106.3.2.86 TM-86 Preparation of Samples for Surface Sealer Wet Track Abrasion
The purpose of this test method is to outline the process and procedure for making and testing Wet Track Abrasion Samples based on International Slurry Surfacing Association (ISSA) TB-100. Method ISSA TB-100 measures the wearing qualities of pavement sealer systems under wet abrasion conditions.
106.3.2.86.1 Definitions
WTAT – Wet Track Abrasion Test
WTAT prep glass – Glass plate with dimensions of 30 cm x 30 cm x 1.27 cm that is equipped with a clipboard clip at the top to hold the sample drawdown felt in place.
106.3.2.86.2 Equipment
1. Equipment needed as outlined in ISSA TB-100.
2. Drawdown plate (WTAT Prep Glass) capable of holding drawdown felt in place for casting.
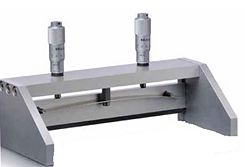
3. Casting knife 12 inches wide; capable of making smooth, even draw of liquid sealer sample.
4. Roofing felt (30-45 lb. strength).
5. Balance capable of weighing 5,000 grams to within 0.1 gram.
6. Liquid sealer sample needing to be tested.
7. Wash bottle equipped with narrow mouth to control water flow.
8. Sealer stirring mechanism capable of homogenous mixing of material.
9. Soft, absorbent paper towel or cloth towels.
106.3.2.86.3 Procedure
1. Cut a piece of 30-45 lb. roofing felt to measure 29 cm X 35 cm. Flatten roofing felt substrate and dry in a 50°C oven overnight.
2. Place roofing felt on a support base capable of holding felt in a flat position that will prevent felt from moving. WTAT prep glass works well as the support base with hold down.
- a. Place the long side of the felt at the top of the support base under the hold down mechanism.
- b. Make sure the near edge of the felt is at or just over the near edge of the table or bench it rests on to allow a slight overhang of the felt to allow excess cast sealer to fall off the sample felt when drawn.
3. Verify that the casting knife is wide enough to cover the long edge of the WTAT drawdown felt. Place casting knife on the top edge of the drawdown felt just below the clip and verify the following:
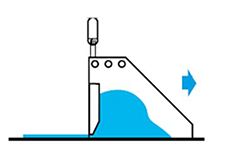
- a. Casting knife has been set to a depth of 50 mils (0.0127 cm).
- b. The knife edge is facing down and the edge stops are facing the tester. (Casting knives with bevel edge must face tester to draw sample properly. See figure to the right.)
4. Place 50-100 grams of sealer on the felt just in front of the knife edge and spread it from side to side to even out the material depth. Enough material should be placed to allow the sample to make a smooth even casting over enough area to cover the WTAT abrasion head wear pattern.
5. Gently pull the casting knife smoothly and evenly at a moderate speed to create a casting of sealer material that is even in depth and smooth all the way across. Allow excess material to fall off the edge of the felt into a waste container or receiving vessel.
6. Clean the casting knife with clean tap or distilled water, making sure not to get the micrometer dials wet. Dry the knife area with a soft, absorbent paper towel or a cloth towel.
7. Place cast sample in a 60°C forced air oven and dry to constant weight according to ISSA TB-100.
8. Remove cast sample from oven and let cool for at least 5 minutes. Record weight of cured cast sample as Cured Casting Total Weight.
9. Fully submerge cured cast sample in 25°C tap water bath for 3-day soak.
10. Promptly remove cured cast sample from water bath and place in WTAT abrasion test pan by pressing soaked felt sample flat all the way to the pan edges. Ensure felt is pressed well into the pan bottom and around the edges of the test pan.
11. Follow ISSA TB-100 steps 5.9 and 7.3-7.7 for abrasion testing of soaked cured cast sample and post abrasion drying.
106.3.2.86.4 Calculation
1. Record the weight (grams) of cured cast sample as Cured Casting Total Weight.
2. Record weight (grams) of abraded cast sample as Cured Abraded Weight.
3. Determine the mean diameter (cm) of the abrasion pattern on a series of test samples and calculate the mean abrasion wear area in cm2.
4. Calculate the abrasion loss (g/m2) of the sample using this equation:
- Abrasion Loss =