Category:242 Optional and Alternate Pavement Designs
Examples and Results |
Request for Bids |
Pavement Plans |
January 2007 Bid Results |
Overall Bid Results |
242.1 Purpose of Alternate and Optional Pavement Bidding
In an effort to get the best value, create a competitive environment for concrete and asphalt paving industries and promote innovation, MoDOT requires a concrete and asphalt option on the majority of contracts containing full depth pavement 7 inches or greater. If the combined total of all full depth pavements, for one or more projects under a single contract, is greater than 14,000 square yards or any single project has at least 7,500 square yards of continuous paving, all full depth pavement for all projects within the contract shall be set up as alternate pavement. Continuous paving is defined as one continuous, monolithic piece of full depth pavement with no breaks.
Alternate pavement requires a Life Cycle Cost Adjustment (LCCA) factor be calculated and applied to the asphalt alternate. If the full depth quantities do not meet the threshold for alternate pavements, the full depth pavement should be set up as optional pavement, with no LCCA factor.
No LCCA factor shall be applied for the alternate pavement quantity in the infrequent case of a composite pavement design bid against a full depth pavement design, such as for a widening project with a UBAWS on a PCC pavement versus a full depth HMA pavement.
Use of Life Cycle Cost Adjustment Factor for Alternate Pavements | ||
---|---|---|
Area of Pavement> 14,000 yd2 total (Combined area for all projects in single contract) (Combined total of all SP and BP) (Do not include shoulder quantity) |
Area of Pavement < 14,000 yd2 total (Combined area for all projects in single contract) (Combined total of all SP and BP) (Do not include shoulder quantity) | |
≥ 7,500 yd2 Continuous in any single project within a contract | < 7,500 yd2 Continuous in all single projects within a contract | |
Alternate with a LCCA | Alternate with a LCCA | Optional (No LCCA) |
242.2 Life Cycle Cost Adjustment (LCCA) Factor
Life Cycle Cost Adjustment (LCCA) Factor is the monetary difference in total future pavement rehabilitation costs, between asphalt and concrete, brought back to present worth value using a 5-year average of the most current Federal Office of Management and Budget (OMB) discount rate. The average rate will be limited to a minimum of zero. Since the anticipated future rehabilitation costs for asphalt exceed those for concrete, the LCCA factor, or cost difference between the pavement types, is added to the low asphalt bid for purposes of comparison with the low concrete bid. Anticipated future rehabilitation treatments for asphalt pavements are cold milling and overlay of the traveled-way surface course only at 20 years and the entire surface, including the shoulders (Type A2 or thicker), at 33 years. Anticipated future rehabilitation treatments for PCCP are full depth pavement repair of 1.5% of the entire surface and diamond grinding of the entire traveled-way surface at 25 years. The treatment types and timeframes used for calculating the LCCA were jointly agreed upon between MoDOT and the contracting industries.
The following figures show how the LCCA is applied.
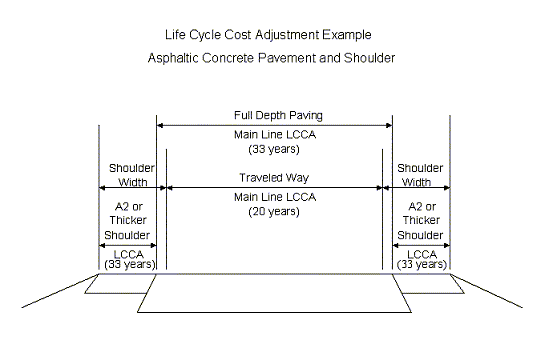
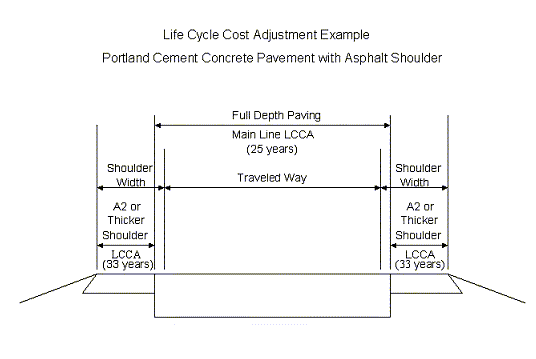
MoDOT estimators prepare LCCA factors, for inclusion in the contracts' Job Special Provisions for projects containing alternate pavements, using current construction and material unit costs and the latest published OMB discount rates. Having knowledge of the LCCA factor allows contractors flexibility in bidding to enable use of the best valued material for the regional market.
242.2.1 Alternate Categories for LCCA Factors
The designer must determine if a project has a need for multiple LCCA factors. All common pavement types should be grouped under one LCCA factor. Circumstances for using LCCA factors other than the primary one for the mainline pavement include:
- asphalt pavements with different surface courses
- side roads and city streets
- A2 or thicker shoulders
- significant changes in directional truck traffic.
Ramps should normally be included with the mainline pavement. Type A3 shoulders do not receive an LCCA factor.
It is strongly recommended to not exceed three LCCA factors for a single project for the sake of simplifying bidding for the contractor. The following examples help explain how to determine the LCCA factor groupings:
Example 1:
- Mainline - 10,000 sy 11” SP125BSM or 9” PCCP
- Mainline Shoulder – 2400 sy A2
- Side Road – 6000 sy 7” BP-1 or 7” PCCP
- Ramps 4000 sy 10” SP125BSM or 8” PCCP
This example will have 3 sets of alternates with an LCCA, since the contract has three different non-shoulder pavement designs and the cumulative full depth pavement for all projects within a contract exceeds 14,000 yd2. The mainline and ramps will be one set of alternates, the side road would be one set of alternates and the A2 shoulder will be the other.
Example 2:
- Mainline – 7,044 sy 11” SP125C or 9” PCCP
- Mainline Shoulder – 1000 sy A3
- Side Road – 7,088 sy 7” BP-1 or 7” PCCP
This example will have 2 sets of alternates with an LCCA, since the contract has two different non-shoulder pavement designs and the cumulative full depth pavement for all projects within a contract exceeds 14,000 yd2. The mainline will be one set of alternates and the side road would be the other. The A3 shoulder will be optional in the roadway category.
Example 3:
- Mainline – 4,000 sy 8” SP125C or 7.5” PCCP
- Side Road – 5,000 sy 8” BP-1 or 7.5” PCCP
- 2 Outer Roads – 3,200 sy and 2,800 sy 8” BP-1 and 7.5” PCCP
This example will have 2 sets of alternates with an LCCA, since the contract has two different non-shoulder pavement designs and the cumulative full depth pavement for all projects within a contract exceeds 14,000 yd2. The mainline will be one set of alternates and the side and outer roads would be the other.
Example 4:
- Mainline – 4,000 sy 8” BP-1 or 7.5” PCCP
- Side Road – 5,000 sy 6” BP-1 or 6” PCCP
This example will be set up as optional, since the total full depth pavement area does not exceed 14,000 yd2 and has less than 7,500 yd2 of continuous paving in any of the single projects., The contract line items would be 401.00-05 Optional Pavement (8”BP vs 7.5”PC) and 401-99.05 Optional Pavement (6”BP vs. 6” PC).
242.2.2 Information Required for Completion of LCCA
Separate traveled way and total area of pavement quantities should be provided for each surface mix and binder type for each route. The following information is necessary:
- 1) Area of Traveled Way - consists of the area within the travel lane (area of new full depth between the pavement markings) for each set of alternates per mix design and binder grade (see the above typical for details). A good check of the calculated traveled way is that the area should be less than the total area of pavement quantity.
- 2) Total Area of Pavement – Needed for each set of alternates and can usually be obtained from a project’s plans Quantity Sheets or proposal (per mix design and binder grade).
- 3) Type of Asphalt Pavement Surface Mix (mix design and binder grade).
242.2.3 Time Frame for LCCA Completion
Districts need to supply the information required for completion of the LCCA factors in the transmittal memorandum that is included with the PS&E submittal by the PS&E due date. This will allow time for the Design Division reviewer to check the submittal, send any review comments as necessary and forward a request to the estimator within the time allotted.
To ensure there is sufficient time to prepare an accurate LCCA by the due date, a request for LCCA should be submitted to the estimators a minimum of one week prior to the notice with all the required information. This will allow time to receive material quotes, which may take a few days to receive and the use of the most current binder price.
242.3 Plans and Estimates for Projects with Alternate Pavements
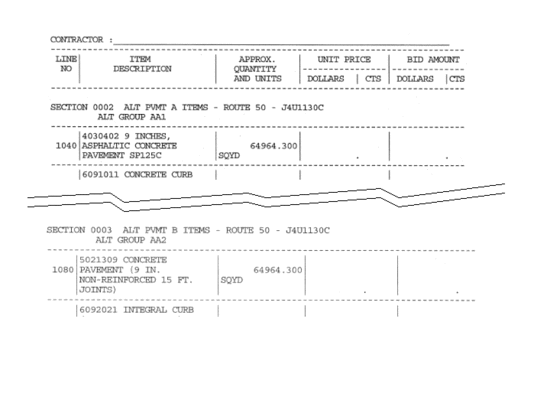
Plans and estimates for projects with alternate pavements should have:
- Typical sections for both alternates, including station limits, and all side road connections.
- All pay items for full depth alternate pavements shall be in square yards for the entire pavement.
- One set of quantities sheets with separate sheets for the items associated with each alternate.
- Using the "Bidtabs.net" program, the quantities for pavement and other items associated only with the asphalt alternate (designated as "Alternate A") should be designated as "Section 02" and the quantities for pavement and other items associated only with the concrete alternate (designated as "Alternate B") should be designated "Section 03". For A2 shoulders or thicker use "Section 04" for the shoulder type that corresponds with "Section 02" and "Section 05" for the shoulder type that corresponds with "Section 03". This will enable summation of the appropriate subtotals to compile an estimated total cost per alternate. If the project had multiple pavement alternates, the 2nd pavement alternate would be “Section 6” and “Section 7”. For shoulder rumble strips, include the bituminous rumble strip pay item with the asphalt alternate, and the concrete rumble strip pay item with the concrete alternate.
- Job Special Provision ALTERNATE FOR PAVEMENTS should be inserted in the Job Special Provisions. The LCCA factor is calculated by the Central Office.
- For projects that the pavement team has provided alternates for base and pavement designs, then the job special provision ALTERNATE TECHNICAL CONCEPT – GRADING, BASE AND PAVING may be inserted to give the contractor base and pavement thickness options.
242.4 Plans and Estimates for Projects with Optional Pavements
Plans and estimates for projects with optional pavements should include:
- Typical sections for both options, including station limits, and all side road connections.
- All pay items for optional pavements shall be in square yards and included in the roadway section. For BP pavements use 401-99.05 and for SP pavements use 403-99.05. Be sure to use a description what pavement options it covers.
- Shoulder rumble strips should be paid for by pay item 626-99.09 Optional Rumble Strips per station and be included in the roadway section.
- The plans should include a note that states that contrast marking will be required for the concrete option at no direct pay.
- Job Special Provision OPTIONAL PAVEMENTS should be inserted in the Job Special Provisions.
- For projects that the pavement team has provided alternates for base and pavement designs, then the job special provision ALTERNATE TECHNICAL CONCEPT – GRADING, BASE AND PAVING may be inserted to give the contractor base and pavement thickness options.
242.5 Selecting a Controlling Pavement Thickness for Base and Subgrade Profile
Below are design guidelines for determining the subgrade and base profile elevations for different project scenarios:
242.5.1 Separate Grading and Paving Projects with 12 in. or 18 in. Rock Base
Subgrade profile and cross sections should be designed for the thicker pavement design. If the thinner pavement design is constructed, the contractor will be responsible for maintaining the profile grade. In the paving project the addition of subgrade material for the thinner pavement design will be paid for as Subgrading and Shouldering, Class 2.
242.5.2 Separate Grading and Paving Projects with Type 1, 5 or 7 Base
Subgrade, profile and cross sections should be designed for the thinner pavement design. If the thicker pavement design is constructed, the contractor will be responsible for maintaining the profile grade. In the paving project the removal of subgrade material for the thicker pavement design will be paid for as Subgrading and Shouldering, Class 1. Crossroad structures should be designed to accommodate a minimum cover based on the thicker pavement design.
242.5.3 Combined Grading and Paving Project
Subgrade profile and cross sections should be designed for the thinner pavement design. The contractor will be responsible for maintaining the profile grade for either pavement design with no direct pay. Crossroad structures should be designed to accommodate a minimum cover based on the thicker pavement design.
242.6 Specifying One Pavement Type
The core team should always provide pavement options that allow flexibility in bidding to enable use of the best valued material for the regional market.
Occasionally, reasons exist to specify one type of pavement instead of optional or alternate designs. These may include circumstances such as:
- widening existing pavements where different pavement types introduce safety and durability issues
- underground utilities where using one pavement type eliminates the need to relocate
- maintaining cross drainage across pavement structure
- project staging and project scoping regarding long-range transportation goals.
In consideration of these reasons and others, the core team may determine there is a need to specify one pavement type over another on a project. The core team decision, which will include the concurrence of the Pavement Team member and the Design Liaison Engineer, is documented with a memo in eProjects.
In other unique circumstances, the selection of one pavement type is made because of preference by a stakeholder or outside entity or, because of factors other than the aforementioned reasons, without concurrence by the Pavement Team member and/or Design Liaison Engineer. For these instances, the district core team will document the reasons why one pavement type was selected in eProjects.
When one pavement type is included in a MoDOT contract for any of the above mentioned reasons, the State Design Engineer and State Construction and Materials Engineer should be informed of reasoning for the decision to ensure consistent communication with industry.