved using the MASH 2016 testing requirements.
MGS Guardrail – Midwest Guardrail System (MGS) a non-proprietary MASH 2016 approved guardrail system.
Non-350 Guardrail - Existing guardrail that does not meet NCHRP 350 testing requirements. Existing Type A guardrail that is either less than 27 ¾ in. tall, uses steel blockouts, or uses blockouts that are less than 8 in. deep is considered to be Non-350 Guardrail.
Pre-350 End Terminal – Devices that have not been approved by NCHRP 350 test requirements. Examples include Breakaway Cable Terminals (BCT), MELT, Turn-down ends, concrete height transitions and any unprotected blunt ends.
Rock Face End Anchor - an end anchorage system for guardrail whereby the rail is bolted to a rock face.
Warrant for Median Barriers |
These are very short video clips of guardrail crash tests conducted at the Midwest Roadside Safety Facility in Lincoln, Nebraska. The video image is very small (and typically located on the lower left of your screen) unless you click the video's enlarge button. |
A successful pickup test |
A successful pickup test, slow motion |
Another successful pickup test |
Another successful pickup test, rear view |
A successful car test |
An unsuccessful pickup test |
MoDOT cooperates with other states in the Midwest State's Regional Pooled Fund Program to develop and improve new and innovative safety devices. |
606.1.3 Guardrail Systems
Beam guardrail systems are shown in Std. Plan 606.00 and other standard plans. Strong post W-beam guardrail (MGS, Type A and Type B) and thrie beam guardrail (Type E) are semirigid barriers used predominantly on roadsides. Installed correctly, W-beam laps the rail splices in the direction of the traffic flow, crashworthy end terminals are used and the rail is blocked away from the strong posts. Placement of curb at guardrail installations also requires careful consideration.
The Midwest Guardrail System (MGS) is mounted at a 31 in. rail height, requires blockouts that are 12 in. deep (measured from the rail to the post) and includes rail elements that are spliced between guardrail posts.
The MGS offers tolerance for future resurfacings. The MGS allows a 3 in. height tolerance from 31 in. to 28 in. without adjustment of the rail element.
606.1.3.1 Guardrail Selection and Placement
During the project development process, use the following guidance to determine the guardrail improvements for the project:
- Use MGS for new runs of guardrail on all routes. When guardrail is installed along existing shoulders that are 4 ft. or wider, the shoulder width may be reduced by 4 in. to accommodate the 12 in. blockout. For shoulders narrower than 4 ft., long post MGS should be considered.
- On major routes with existing guardrail height at or higher than 27 ¾ in., the guardrail may be used in place.
- On major routes with existing guardrail height lower than 27 ¾ in., replace the run with MGS.
- For existing guardrail height lower than 27 ¾ in. within the limit of ramps, replace the run with MGS.
- Improvements to existing guardrail that extends beyond the limits of the ramp onto the crossing route will be a judgment of the engineer of record.
- On minor routes, existing runs of rail, in serviceable condition, may be left in place. Engineering judgment in accordance with AASHTO’s Roadside Design Guide and crash history should be used to evaluate guardrail needs for each project. Where future overlays are anticipated within the next ten years, use of MGS should be considered.
- On minor routes where any portion of the guardrail run is repaired, moved or modified in any way, the following options are available based upon the height of rail:
- For existing runs with a rail height lower than 24 ¾ in., replace the run with MGS.
- For existing runs in serviceable condition with a rail height lower than 27 ¾ in. but as high or higher than 24 ¾ in., adjust the height to a minimum height of 27 ¾ in. or replace the run with MGS at 31 inches.
- Existing runs with rail height of 27 ¾ in. or greater can be used in place.
- When it is necessary to replace more than 50% of an existing length of guardrail as a result of slides or extensive damage, the entire length of guardrail is to be removed and replaced with MGS at 31 inches.
- Some 31 in. proprietary guardrail systems that do not incorporate the use of blockouts have been successfully crash-tested for MASH 2016. The use of this type of system may be appropriate for some applications. Contact the Design Division for further details.
- Criteria for guardrail use on outer roadways are the same as for other roads except for the shoulder side adjacent to a through lane. Guardrail is specified along outer roadways where the outer roadway is 10 ft. or more above the main roadway, and the shoulder of the outer roadway is less than 25 ft. from the top of the roadway backslope. Sometimes it is more economical to move the outer roadway back sufficiently to eliminate the requirement for guardrail. Guardrail along outer roadways is installed with the face of the rail toward the outer roadway. Double faced MGS may be required if the guardrail is within the limits of the clear zone for the through lanes.
Additional Guidance
- The slope of the area between the edge of the shoulder and the face of the guardrail must be 1V:10H (10:1) or flatter. Do not place guardrail on a fill slope steeper than 1V:6H (6:1).
- Shoulder cross slope may be adjusted during resurfacing in an attempt to use in place existing guardrail (in serviceable condition) that meets current design guidelines. The accepted range in cross-slope for shoulders is 2% to 6%. A tapered shoulder resurfacing to a minimum ½ in. thickness may be considered. A maximum of 8% algebraic difference in the slope of pavement and shoulder at the pavement edge is permitted. If the shoulder surfacing cannot be tapered to minimum thickness without exceeding the maximum cross slope, the shoulder resurfacing will be constructed to the minimum cross slope of 2% and the existing guardrail will be replaced with MGS at 31 inches.
- On the high side of superelevated sections, place guardrail at the edge of shoulder prior to the slope break.
- For guardrail installed at or near the shoulder, 2 ft. of shoulder widening behind the guardrail posts must be provided from the back of the post to the beginning of a fill slope. On existing roadways with less than 2 ft. behind the guardrail, Class III shaping slopes shall be used to widen the shoulder.
- On projects where no roadway widening is proposed and the minimum 2 ft. shoulder widening behind the barrier is not practicable, the 8 ft. MGS long post design should be used. A cost analysis should be conducted to determine whether to add the 2 ft. shoulder widening or use 8 ft. MGS long post design. For fill slopes steeper than 1V:2H (2:1), the use of special designs are necessary. Contact the Design Division for further details.
- MASH 2016 end terminals at 31 in. height will require a height and lateral transition for connection to existing non-MGS guardrail. The plans will need to include a 25 ft. MGS Transition Section between the MASH 2016 end terminal and the existing or modified guardrail.
- Adjustment of guardrail height should be performed in accordance with the guidance provided in the Assessment of Existing G4(1S) Strong Post Guardrail (Rail). The minimum guardrail height after adjusting/replacing blocks is 27 ¾ inches. If the 27 ¾ in. height will not be achieved, the guardrail must be replaced with MGS. A non-standard job special provision for height adjustment is available.
- In areas of a roadway cut section, or where the road is transitioning from cut to fill, designers may consider the application of an embedded terminal. Often this can be accomplished by extending the guardrail beyond the length of need to tie the guardrail into the backslope. When properly designed and located, this type of anchor provides full shielding for the identified hazard, eliminates the possibility of an end-on impact with the terminal, and minimizes the likelihood of the vehicle passing behind the rail.
- Any unconnected or unacceptably connected bridge approach guardrail is to be connected to the bridge by an acceptable transition design.
- The use of curb in conjunction with guardrail is discouraged. When used in conjunction with MGS, an acceptable option is to place up to a 6 in. high curb at a maximum 6 in. offset outside the face of the rail at any posted speed. Where barrier curb is used, guardrail is placed with the guardrail face located at the face of the curb and the top of the rail is located 31 in. above the pavement elevation at the curb face. Where mountable curb is used, guardrail is placed with the face at the edge of the usable shoulder and the top of the rail is located 31 in. above the shoulder elevation. Where curb and gutter is used, guardrail is placed with the guardrail face at the face of curb and the top of the rail at 31 in. above the gutter flow line.
- When an obstacle such as a culvert headwall is located close to the shoulder line, the MGS long-span section can be used to span up to 25 feet. When obstacles are to be marked with a Type 3 Object Marker, it shall be in accordance with EPG 903.17.4 Object Markers for Obstructions Adjacent to the Roadway.
- Guardrail should be used to protect traffic from non-breakaway signposts, sign trusses and bridge piers within the clear zone. Typical treatments are indicated in the standard plans. Bridge piers located close to the roadway are marked with a Type 2 Object Marker.
- Guardrail is usually galvanized and has a silver color. It can also be provided in weathering steel that has a brown or rust color. Along Scenic Byways, at scenic overlooks, state highways through national forests, or other designated areas where aesthetic guardrail is needed, consider using weathering steel guardrail, colored terminals (powder-coated galvanized steel), colored steel posts (galvanized weathering steel or powder-coated galvanized steel) or wood posts to minimize the barrier’s visual impact. Funding for the increased cost of aesthetic guardrail should come from the local public agency or other outside sources. If a specific appearance is deemed appropriate in order to coordinate with existing facilities or some other aspect of the scenic location, the designer is to specify the system desired with a job special provision.
Guardrail details and typical locations for installation are shown in the standard plans. Guardrail is shown by proper legend on the plan sheets and the station location and quantities are tabulated on the 2B sheets. Quantities are tabulated in 12 ft. 6 in. increments. Curved sections of guardrail are to be installed on curves with a radius of 150 ft. or less. The plans specify the lengths of curved guardrail and the radius of curvature. Curved guardrail is not tabulated separately on the plans. Examples of guardrail delineation and tabulation are shown in Sample Plans.
Fill Slopes
Fill slopes can present a risk to an errant vehicle with the degree of severity dependent upon the slope and height of the fill. Providing fill slopes that are 1V:4H (4:1) or flatter can mitigate this condition. If flattening the slope is not feasible or cost-effective, the installation of a barrier might be appropriate. Figs. 5.1 through 5.3 in the AASHTO Roadside Design Guide provide guidelines to determine whether a fill slope constitutes a condition for which a barrier is a cost-effective mitigation. The curves are based on the severity indexes and represent the points where total costs associated with a traffic barrier are equal to the predicted cost of crashes over the service life for selected slope heights without traffic barrier. If the ADT and height of fill intersect on the “Barrier Considered” side of the embankment slope curve, then provide a barrier if flattening the slope is not feasible or cost-effective.
If the figure indicates that barrier is not recommended at an existing slope, that result is not justification for a deviation. For example, if the AADT is 4,000 and the embankment is 10 ft. tall, barrier might be cost-effective for a 1V:2H (2:1) slope, but not for a 1V:2.5H (2.5:1) slope. This process only addresses the potential risk of exposure to the slope. Obstacles on the slope can compound the condition. Where barrier is not cost-effective, use the recovery area formula to evaluate fixed objects on critical fill slopes shorter than 10 feet.
Guardrail is usually not used to protect traffic from headwalls located outside of the shoulder line of roadways without clear zones unless warranted by high fills. Exceptions include interstate safety modification projects where clear zones are not added and where it may not be economically feasible to extend a large box culvert to locate the headwall outside the clear zone point.
For routes under 400 AADT, guardrail for fill slopes is optional, however, good design judgment may require guardrail when conditions warrant.
Cut Slopes
A cut slope is usually less of a risk than a traffic barrier. The exception is a rock cut with a rough face that might cause vehicle snagging rather than providing relatively smooth redirection.
Analyze the potential motorist risk and the benefits of treatment of rough rock cuts located within the Design Clear Zone. Conduct an individual investigation for each rock cut or group of rock cuts. A cost-effectiveness analysis that considers the consequences of doing nothing, removal, smoothing of the cut slope, and other viable options to reduce the severity of the condition can be used to determine the appropriate treatment. Some potential options are:
- W-beam guardrail barrier
- Concrete barrier.
The length of guardrail needed to shield a fixed feature (length of need) is dependent on the location and geometrics of the object, direction(s) of traffic, posted speed, traffic volume, and type and location of traffic barrier. The length of need and the flare rate of the guardrail shall be determined in accordance with the procedures contained in Sections 5.6.3 and 5.6.4 of the AASHTO Roadside Design Guide. The general geometric data covering the length of need are illustrated on Figure 5.39 of the Roadside Design Guide.
Guardrail protection for fixed objects such as trees or utility poles may be necessary. If this protection is required, the protection is determined from the near lane on one-direction roadways and from both lanes on a two-direction roadway. Guardrail is warranted in advance of any fixed object located within the clear zone provided the object is potentially more damaging than the guardrail if struck by a vehicle and the object cannot be economically removed, relocated, or made crashworthy by means of breakaway type construction. When designing a barrier for a fill slope, the length of need begins at the point where the need for barrier is recommended.
When barrier is to be installed on the outside of a horizontal curve, the length of need can be determined graphically. For installations on the inside of a curve, determine the length of need as though it were straight. Also, consider the flare rate, barrier deflection, and barrier end treatment to be used.
When guardrail is placed in a median, consider the potential for impact from opposing traffic when conducting a length of need analysis. When guardrail is placed on either side of objects in the median, consider whether the trailing end of each run of guardrail will shield the leading end of the opposing guardrail. Shield the leading end when it is within the clear zone of opposing traffic. This is also a consideration for outer roads.
Before the actual length of need is determined, establish the lateral distance between the proposed barrier installation and the object shielded. Provide a distance that is greater than or equal to the anticipated deflection of the longitudinal barrier (See standard plans for barrier deflections). Place the barrier as far from the edge of the traveled way as possible while maintaining the deflection distance.
If the end of the length of need is near an adequate cut slope, extend the guardrail and embed it in the slope or attach it to a rock cut. Avoid gaps of 300 feet or less. Short gaps are acceptable when the guardrail is terminated in a cut slope. If the end of the length of need is near the end of an existing barrier, it is recommended that the barriers be connected to form a continuous barrier. Consider maintenance access issues when determining whether or not to connect barriers.
Barrier Deflections
Expect all barriers except rigid barriers (such as concrete bridge rails) to deflect when hit by an errant vehicle. The amount of deflection is primarily dependent on the stiffness of the system. However, vehicle speed, angle of impact, and weight also affect the amount of barrier deflection. For flexible and semirigid roadside barriers, the deflection distance is designed to help prevent the impacting vehicle from striking the object being shielded. For unrestrained rigid systems (unanchored precast concrete barrier), the deflection distance is designed to help prevent the barrier from being knocked over the side of a drop-off or steep fill slope (1V:2H [2:1] or steeper).
In median installations, design systems such that the anticipated deflection will not enter the lane of opposing traffic using deflection values that were determined from crash tests. When evaluating new barrier installations, consider the impacts where significant traffic closures are necessary to accomplish maintenance. Use a rigid system where deflection cannot be tolerated, such as in narrow medians or at the edge of bridge decks or other vertical drop-off areas. Runs of rigid concrete barrier can be cast in place or extruded with appropriate footings.
In some locations where deflection distance is limited, anchor precast concrete barrier. Unless the anchoring system has been designed to function as a rigid barrier, some movement can be expected and repairs may be more expensive. Use of an anchored or other deflecting barrier on top of a retaining wall without deflection distance provided requires approval from the Design Division.
Refer to Table 606.1.3.1 for barrier deflection design values when selecting a longitudinal barrier. The deflection distances for cable and guardrail are the minimum measurements from the face of the barrier to the fixed feature. The deflection distance for unanchored concrete barrier is the minimum measurement from the back edge of the barrier to the drop-off or slope break. The minimum offset to the obstacle can be eliminated completely by attaching the rail to the obstacle by use of a bridge anchor section.
Barrier Type | System Type | Deflection |
---|---|---|
Cable barrier | Flexible | Min. 8 ft. (face of barrier to object) |
Type A guardrail | Semirigid | 4 ft. (back of post to object) |
Type E guardrail | Semirigid | 2 ft. (back of post to object) |
MGS guardrail | Semirigid | 2 ft. 6 in. (back of post to object) |
MGS, 3’ 1 ½” post spacing | Semirigid | 2 ft. (back of post to object) |
MGS, 1’ 6 ¾” post spacing | Semirigid | 1 ft. 6 in. (back of post to object) |
MGS guardrail, double faced | Semirigid | 2 ft. (back of post to object) |
Permanent concrete barrier, unanchored | Rigid Unrestrained | 3 ft.1 (back of barrier to object) |
Temporary concrete barrier, unanchored | Rigid Unrestrained | 2 ft.2 (back of barrier to object) |
Precast concrete barrier, anchored | Rigid Anchored | 6 in. (back of barrier to object) |
Rigid concrete barrier | Rigid | No deflection |
1 When placed in front of 2:1 or flatter fill slope, the deflection distance can be reduced to 2 feet. | ||
2 When used as temporary bridge rail, anchor all barrier within 3 feet of drop-off. |
606.1.3.2 End Terminals, Crash Cushions and Anchors
A guardrail anchor is needed at the end of a run of guardrail to develop tensile strength throughout its length. In addition, when the end of the barrier is subject to head-on impacts, an end treatment is needed. End treatments generally fall into two categories: end terminals and crash cushions.
Guardrail should be extended outside of the clear zone, or the guardrail end is to be embedded into an adjacent embankment or attached to a solid rock face to eliminate the need for a crashworthy end treatment. If these options are not practical, all approach ends of guardrail are provided with a crashworthy end treatment. All downstream ends on two-way roadways are provided with a crashworthy end treatment. Downstream ends on dual lane highways that are not within the clear zone of the opposing lanes need only be treated with end anchors. The plans are to indicate where a crashworthy end treatment is to be installed and a separate payment is made for each crashworthy end treatment.
During the project development process, use the following guidance to determine the guardrail improvements for your project.
- Use MASH 2016 crashworthy end terminals for exposed ends of all new runs of guardrail on all routes.
- On dual lane facilities, guardrail end terminals are to be upgraded with MASH 2016 crashworthy end terminals in both directions even if the project covers only rehabilitation of the roadway in one direction.
- On major routes, replace all existing Pre-350 and 350 end terminals with MASH crashworthy end terminals.
- Downstream Pre-350 and 350 end terminals outside of the major route clear zone may remain in place as long as the terminal provides sufficient anchorage to the guardrail system.
- End terminals within the limits of ramps will be upgraded to MASH 2016 crashworthy end terminals. Improvements to existing guardrail that extends beyond the limits of the ramp onto the crossing route will be up to the judgment of the engineer of record.
- On major routes, guardrail or concrete barrier blunt ends located on either side of a two-way roadway or on the guardrail approach end of dual lane facilities must be replaced with a MASH 2016 crashworthy end terminal even if the project covers only rehabilitation of the roadway in one direction.
- Median Pier Protection: All undamaged bullnose systems may remain in place. Any Pre-350 and 350 end terminals (not protected by guard cable) and Non-350 Guardrail on median pier protection systems shall be replaced with MASH 2016 approved end terminals and MGS guardrail.
- On minor routes, damaged end terminals shall be replaced with MASH 2016 crashworthy end terminals.
- On minor routes, existing end terminals (in serviceable condition) may be left in place. Engineering judgment in accordance with AASHTO’s Roadside Design Guide and crash history should be used to determine guardrail improvements for each project.
Grading for New Roadway Construction. When an end terminal falls within the limits of an area that includes construction of a new roadbed, provide the needed embankment (cut/fill) quantities to construct the Standard Grading Limits shown in Standard Plan 606.81 and include that volume in the model. Indicate in the Summary of Quantities for Crashworthy End Terminals that “Standard Grading Limits” are required and that payment is included in the embankment quantities.
See Roadside Design Guide 4th Edition 2011, Chap. 8.3.3 (pages 8-4, 5, 6 and 7), for further information on grading. On projects without earthwork pay items, Class III shaping slopes shall be used to provide the flat recovery area.
Grading for Existing Roadbeds. When end terminals are to be installed on an existing roadway, an evaluation of each location should be made to determine if an existing platform is already in place that meets the Standard Grading Limits shown in Std. Plan 606.81. If a sufficient platform does exist, indicate in the Summary of Quantities for Crashworthy End Terminals that no grading is necessary.
If an existing platform does not exist, or is insufficient, evaluate the existing terrain and determine whether the Standard Grading Limits can reasonably be constructed with Shaping Slopes Class III without creating an excessively steep in-slope or blocking the ditch with fill (that is, project scope generally does not include purchasing new right of way and/or making significant alterations to the existing in-slopes/back-slopes/ditches). For most existing locations, retrofitting the terrain to meet the Standard Grading Limits is not feasible, but if it is, indicate in the Summary of Quantities for Crashworthy End Terminals that Standard Grading Limits are required and include the necessary quantities for Shaping Slopes Class III.
If it is not practical to construct the Standard Grading Limits but Alternate Grading Limits can reasonably be constructed, indicate in the Summary of Quantities for Crashworthy End Terminals that “Alternate Grading Limits” are required and include the necessary quantities for Shaping Slopes Class III. This is the most common option for existing roadways.
Shaping Slopes Class III should not be used if the existing terrain requires significant quantities of fill. When significant grading is required, other grading pay items should be used with specific volumetric quantities to provide the flat recovery area.
If the existing terrain is such that Alternate Grading Limits cannot be reasonably constructed within the project scope, a design exception may be necessary.
See Roadside Design Guide 4th Edition 2011, Chap. 8.3.3 (pages 8-4, 5, 6 and 7), for further information on grading.
Bridge End Treatment
Guardrail is placed at bridge end in accordance with typical locations show in the standard plans on most routes. When the bridge end is shielded with guardrail, crashworthy end terminals are provided.
On certain low-volume highways throughout the state, bridge ends may be delineated in lieu of shielding. This option is viable where the operating speed is less than 60 mph and the design AADT is 400 or fewer vehicles per day. The delineation-only option is primarily governed by the parameters of speed and volume. Irrespective of any values for these parameters, however, the use of delineation-only is prohibited on Major Routes as well as the National Highway System (NHS).
Use of the delineation-only option is not recommended on bridge ends in areas of poor geometry (horizontal alignment, vertical alignment, sight distance, etc.). Nor is it recommended in areas with a crash history (as calculated between two points at least 0.25 miles from either approach) in excess of the statewide average for similar road. If further analysis of either of these situations proves the delineation option to be viable, then a design exception should be obtained for its use.
Additionally, the delineation-only option should be limited to those bridge replacements or rehabilitations where the existing structure was unshielded or the existing roadway template cannot reasonably accommodate the installation of guardrail.
Guardrail is not generally used to protect traffic from the ends of bridges carrying a crossroad or street over the through lanes in developed areas where speed controls exist or sidewalks are provided. If however, at ends of such bridges the roadway is in a high fill or has sharp curvature, guardrail may be considered.
Embedded and Rock Face Terminals
An embedded terminal is designed to terminate the guardrail by burying the end in a backslope. The embedded terminal is the preferred terminal because it eliminates the exposed end of the guardrail. The embedded terminal uses a concrete block anchor or embedded steel post to develop the tensile strength in the guardrail. The backslope needed to install an embedded terminal is to be 1V:3H (3:1) or steeper and at least 4 ft. above the roadway. The entire embedded terminal can be used within the length of need for backslopes of 1V:1H (1:1) or steeper if the barrier remains at full height in relation to the roadway shoulder to the point where the barrier enters the backslope. For backslopes between 1V:1H (1:1) and 1V:3H (3:1), design the length of need beginning at the point where the W-beam remains at full height in relation to the roadway shoulder usually beginning at the point where the barrier crosses the ditch line. If the backslope is flatter than 1:1, provide a minimum 20-ft. wide by 75 ft. long distance behind the barrier and between the beginning length of need point at the terminal end to the mitigated object to be protected.
For new installations, flare the guardrail to the foreslope/backslope intersection using a flare rate that meets the criteria in Standard Plan 606.30 and or Standard Plan 606.80. Provide a 1V:4H (4:1) or flatter foreslope into the face of the guardrail and maintain the full guardrail height to the foreslope/backslope intersection in relation to a 1V:10H (10:1) line extending from edge of shoulder breakpoint.
For rock cuts with a smooth face, a rock face guardrail anchor is the preferred terminal. This option should not be used on rock cuts with a rough face that might cause vehicle snagging rather than providing relatively smooth redirection.
Crashworthy End Terminals and Crash Cushions
If an embedded terminal or rock face anchor cannot be installed, consider installing a crashworthy end terminal and/or crash cushion. Crashworthy end terminals and crash cushions are devices used to provide an acceptable level of safety to the end of a roadside barrier or fixed object. Such treatment is required because of the serious consequences that may result from a vehicle impacting an unprotected barrier or object. An unprotected barrier or object can cause an impacting vehicle to abruptly stop, become unstable or roll; it can even penetrate the passenger compartment, all of which increase the risk of injury to the vehicle’s occupants.
End terminals or crash cushions that have met the safety requirements contained in MASH 2016 are deemed crashworthy and must be listed as eligible for use on the NHS by FHWA. MoDOT then reviews these items and makes a determination of their use on Missouri’s state-owned roadways. Refer to MoDOT’s End Terminals, Crash Cushions and Barrier Systems website for more information on approved crashworthy end terminals.
While crashworthy end terminals do not require an offset at the end, a flare is recommended so the end piece does not protrude into the shoulder. These terminals may have a 2 ft. offset to the first post. Four feet of widening is needed at the end posts to properly anchor the system. When widening includes an embankment, fill material will be necessary for optimum terminal performance. (See Standard Plan 606.30 for widening details.) When the entire barrier run is located farther than 12 ft. beyond the shoulder break point and the slopes are greater than 1V:10H (10:1) and 1V:6H (6:1) or flatter, additional embankment at the terminal is not needed. Crashworthy end terminals located within 10 ft. of the edgeline will be delineated with a Type 3 Modified Object Marker.
Currently, there is not a MASH 2016 approved flared-end terminal system. However, if a flared-end terminal is needed, there are NCRHP 350 systems available. These designs include an anchor for developing the tensile strength of the guardrail. The length of need begins at the third post for two approved flared terminals. When a flared terminal is specified, it is critical the embankment quantity also be specified so the area around the terminal can be constructed as shown in the standard plans.
Additional information on crashworthy end terminals and internet links to approved terminals |
MoDOT's end terminal website |
EPG 1040.4 Crashworthy End Terminal and Qualified Plastic Guardrail Block |
There are five distinct types of end terminals and crash cushions; Type A, B, C, D and E. This classification aids in the designers’ selection of the appropriate treatment for a given context. It is important to note each of these treatments reduces driver risk to equally acceptable levels and the classifications are based merely on the benefit/cost associated with replacement or repair.
Each type is classified as follows:
End Terminals
Type A. Type A end terminals are treatments used for one-sided barriers such as roadside guardrail or roadside concrete barrier. These devices can also be used on one-sided barriers in the median, provided sufficient clear space is available behind the system to allow opposite direction traffic to recover from an errant path.
Crash Cushions
Type B. Type B crash cushions are end treatments used for double-sided barriers, most often in the median. These devices can safely be impacted from several angles including the opposite direction. Type B crash cushions cannot be installed in paved surface locations unless the installation is temporary and the paved area will be resurfaced after the system’s removal.
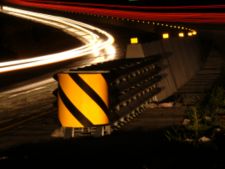
Type C. Type C crash cushions are an end treatment used for double-sided barriers, in gore areas and in the median. Like the Type B, this device can safely be impacted from several angles usually ranging from head-on to the opposite direction. Type C crash cushions, however, may be installed in both paved and unpaved surface locations, but must be installed on an asphalt or concrete pad in non-paved areas. After impact, these crash cushions are usually damaged beyond repair and as such, should be used only in areas where low, annual-impact frequencies are expected.
Type D. Type D crash cushions have all of the installation and performance parameters of the Type C, but must be at least 80% reusable and have the ability to be reset manually with a moderate amount of repair. Type D crash cushions should be used in gore areas or medians with moderate traffic volumes and where high-impact frequencies are expected.
Type E. Type E crash cushions have all of the installation and performance parameters of the Type C but must have the ability to reset with little or no manual intervention and have an average cost of repair under $250 per event. Type E crash cushions should be used in gore areas or medians with high traffic volumes and where high-impact frequencies are expected.
Use the following decision matrix to help determine the appropriate end treatment for a given context, not to determine whether or not a barrier or object should be protected. The expected crashes per year are on an average basis:
End Treatment Decision Matrix | |||||||
---|---|---|---|---|---|---|---|
One-Sided Protection Required | Two-Sided Protection Required | ||||||
Non-traversable Terrain Beyond the Terminal | Traversable Terrain Beyond the Terminal | Fewer than 0.5 Crashes Per Year Expected | 0.5 or More Crashes Per Year Expected | ||||
Unpaved | Paved or Unpaved | Major ADT <75,000 | Minor ADT <30,000 | Major ADT ≥75,000 | Minor ADT ≥30,000 | ||
Type A (energy absorbing) | Type A (non-energy absorbing) | Type B | Type C | Type D | Type E |
Sand barrels are a crash cushioning system most often used to shield fixed objects that cannot be removed or relocated. Sand barrels are recommended for temporary usage such as in work zones. Conduct a benefit/cost analysis before sand barrels are installed in a permanent application and consult with Maintenance staff. For more information, refer to EPG 612.2 Sand-Filled Impact Attenuators (Sand Barrels).
Other Anchor Applications
End anchors are used to develop the tensile strength of the guardrail at the end of guardrail runs where a crashworthy end terminal is not needed.
606.1.3.2.1 Crashworthy End Terminals with Curb
When curb is present in front of and parallel to a crashworthy end terminal (CET), the potential exists the CET will not perform as designed (i.e. will not redirect the vehicle). When installing CETs, for new construction and roadway upgrades, the need for the curb and the curb height at the location of the CET shall be considered. See EPG 749 Hydrologic Analysis and EPG 640.1 Pavement Drainage to calculate the drainage needs in and around CETs. Gutters might be able to be spread out or curb heights reduced in the vicinity of the CET while still accommodating drainage needs and the installation of the CET. Drainage calculations shall be documented in eProjects.
When curb is present in front of and parallel to the CET, the project file should have documentation regarding the design selected and considered in the following priority order:
- 1. Eliminate the curb or do not install new curb for the entire length of the CET with an additional 30’-50’ of curb removed upstream of the CET.
- 2. Reduce the curb or install new curb to a height of two (2) inches for the entire length of the CET with an additional 30’-50’ upstream of the CET.
- 3. Reduce the curb or install new curb to a height of four (4) inches for the entire length of the CET with an additional 30’-50’ upstream of the CET.
If a two-inch curb is not adequate for the drainage needs, a four-inch curb may be installed but is the maximum curb height allowed when installing a CET.
606.1.3.3 Transitions and Connections
When there is an abrupt change from one barrier type to a more rigid barrier type, a vehicle hitting the more flexible barrier is likely to be caught in the deflected barrier pocket and directed into the more rigid barrier. This is commonly referred to as “pocketing.” A transition stiffens the more flexible barrier by decreasing the post spacing, increasing the post size, and using stiffer beam elements to eliminate the possibility of pocketing. A transition is needed when connecting guardrail to a more rigid barrier or a structure, or when a rigid object is within the deflection distance of the barrier.
Bridge Connections
Guardrail is placed at bridge ends in accordance with typical locations shown in the standard plans. Guardrail placed for bridge end protection is anchored to the bridge end by a vertical barrier transition section. Existing bridge end connections that do not conform to current standards are to be considered for replacement or modification. In order to determine the appropriate solution for the specific non-standard bridge end connection, the Bridge Division Liaison Engineer is to be consulted. Where guardrail at the downstream end of a one-way bridge is necessary because of a high fill or other condition, the guardrail is connected to the vertical transition section.
The post spacing for MGS vertical bridge transitions varies from the previous bridge transition sections for Type A guardrail. If an existing bridge anchor section is replaced, an evaluation of the impact to drain basins should be conducted.
Common Bridge Barrier and Railing (for Rehabilitations) Table |
606.1.3.4 Median Barrier Selection and Placement
The most desirable barrier installation uses the most flexible system appropriate for the location and one that is placed as far from the traveled way as practicable. Good engineering judgment is called for in determining the appropriate placement of barrier systems. Solutions may need to be arrived at while considering competing factors such as crash frequency and severity. As discussed previously, performance of the system relies on the interaction of the vehicle, driver and system design at any given location. Additionally, the ability to access the system for maintenance and the need for access across the barrier play into the final decision.
With median barriers, the deflection characteristics and placement of the barrier for a traveled way in one direction can have an impact on the traveled way in the opposing direction. In addition, the median slopes and environmental issues often influence the type of barrier that is appropriate.
In narrow medians, avoid placement of barrier where the design deflection extends into oncoming traffic. Narrow medians provide little space for maintenance crews to repair or reposition the barrier. Therefore, avoid installing deflecting barriers in medians that provide less than 8 ft. from the edge of the traveled way to the face of the barrier.
In wider medians, the selection of barrier might depend on the slopes in the median. At locations where the median slopes are relatively flat (1V:10H [10:1] or flatter), unrestrained precast concrete barrier, beam guardrail and cable barrier can be used depending on the available deflection distance. At these locations, position the barrier as close to the center as possible so that the recovery distance can be maximized for both directions. There may be a need to offset the barrier from the flow line to avoid impacts to the drainage flow.
In general, cable barrier is recommended with medians that are 30 ft. wide or wider. However, cable barrier may be appropriate for narrower medians if adequate deflection distance exists. Refer to EPG 606.2.3 Design and Installation Guidelines for design and installation guidelines for cable barriers. Do not use concrete barrier at locations where the foreslope into the face of the barrier is steeper than 1V:10H (10:1).
At locations where the roadways are on independent alignments and there is a difference in elevation between the roadways, the slope from the upper roadway might be steeper than 1V:6H (6:1). In these locations, position the median barrier along the upper roadway and provide deflection and offset distance as discussed previously. Barrier is generally not needed along the lower roadway except where there are fixed features in the median. When W-beam barrier is placed in a median as a countermeasure for cross-median crashes, design the barrier to be struck from either direction of travel. For example, the installation of beam guardrail might be double-sided.
Guardrail may be specified in medians to provide a positive barrier. Guardrail may also be specified to convert an existing raised curb median to a barrier median provided the top of the MGS guardrail is placed 31 in. above the pavement elevation at the curb face. Double faced MGS guardrail may be used on a raised median width of 2 ft. back-to-back. For greater widths, two single lines of MGS guardrail will be required.
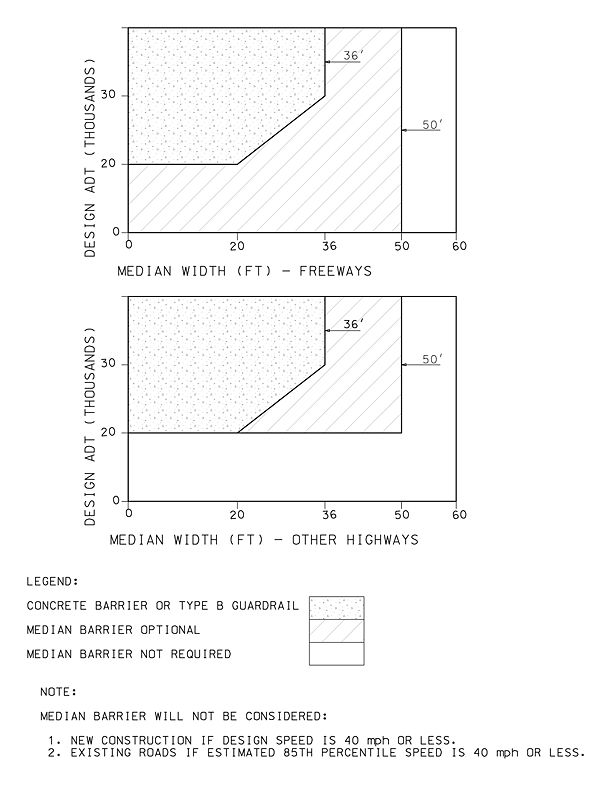
For medians of variable widths, a detail in the standard plans provides for transition from single faced to double faced guardrail. Crashworthy end terminals are added only at the beginning and ending of a total run of guardrail and not at each break caused by intersections and median openings. Breaks caused by intersections and median openings will be closed by means of a crashworthy special end treatment.
Double faced MGS guardrail can be used on a flush median, as shown in the figure below. Double faced MGS guardrail is to be used where a median barrier is to be provided but site conditions will not permit the use of a concrete barrier (drainage, visibility requirements, aesthetics, etc.). The concrete barrier is generally limited to the high volume roadways with narrow width medians.
Bullnose Guardrail System
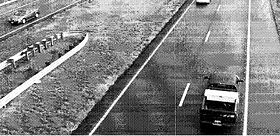
The bullnose guardrail system may be used in the medians of expressways or freeways to shield drivers from hazards, such as bridge piers and other obstacles. It is not a crashworthy end terminal, but is rather a non-gating barrier principally constructed of Type E guardrail. As long as the median’s vertical differences are minimal or can be minimized through grading, the bullnose guardrail system is an appropriate treatment for new construction. This system requires at least 15 ft. of median width for its construction. The bullnose guardrail system is not to be erected between twin bridges. Alternatives are available for twin bridge protection in Standard Plan 606.01. Consult Standard Plan 606.30 for grading requirements and other important details.
606.1.3.5 Closures of Existing Streets, Roads, Bridges or Non-Traversable Roads
606.1.3.5.1 Closures of Existing Streets and Roads
When closing a street or road, use either Type 4 Object Markers only or a combination of Type 4 Object Markers and Type D guardrail as shown in Figs. 606.1.3.5.1.1 and 606.1.3.5.1.2. Where no hazard exists beyond the end of the closed street or road for a reasonable distance, Type 4 Object Markers are sufficient for delineation. Where a hazard exists beyond the end of the closed street or road that is considered equal to or greater than that created by the use of guardrail (for example a removed bridge or culvert, or a structurally deficient bridge), a combination of both Type 4 Object Markers and Type D guardrail is specified. Refer to Standard Plan 606.00 Guardrail and Standard Plan 903.03 Sign Mounting Details.
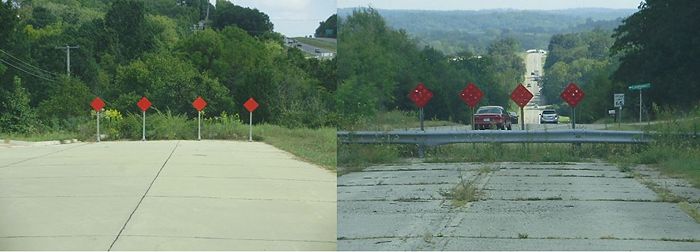
with Type D Guardrail |
Additional emphasis of a sign barricade may be required for horizontal and vertical alignment of the roadway and at tee intersections as shown in Fig. 606.1.3.5.1.3. Location and installation guidelines for sign barricades are located in EPG 903.6.53 Sign Barricades, and Standard Plan 903.02 Highway Signing Structure Signs.

606.1.3.5.2 Closure of Existing Bridges or Non-Traversable Roads
Bridges and roadways may be closed to the traveling public due to natural aging process of the structure, weather damage (ex. flooding), bridge/roadway slides, etc.
Restoration of the bridges and roadways may be delayed due to scheduling constraints or budget costs of projects. District personnel and Central Office Bridge Division personnel should discuss the schedule to repair the bridge. District personnel and Central Office Construction/Material Geotechnical personnel should discuss the schedule to repair the roadway. Based on the repair schedule, the district will determine the type of closure needed for the bridge or roadway.
For bridge and/or roadway closures, bridge/roadways shall be closed according to typical application EPG 616.8.8 (TA-8) Highway Closure – MT, EPG 616.8.8 (TA-8) Highway Closure – DE/CM, EPG 616.8.8a (TA-8a) Closure of Existing Bridges or Non-Traversable Roads, Standard Plan 606.00 Guardrail and Standard Plan 903.03 Sign Mounting Details.
Figs. 606.1.3.5.2.1 and 606.1.3.5.2.2 are examples of the recommended installation of the bridge/roadway closures based on EPG 616.8.8a Closure of Existing Bridges or Non-Traversable Roads.
For less than one month closure duration, the district may use Type 3 barricades as shown in Fig. 606.1.3.5.2.1.
For six-month closure durations, the district may use Type 3 barricades and temporary concrete traffic barriers as shown in Picture 5. As shown in typical application EPG 616.8.8a, the temporary concrete traffic barriers should have red reflective sheeting across the face of the barrier.
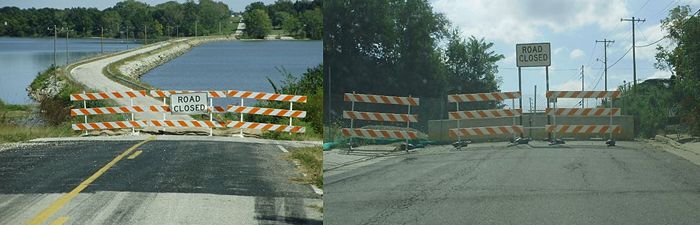
Type 3 Barricades and Temporary Barriers |
For longer closure durations, the district may use Type D guardrail and Type 4 object markers as shown in Fig. 606.1.3.5.2.3.
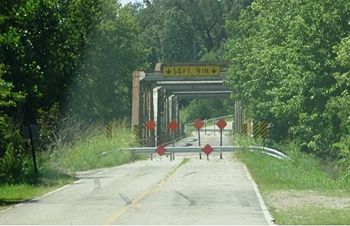
D Guardrail and Type 4 Object Markers |
When closing bridges and/or roadway, the more temporary devices used will require additional attention compared to permanent devices.
606.1.4 Maintenance Planning Guidelines for Guardrail
Printable Maintenance Planning Guideline for Guardrail.
Index of all Maintenance Planning Guidelines.
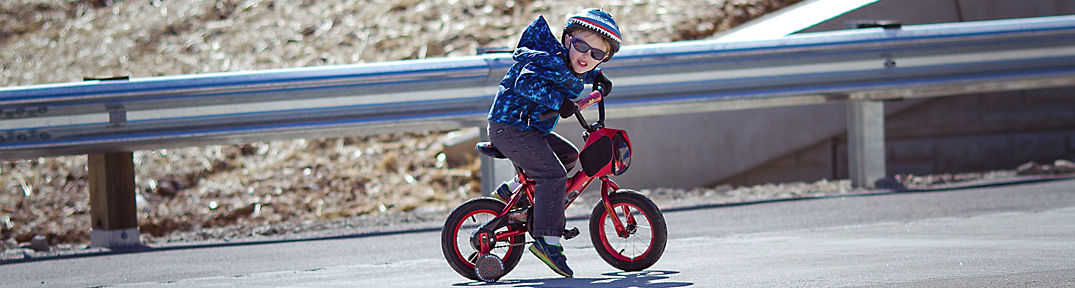