User talk:Hoskir
REVISION REQUEST 4023
751.24.2.1 Design
Designs of Mechanically Stabilized Earth (MSE) walls shall be completed by consultants or contractors in accordance with Section 11.10 of LRFD specifications, FHWA-NHI-10-024 and FHWA-NHI-10-025 for LRFD. Bridge Pre-qualified Products List (BPPL) provided on MoDOT's web page and in Sharepoint contains a listing of facing unit manufacturers, soil reinforcement suppliers, and wall system suppliers which have been approved for use. See Sec 720 and Sec 1010 for additional information. The Geotechnical Section is responsible for checking global stability of permanent MSE wall systems, which should be reported in the Foundation Investigation Geotechnical Report. For MSE wall preliminary information, see EPG 751.1.4.3 MSE Walls. For design requirements of MSE wall systems and temporary shoring (including temporary MSE walls), see EPG 720 Mechanically Stabilized Earth Wall Systems. For staged bridge construction, see EPG 751.1.2.11 Staged Construction.
For seismic design requirements, see Bridge Seismic Design Flowchart. References for consultants and contractors include Section 11.10 of LRFD, FHWA-NHI-10-024 and FHWA-NHI-10-025.
Design Life
- 75 year minimum for permanent walls (if retained foundation require 100 year than consider 100 year minimum design life for wall).
Global stability:
Global stability will be performed by Geotechnical Section or their agent.
MSE wall contractor/designer responsibility:
MSE wall contractor/designer shall perform following analysis in their design for all applicable limit states.
- External Stability
- Limiting Eccentricity
- Sliding
- Factored Bearing Pressure/Stress ≤ Factored Bearing Resistance
- Internal Stability
- Tensile Resistance of Reinforcement
- Pullout Resistance of Reinforcement
- Structural Resistance of Face Elements
- Structural Resistance of Face Element Connections
- Compound Stability
- Capacity/Demand ratio (CDR) for bearing capacity shall be ≥ 1.0
- Strength Limit States:
- Factored bearing resistance = Nominal bearing resistance from Geotech report X Minimum Resistance factor (0.65, Geotech report) LRFD Table 11.5.7-1
- Extreme Event I Limit State:
- Factored bearing resistance = Nominal bearing resistance from Geotech report X Resistance factor
- Resistance factor = 0.9 LRFD 11.8.6.1
- Factored bearing stress shall be computed using a uniform base pressure distribution over an effective width of footing determined in accordance with the provisions of LRFD 10.6.3.1 and 10.6.3.2, 11.10.5.4 and Figure 11.6.3.2-1 for foundation supported on soil or rock.
- B’ = L – 2e
- Where,
- L = Soil reinforcement length (For modular block use B in lieu of L as per LRFD 11.10.2-1)
- B’ = effective width of footing
- e = eccentricity
- Note: When the value of eccentricity e is negative then B´ = L.
- Where,
- Capacity/Demand ratio (CDR) for overturning shall be ≥ 1.0
- Capacity/Demand ratio (CDR) for eccentricity shall be ≥ 1.0
- Capacity/Demand ratio (CDR) for sliding shall be ≥ 1.0 LRFD 11.10.5.3 & 10.6.3.4
- Capacity/Demand ratio (CDR) for internal stability shall be ≥ 1.0
- Eccentricity, (e) Limit for Strength Limit State: LRFD 11.6.3.3 & C11.10.5.4
- For foundations supported on soil or rock, the location of the resultant of the reaction forces shall be within the middle two-thirds of the base width, L or (e ≤ 0.33L).
- Eccentricity, (e) Limit for Strength Limit State: LRFD 11.6.3.3 & C11.10.5.4
- Eccentricity, (e) Limit for Extreme Event I (Seismic): LRFD 11.6.5.1
- For foundations supported on soil or rock, the location of the resultant of the reaction forces shall be within the middle two-thirds of the base width, L or (e ≤ 0.33L) for γEQ = 0.0 and middle eight-tenths of the base width, L or (e ≤ 0.40L) for γEQ = 1.0. For γEQ between 0.0 and 1.0, interpolate e value linearly between 0.33L and 0.40L. For γEQ refer to LRFD 3.4.
- Eccentricity, (e) Limit for Extreme Event I (Seismic): LRFD 11.6.5.1
- Note: Seismic design shall be performed for γEQ = 0.5
- Eccentricity, (e) Limit for Extreme Event II:
- For foundations supported on soil or rock, the location of the resultant of the reaction forces shall be within the middle eight-tenths of the base width, L or (e ≤ 0.40L).
- Eccentricity, (e) Limit for Extreme Event II:
General Guidelines
- Drycast modular block wall (DMBW-MSE) systems are limited to a 10 ft. height in one lift.
- Wetcast modular block wall (WMBW-MSE) systems are limited to a 15 ft. height in one lift.
- For Drycast modular block wall (DMBW-MSE) systems and Wetcast modular block wall (WMBW-MSE) systems, top cap units shall be used and shall be permanently attached by means of a resin anchor system.
- For precast modular panel wall (PMPW-MSE) systems, capstone may be substituted for coping and either shall be permanently attached to wall by panel dowels.
- For precast modular panel wall (PMPW-MSE) systems, form liners are required to produce all panels. Using form liner to produce panel facing is more cost effective than producing flat panels. Standard form liners are specified on the MSE Wall Standard Drawings. Be specific regarding names, types and colors of staining, and names and types of form liner.
- MSE walls shall not be used where exposure to acid water may occur such as in areas of coal mining.
- MSE walls shall not be used where scour is a problem.
- MSE walls with metallic soil reinforcement shall not be used where stray electrical ground currents may occur as would be present near electrical substations.
- No utilities shall be allowed in the reinforced earth if future access to the utilities would require that the reinforcement layers be cut, or if there is a potential for material, which can cause degradation of the soil reinforcement, to leak out of the utilities into the wall backfill, with the exception of storm water drainage.
- All vertical objects shall have at least 4’-6” clear space between back of the wall facing and object for select granular backfill compaction and soil reinforcement skew limit requirements. For piles, see pipe pile spacers guidance.
- The interior angle between two MSE walls should be greater than 70°. However, if unavoidable, then place EPG 751.50 J1.41 note on the design plans.
- Drycast modular block wall (DMBW-MSE) systems and Wetcast modular block wall (WMBW-MSE) systems may be battered up to 1.5 in. per foot. Modular blocks are also known as “segmental blocks”.
- The friction angle used for the computation of horizontal forces within the reinforced soil shall be greater than or equal to 34°.
- For epoxy coated reinforcement requirements, see EPG 751.5.9.2.2 Epoxy Coated Reinforcement Requirements.
- All concrete except facing panels or units shall be CLASS B or B-1.
- The friction angle of the soil to be retained by the reinforced earth shall be listed on the plans as well as the friction angle for the foundation material the wall is to rest on.
- The following requirement shall be considered (from 2009_FHWA-NHI-10-024 MSE wall 132042.pdf, page 200-201) when seismic design is required:
- For seismic design category, SDC C or D (Zones 3 or 4), facing connections in modular block faced walls (MBW) shall use shear resisting devices (shear keys, pin, etc.) between the MBW units and soil reinforcement, and shall not be fully dependent on frictional resistance between the soil reinforcement and facing blocks. For connections partially dependent on friction between the facing blocks and the soil reinforcement, the nominal long-term connection strength Tac, should be reduced to 80 percent of its static value.
- Seismic design category and acceleration coefficients shall be listed on the plans for categories B, C and D. If a seismic analysis is required that shall also be noted on the plans. See EPG 751.50 A1.1 note.
- Plans note (EPG 751.50 J1.1) is required to clearly identify the responsibilities of the wall designer.
- Do not use Drycast modular block wall (DMBW-MSE) systems in the following locations:
- Within the splash zone from snow removal operations (assumed to be 15 feet from the edge of the shoulder).
- Where the blocks will be continuously wetted, such as around sources of water.
- Where blocks will be located behind barrier or other obstacles that will trap salt-laden snow from removal operations.
- Do not use Drycast modular block wall (DMBW-MSE) systems or Wetcast modular block wall (WMBW-MSE) systems in the following locations:
- For structurally critical applications, such as containing necessary fill around structures.
- In tiered wall systems.
- For locations where Drycast modular block wall (DMBW-MSE) systems and Wetcast modular block wall (WMBW-MSE) systems are not desirable, consider coloring agents and/or architectural forms using precast modular panel wall (PMPW-MSE) systems for aesthetic installations.
- For slab drain location near MSE Wall, see EPG 751.10.3.1 Drain Type, Alignment and Spacing and EPG 751.10.3.3 General Requirements for Location of Slab Drains.
- Roadway runoff should be directed away from running along face of MSE walls used as wing walls on bridge structures.
- Drainage:
- Gutter type should be selected at the core team meeting.
- When gutter is required without fencing, use Type A or Type B gutter (for detail, see Std. Plan 609.00).
- When gutter is required with fencing, use Modified Type A or Modified Type B gutter (for detail, see Std. Plan 607.11).
- When fencing is required without gutter, place in tube and grout behind the MSE wall (for detail, see MSE Wall Standard Drawings - MSEW, Fence Post Connection Behind MSE Wall (without gutter).
- Lower backfill longitudinal drainage pipes behind all MSE walls shall be two-6” (Min.) diameter perforated PVC or PE pipe (See Sec 1013) unless larger sizes are required by design which shall be the responsibility of the District Design Division. Show drainage pipe size on plans. Outlet screens and cleanouts should be detailed for any drain pipe (shown on MoDOT MSE wall plans or roadway plans). Lateral non-perforated drain pipes (below leveling pad) are permitted by Standard Specifications and shall be sized by the District Design Division if necessary. Lateral outlet drain pipe sloped at 2% minimum.
- Identify on MSE wall plans or roadway plans drainage pipe point of entry, point of outlet (daylighting), 2% min. drainage slopes in between points to ensure positive flow and additional longitudinal drainage pipes if required to accommodate ground slope changes and lateral drainage pipes if required by design.
- Adjustment in the vertical alignment of the longitudinal drainage pipes from that depicted on the MSE wall standard drawings may be necessary to ensure positive flow out of the drainage system.
- Identify on MSE wall plans or roadway plans the outlet ends of pipes which shall be located to prevent clogging or backflow into the drainage system. Outlet screens and cleanouts should be detailed for any drain pipe.
- For more information on drainage, see Drainage at MSE Walls.
MSE Wall Construction: Pipe Pile Spacers Guidance
For bridges not longer than 200 feet, pipe pile spacers or pile jackets shall be used at pile locations behind mechanically stabilized earth walls at end bents. Corrugated pipe pile spacers are required when the wall is built prior to driving the piles to protect the wall reinforcement when driving pile for the bridge substructure at end bents(s). Pile spacers or pile jackets may be used when the piles are driven before the wall is built. Pipe pile spacers shall have an inside diameter greater than that of the pile and large enough to avoid damage to the pipe when driving the pile. Use EPG 751.50 Standard Detailing Note E1.2a on bridge plans.
For bridges longer than 200 feet, pipe pile spacers are required and the pile spacer shall be oversized to mitigate the effects of bridge thermal movements on the MSE wall. For HP12, HP14, CIP 14” and CIP 16” piles provide 24-inch inside diameter of pile spacer for bridge movement. Minimum pile spacing shall be 5 feet to allow room for compaction of the soil layers. Use EPG 751.50 Standard Detailing Note E1.2b on bridge plans.
The bottom of the pipe pile spacers shall be placed 5 ft. min. below the bottom of the MSE wall leveling pad. The pipe shall be filled with sand or other approved material after the pile is placed and before driving. Pipe pile spacers shall be accurately located and capped for future pile construction.
Alternatively, for bridges shorter than or equal to 200 feet, the contractor shall be given the option of driving the piles before construction of the mechanically stabilized earth wall and placing the soil reinforcement and backfill material around the piling. In lieu of pipe pile spacers contractor may place pile jackets on the portion of the piles that will be in the MSE soil reinforced zone prior to placing the select granular backfill material and soil reinforcement. The contractor shall adequately support the piling to ensure that proper pile alignment is maintained during the wall construction. The contractor’s plan for bracing the pile shall be submitted to the engineer for review.
Piling shall be designed for downdrag (DD) loads due to either method. Oversized pipe pile spacers with sand placed after driving or pile jacket may be considered to mitigate some of the effects of downdrag (DD) loads. Sizing of pipe pile spacers shall account for pile size, thermal movements of the bridge, pile placement plan, and vertical and horizontal placement tolerances.
When rock is anticipated within the 5 feet zone below the MSE wall leveling pad, prebore into rock and prebore holes shall be sufficiently wide to allow for a minimum 10 feet embedment of pile and pipe pile spacer. When top of rock is anticipated within the 5 to 10 feet zone below the MSE wall leveling pad, prebore into rock to achieve a minimum embedment (pile only) of 10 feet below the bottom of leveling pad. Otherwise, the pipe pile spacer requires a minimum 5 feet embedment below the levelling pad. Consideration shall also be given to oversizing the prebore holes in rock to allow for temperature movements at integral end bents.
For bridges not longer than 200 feet, the minimum clearance from the back face of MSE walls to the front face of the end bent beam, also referred to as setback, shall be 4 ft. 6 in. (typ.) unless larger than 18-inch pipe pile spacer required. The 4 ft. 6 in. dimension serves a dual purpose:
- 1) the setback ensures that soil reinforcement is not skewed more than 15° for nut and bolt reinforcement connections to clear an 18-inch inside diameter pipe pile spacers by 6 inches per FHWA-NHI-10-24, Figure 5-17C, while considering vertical and horizontal pile placement tolerances
- 2) the setback helps to reduce the forces imparted on the MSE wall from bridge movements that typically are not accounted for in the wall design and cannot be completely isolated using a pipe pile spacer. Increasing the minimum setback shall be considered when larger diameter pile spacers are required or when other types of soil reinforcement connections are anticipated
For bridges longer than 200 feet, the minimum setback shall be 5 ft. 6 in. based on the use of 24-inch inside diameter of pipe pile spacers.
If interference with soil reinforcement is not a concern and the wall is designed for forces from bridge movement, the following guidance for pipe pile spacers clearance shall be used: pipe pile spacers shall be placed 36 in. clear min. from the back face of MSE wall panels to allow for proper compaction; 12 in. minimum clearance is required between pipe pile spacers and leveling pad and 18 in. minimum clearance is required between leveling pad and pile. For isolated pile (e.g, walls skewed from the bent orientation), the pipe pile spacer may be placed 18 in. clear min. from the back face of MSE wall panels.
MSE Wall Plan and Geometrics
- A plan view shall be drawn showing a baseline or centerline, roadway stations and wall offsets. The plan shall contain enough information to properly locate the wall. The ultimate right of way shall also be shown, unless it is of a significant distance from the wall and will have no effect on the wall design or construction.
- Stations and offsets shall be established between one construction baseline or roadway centerline and a wall control line (baseline). Some wall designs may contain a slight batter, while others are vertical. A wall control line shall be set at the front face of the wall, either along the top or at the base of the wall, whichever is critical to the proposed improvements. For battered walls, in order to allow for batter adjustments of the stepped level pad or variation of the top of the wall, the wall control line (baseline) is to be shown at a fixed elevation. For battered walls, the offset location and elevation of control line shall be indicated. All horizontal breaks in the wall shall be given station-offset points, and walls with curvature shall indicate the station-offsets to the PC and PT of the wall, and the radius, on the plans.
- Any obstacles which could possibly interfere with the soil reinforcement shall be shown. Drainage structures, lighting, or truss pedestals and footings, etc. are to be shown, with station offset to centerline of the obstacle, with obstacle size. Skew angles are shown to indicate the angle between a wall and a pipe or box which runs through the wall.
- Elevations at the top and bottom of the wall shall be shown at 25 ft. intervals and at any break points in the wall.
- Curve data and/or offsets shall be shown at all changes in horizontal alignment. If battered wall systems are used on curved structures, show offsets at 10 ft. (max.) intervals from the baseline.
- Details of any architectural finishes (formliners, concrete coloring, etc.).
- Details of threaded rod connecting the top cap block.
- Estimated quantities, total sq. ft. of mechanically stabilized earth systems.
- Proposed grade and theoretical top of leveling pad elevation shall be shown in constant slope. Slope line shall be adjusted per project. Top of wall or coping elevation and stationing shall be shown in the developed elevation per project. If leveling pad is anticipated to encounter rock, then contact the Geotechnical Section for leveling pad minimum embedment requirements.
MSE Wall Cross Sections
- A typical wall section for general information is shown.
- Additional sections are drawn for any special criteria. The front face of the wall is drawn vertical, regardless of the wall type.
- Any fencing and barrier or railing are shown.
- Barrier if needed are shown on the cross section. Barriers are attached to the roadway or shoulder pavement, not to the MSE wall. Standard barriers are placed along wall faces when traffic has access to the front face of the wall over shoulders of paved areas.
Drainage at MSE Walls
- Drainage Before MSE Wall
- Drainage is not allowed to be discharged within 10 ft. from front of MSE wall in order to protect wall embedment, prevent erosion and foundation undermining, and maintain soil strength and stability.
- Drainage Behind MSE Wall
- Internal (Subsurface) Drainage
- Groundwater and infiltrating surface waters are drained from behind the MSE wall through joints between the face panels or blocks (i.e. wall joints) and two-6 in. (min.) diameter pipes located at the base of the wall and at the basal interface between the reinforced backfill and the retained backfill.
- Excessive subsurface draining can lead to increased risk of backfill erosion/washout through the wall joints and erosion at the bottom of walls and at wall terminal ends. Excessive water build-up caused by inadequate drainage at the bottom of the wall can lead to decreased soil strength and wall instability. Bridge underdrainage (vertical drains at end bents and at approach slabs) can exacerbate the problem.
- Subsurface drainage pipes should be designed and sized appropriately to carry anticipated groundwater, incidental surface run-off that is not collected otherwise including possible effects of drainage created by an unexpected rupture of any roadway drainage conveyance or storage as an example.
- External (Surface) Drainage
- External drainage considerations deal with collecting water that could flow externally over and/or around the wall surface taxing the internal drainage and/or creating external erosion issues. It can also infiltrate the reinforced and retained backfill areas behind the MSE wall.
- Diverting water flow away from the reinforced soil structure is important. Roadway drainage should be collected in accordance with roadway drainage guidelines and bridge deck drainage should be collected similarly.
- Guidance
- ALL MSE WALLS
- 1. Appropriate measures to prevent surface water infiltration into MSE wall backfill should be included in the design and detail layout for all MSE walls and shown on the roadway plans.
- 2. Gutters behind MSE walls are required for flat or positive sloping backfills to prevent concentrated infiltration behind the wall facing regardless of when top of backfill is paved or unpaved. This avoids pocket erosion behind facing and protection of nearest-surface wall connections which are vulnerable to corrosion and deterioration. Drainage swales lined with concrete, paved or precast gutter can be used to collect and discharge surface water to an eventual point away from the wall. If rock is used, use impermeable geotextile under rock and align top of gutter to bottom of rock to drain. (For negative sloping backfills away from top of wall, use of gutters is not required.)
- District Design Division shall verify the size of the two-6 in. (min.) diameter lower perforated MSE wall drain pipes and where piping will daylight at ends of MSE wall or increase the diameters accordingly. This should be part of the preliminary design of the MSE wall. (This shall include when lateral pipes are required and where lateral drain pipes will daylight/discharge).
- BRIDGE ABUTMENTS WITH MSE WALLS
- Areas of concern: bridge deck drainage, approach slab drainage, approach roadway drainage, bridge underdrainage: vertical drains at end bents and approach slab underdrainage, showing drainage details on the roadway and MSE wall plans
- 3. Bridge slab drain design shall be in accordance with EPG 751.10.3 Bridge Deck Drainage – Slab Drains unless as modified below.
- 4. Coordination is required between the Bridge Division and District Design Division on drainage design and details to be shown on the MSE wall and roadway plans.
- 5. Bridge deck, approach slab and roadway drainage shall not be allowed to be discharged to MSE wall backfill area or within 10 feet from front of MSE wall.
- (Recommended) Use of a major bridge approach slab and approach pavement is ideal because bridge deck, approach slab and roadway drainage are directed using curbs and collected in drain basins for discharge that protect MSE wall backfill. For bridges not on a major roadway, consideration should be given to requiring a concrete bridge approach slab and pavement incorporating these same design elements (asphalt is permeable).
- (Less Recommended) Use of conduit and gutters:
- Conduit: Drain away from bridge and bury conduit daylighting to natural ground or roadway drainage ditch at an eventual point beyond the limits of the wall. Use expansion fittings to allow for bridge movement and consider placing conduit to front of MSE wall and discharging more than 10 feet from front of wall or using lower drain pipes to intercept slab drainage conduit running through backfill.
- Conduit and Gutters: Drain away from bridge using conduit and 90° elbow (or 45° bend) for smoothly directing drainage flow into gutters and that may be attached to inside of gutters to continue along downward sloping gutters along back of MSE wall to discharge to sewer or to natural drainage system, or to eventual point beyond the limits of the wall. Allow for independent bridge and wall movements by using expansion fittings where needed. See EPG 751.10.3.1 Type, Alignment and Spacing and EPG 751.10.3.3 General Requirements for Location of Slab Drains.
- 6. Vertical drains at end bents and approach slab underdrainage should be intercepted to drain away from bridge end and MSE wall.
- 7. Discharging deck drainage using many slab drains would seem to reduce the volume of bridge end drainage over MSE walls.
- 8. Drain flumes at bridge abutments with MSE walls do not reduce infiltration at MSE wall backfill areas and are not recommended.
- DISTRICT DESIGN DIVISION MSE WALLS
- Areas of concern: roadway or pavement drainage, MSE wall drainage, showing drainage details on the roadway and MSE wall plans.
- 9. For long MSE walls, where lower perforated drain pipe slope become excessive, non-perforated lateral drain pipes, permitted by Standard Specifications, shall be designed to intercept them and go underneath the concrete leveling pad with a 2% minimum slope. Lateral drain pipes shall daylight/discharge at least 10 ft. from front of MSE wall. Screens should be installed and maintained on drain pipe outlets.
- 10. Roadway and pavement drainage shall not be allowed to be discharged to MSE wall backfill area or within 10 feet from front of MSE wall.
- 11. For district design MSE walls, use roadway or pavement drainage collection pipes to transport and discharge to an eventual point outside the limits of the wall.
- Example: Showing drain pipe details on the MSE wall plans.
-
ELEVATION SHOWING DRAIN PIPE
-
Alternate option
-
Section A-A
Notes: |
E1. Excavation and Fill
(E1.1) Use when specified on the Design Layout.
- Existing roadway fill under the ends of the bridge shall be removed as shown. Removal of existing roadway fill will be considered completely covered by the contract unit price for roadway excavation.
Use one of the following two notes where MSE walls support abutment fill.
(E1.2a) [MS Cell] Use when pipe pile spacers are shown on plan details and bridge is 200 feet long or shorter. Add “See special provisions” to the pipe pile spacer callout and add table near the callout.
See special provisions.
Pile Encasement | Option Used (√) |
---|---|
Pipe Pile Spacer | |
Pile Jacket |
MoDOT Construction personnel will indicate the pile encasement used.
(E1.2b) Use note when pipe pile spacers are shown on plan details for HP12, HP14, CIP 14” and CIP 16” piles and bridge is longer than 200 feet. For larger CIP pile size modify following note and use minimum 6” larger pipe pile spacer diameter than CIP pile.
The pipe pile spacers shall have an inside diameter equal to 24 inches.
(E1.4) Use for fill at pile cap end bents. Use the first underlined portion when MSE walls are present. Use approach for semi-deep abutments.
- Roadway fill, exclusive of Select Granular Backfill for Structural Systems, shall be completed to the final roadway section and up to the elevation of the bottom of the concrete approach beam within the limits of the structure and for not less than 25 feet in back of the fill face of the end bents before any piles are driven for any bents falling within the embankment section.
REVISION REQUEST 4028
751.5.9.2.8 Development and Lap Splices
Development and Lap Splice Table of Contents |
---|
1. General |
2. Development and Lap Splices of Straight Deformed Bars in Tension |
3. Development and Lap Splices of Deformed Bars in Compression |
4. Development and Lap Splices of Standard Hooked Deformed Bars in Tension |
751.5.9.2.8.1 Development and Lap Splice General
Development of Straight Tension Reinforcement
Development lengths for tension reinforcement shall be calculated in accordance with LRFD 5.10.8.2.1.
Excess reinforcement modification factor (λer) and beneficial clamping stresses (βt component of λrc) of LRFD 5.10.8.2.1c may be used in situations where development length is difficult to attain. All other modification factors shall be used.
Temperature and shrinkage reinforcement are assumed to fully develop the specified yield stresses. Therefore the development length shall not be reduced by λer .
Development lengths for tension reinforcement have been tabulated on the following pages and include the modification factors except as described above.
Lap Splices of Tension Reinforcement (Straight and Hooked)
Lap splice lengths for tension reinforcement shall be calculated in accordance with LRFD 5.10.8.4.2a and 5.10.8.4.3a. Class B splices are preferred when possible, however it is permissible to use Class A when physical space is limited and Class A requirements are met. It should be noted that "required by analysis" of the Class A requirements is based on the stress encountered at the splice location, which is not necessarily the maximum stress used to design the reinforcement. Lap splice lengths for tension reinforcement have been tabulated on the following pages and include the development length modification factors as described above.
Development of Hooked Tension Reinforcement
Development lengths of hooked tension reinforcement shall be calculated in accordance with LRFD 5.10.8.2.4.
Excess reinforcement modification (λer) and beneficial clamping stresses (βt component of λrc) of LRFD 5.10.8.2.1c may be used in situations where development length is difficult to attain. The permissible 20 percent reduction of LRFD 5.10.8.2.4c may be used in situations where development length is difficult to attain and where required conditions are met. All other modification factors shall be used.
Development lengths of hooked tension reinforcement have been tabulated on the following pages and include the modification factors except as described above.
Development of Compression Reinforcement
Development lengths for compression reinforcement shall be calculated in accordance with LRFD 5.10.8.2.2.
Excess reinforcement modification factor (λer) of LRFD 5.10.8.2.2b may be used in situations where development length is difficult to attain. All other modification factors shall be used.
Development lengths for compression reinforcement have been tabulated on the following pages and include the modification factors except as described above.
Lap Splices of Compression Reinforcement
Lap splices lengths for compression reinforcement shall be calculated in accordance with LRFD 5.10.8.4.2a and 5.10.8.4.5a.
Splice lengths for compression reinforcement have been tabulated on the following pages.
751.5.9.2.8.2 Development and Lap Splices of Straight Deformed Bars in Tension
The values in the following table are based on Grade 60 bars (ƒy = 60 ksi) and may be adjusted for yield strengths up to 100 ksi. The final step in the table adjusts values for other material strengths. The values for Grade 40 bars are 45% (402/602) of the values in the table (not less than 12 inches), and values for 100 ksi bars are 280% (1002/602) of the values in the table.
751.5.9.2.8.3 Development and Lap Splices of Deformed Bars in Compression
The values in the following table are based on Grade 60 bars. Development lengths may be adjusted for yield strengths up to 100 ksi. Lap splice lengths for yield strengths greater than 60 ksi up to 100 ksi shall be calculated in accordance LRFD 5.10.8.4.5a. The final step in the table adjusts values for other material strengths. The values for Grade 40 bars are 40/60 of the values in the table (not less than 8 in. for development length and 12 in. for lap splice length).
751.5.9.2.8.4 Development and Lap Splices of Standard Hooked Deformed Bars in Tension
The hooked bar development length (ldh) is measured from the critical section to the outside edge of the hook.
The values in the following table are based on Grade 60 bars. Due to the complexity of the ldh formula, hooked bar development lengths will need to be calculated manually for ƒc other than 3 and 4 ksi and for ƒy other than 60 ksi. Transverse reinforcement requirements for other material strengths are specified at the bottom of the table.
751.8.3.2 Steel Reinforcement
Barrel Section
Standard boxes shall have main reinforcement placed perpendicular to the centerline of culvert. In any case, main reinforcement should not be skewed more than 25° from a line normal to the centerline of the culvert. (See LRFD 9.7.1.3.) The bar sizes, spacings and lengths given in the Standard Plans 703.17, 703.47 and 703.87 are applicable for uncoated steel reinforcement. Figure 751.8.3.2.1 shows a typical cross-section of standard box culvert and bar marks of steel reinforcement which are described below:
A1 bar - Steel reinforcement shall be designed for maximum positive moment in the top slab. This bar is placed transversely perpendicular to the centerline of culvert at the bottom of top slab. Place A1 bars into headwall or edge beam as close as practical.
A2 bar - Steel reinforcement shall be designed for maximum positive moment in the bottom slab. This bar is placed transversely perpendicular to the centerline of culvert at the top of bottom slab.


B1 bar - Steel reinforcement shall be designed for maximum combined axial load and moment at interior walls. This bar is placed vertical near stream faces of the wall. Minimum steel reinforcement of #5 bars spaced at 12” centers shall be provided. This bar should be extended into the top and bottom slabs. A hook bar may be required if the embedment length is insufficient due to slab thickness limitations. [[751.5 Standard Details#751.5.9.2.8.1 Development and Lap Splice General|EPG 751.5.9.2.8.1 Development and Lap Splice General] has information pertaining to development of tension reinforcement and hooks.
B2 bar – For culverts with bottom slabs, steel reinforcement shall be designed for the maximum positive moment in the exterior wall. For culverts on rock, steel reinforcement shall be designed for the maximum combined positive moment and axial load. This bar is placed vertical near the stream face of the wall. Minimum steel reinforcement of #5 bar spacing at 12” centers shall be provided. This bar should be extended into the top and bottom slabs. A hook bar may be required if the embedment length is insufficient due to slab thickness limitations. EPG 751.5.9.2.8.1 Development and Lap Splice General has information pertaining to development of tension reinforcement and hooks.
J3 bar - Steel reinforcement shall be designed for the maximum negative moment in the top corner of the culvert. This bar is placed vertical along the wall and transversely perpendicular to the centerline of culvert.
J4 bar - Steel reinforcement shall be designed for maximum negative moment in the bottom corner of the culvert. The J4 bar should also be designed for the maximum negative moment near the mid-height of the exterior wall. This bar is placed vertical along the wall and transversely perpendicular to the centerline of culvert.
H1 bar - Steel reinforcement shall be designed for the maximum negative moment in the top slab over the interior walls. This bar is placed transversely perpendicular to the centerline of culvert at the top of top slab. Its spacing is alternated with spacing of H2 bar. The length of H1 bar is longer than the length of H2 bar.
H2 bar - Steel reinforcement shall be designed for the maximum negative moment in the top slab over the interior walls. This bar is placed transversely perpendicular to the centerline of culvert at the top of top slab. Its spacing is alternated with spacing of H1 bar.
F bar - Longitudinal steel reinforcement provides for temperature and shrinkage control. Use #4 bars at about 14” centers for all interior faces. A minimal number of longitudinal bars in exterior faces are also provided primarily to aid in construction. This bar is placed parallel to the centerline of culvert. Additional longitudinal reinforcement may be required to provide for lateral distribution of concentrated live loads. For distribution of reinforcement, see EPG 751.8.2.6.
Headwalls and Edge Beams
Figure 751.8.3.2.2 shows a typical cross-section through headwalls and edge beams, and bar marks of steel reinforcement which are described below. The reinforcement values given below shall be considered standard for headwalls and minimum recommended values for edge beams.
If at least the minimum headwall dimensions are provided (see Fig. 751.8.3.2.2) the steel reinforcement in the top slab need not be increased over that required for barrel design. Otherwise, the width of the edge beam shall be taken as 3 feet and additional reinforcement in the top and bottom of slab is required.
D1 bar – Place 2- #8 bars at the top of headwalls or edge beams. These bars shall be placed along the headwall or edge beam.
D2 bar – Place these bars between D1 bars at the top of headwalls or edge beam and centered over interior walls. The total length of the bar is equal to two times larger value of 48 bar diameters or ¼ clear span length of headwall or edge beam. Neglect this bar for single span and if clear span length along headwall is less than or equal to 10’ for multiple spans. Otherwise, use a number of bars and sizes as indicated below:
- 2- #8 bars when 10’ 13’
- * 2- #9 bars when 13’
* The required area of steel reinforcement should be checked if clear span length along edge beam exceeds 20’.
H bar - Provide 4- #8 bars at bottom of headwalls or edge beam when edge beam is skewed. These bars shall be placed along the headwall or edge beam.
R1 bar – Provide minimum #5 bar spacing at 12” centers. This bar is placed perpendicular to longitudinal axis of upstream headwall or edge beam.
R2 bar - Provide minimum #5 bar spacing at 12” centers. This bar is placed perpendicular to longitudinal axis of upstream headwall or edge beam.
R3 bar - Provide minimum #5 bar spacing at 12” centers. This bar is placed perpendicular to longitudinal axis of downstream headwall or edge beam.

Wings
F bar - Longitudinal steel reinforcement provides for temperature and shrinkage control. Use #4 bars at about 14” centers for all interior faces. A minimal number of longitudinal bars in exterior faces are also provided primarily to aid in construction. This bar should be placed longitudinal along wing walls as shown in Figure 751.8.3.2.3. For wings on rock, longitudinal F bars should be designed using maximum moment and shear as specified in EPG 751.8.2.5.
G bar – Provide the same bar size and spacing as B1 or B2 bar for interior (Figure 751.8.3.2.3(b)) or exterior wall (Figure 751.8.3.2.3(a)), respectively.
J1 or J6 bar – Provide 2- #7 bars at each face of wing walls. These bars are provided for edge beam action and for support in extreme event scenarios, such as washout. The J6 callout is used for flared wings.
J5 bar – Steel reinforcement shall be designed for moment and shear based on Coulomb or Rankine active earth pressure. In any case, the provided steel area of J5 bar shall not be less than that provided by the adjoined wall.
Toe Walls
E1 bar – Provide 4- #5 bars and they should extend into wing walls as far as practical as shown in Figure 751.8.3.2.3. For wing walls on rock, these bars shall be extended 12” into the rock and grouted.



Collar Beams
Figure 751.8.3.2.4 shows steel reinforcement details of collar beams. The figure also shows that two layers of roofing felt shall be provided between culvert and collar beams. This will allow free lateral movement of adjoined sections.

-
(b)


For box culverts where collars are required and the precast option is used, precast concrete box culvert ties in accordance with Sec 733 and Std. Plan 733.00 shall be provided between all precast sections. |
Reinforcement Concrete Cover
The minimum concrete cover shall be 1-1/2” (clear) except the following:
- Top Slab
- The minimum concrete cover shall be 2” (clear) at top and 1-1/2” (clear) at bottom of the slab.
- Bottom Slab
- The minimum concrete cover shall be 1-1/2” (clear) at top and 3” (clear) at bottom of the slab.
- Walls and Wing Walls
- The minimum concrete cover shall be 2” (clear) at fill face and 1-1/2” (clear) at stream face.
- Wearing Surface
- A 1” monolithic protective surface shall be used on the bottom of bottom slab to compensate for pouring concrete on uneven earth surfaces. In special cases, where abrasion on the stream faces is a concern, a 1/2" monolithic wearing surface may be used on stream faces of walls and bottom slab. In the analysis, the protective surface and wearing surfaces (when considered) are included as part of the member thickness, but shall be excluded in the calculation of effective depth of the member for design.
751.10.1.14 Girder and Beam Haunch Reinforcement
General
- Steel Beams and Girders
- Haunch reinforcement consisting of #4 hairpin bars shall be provided where the embedment of existing studs into a new slab is less than 2 inches or for an excessive haunch where at centerline of beam or girder exceeds 3 inches.
- Prestressed Beams or Girders with Full Depth CIP Decks (Conventional or SIP forms)
- Haunch reinforcement consisting of #4 hairpin bars shall be provided when haunch at centerline of beam or girder exceeds:
- 3 inches for Type 2, 3, 4 girders
- 4 inches for Type 6, 7 and 8 girders (bulb-tee), NU girders and spread beams
- Prestressed Beams or Girders and Partial Depth CIP Decks (Prestressed Panels)
- Haunch reinforcement should not be required with precast prestressed panel decks due to joint filler limits.
Details
When possible, hairpin bars and tie bars shall be clearly shown on the section thru slab; otherwise, a part section showing hairpins shall be provided. Include these bars in the slab reinforcing steel quantities.

- (1) Top of slab to bottom of longitudinal bars.
- (2) Haunch limit specified above.
- (3) Use tie bars at the discretion of the Structural Project Manager or the Structural Liaison Engineer.
- (4) The bottom longitudinal bars should be shown to be used as tie bars or add a note allowing adjustment.
- (5) Add asterisked note when there is insufficient clearance or hairpins with varying vertical heights may be used.
Hairpin bars and tie bars shall be shown on the plan of slab. Splice lengths of the tie bars shall also be specified if required (19” for #4 bars). For deck replacements without a plan of slab the hairpin bars and tie bars shall be shown either on a part plan detail or in a table. Include these bars in the slab reinforcing steel quantities.

Hairpin bars and tie bars shall be included in the bill of reinforcing. Include these bars in the slab reinforcing steel quantities.
![]() |
“C” is based on the top horizontal legs located above the longitudinal bars of the bottom mat at the location of the maximum haunch. |
751.12.1.2.7 Details of Mounting Light Poles on Safety Barrier Curbs



Anchor bolts and nuts shall be in accordance with ASTM F1554 Grade 55. Anchor bolts, nuts and washers shall be fully galvanized, See 751.50.H4.2.2 for additional information.
Note to Detailer: Extend slab transverse steel to edge of slab in blister region often shown with an additional detail with the slab details.
Note: Conduit not shown for clarity.
751.12.1.3.2 Typical Section Reinforcement
The single R bar adds to the rigidity of the reinforcement during construction and it is believed to help prevent cracking. The single bar also appears to assist maintaining uniform reinforcement cover.
Splice length for epoxy coated horizontal #5 bars in barrier shall be 30 inches (25” for galvanized bars).
All bent bars are formed using stirrup bends except for the Type D #5-R1 bars.
All values may be used with both 2.0% and 3/16 inch-per-foot cross slopes.

751.12.1.3.3.1 Type D Ending on Integral End Bents
Use when distance between upper and lower construction joint in wings is at least 25½ inches.




751.12.1.3.3.2 Type H Ending on Integral End Bents
Use when distance between upper and lower construction joint in wings is at least 25½ inches.


751.12.1.3.3.3 Type D Ending on Shallow Integral End Bents
Use when distance between upper and lower construction joint in wings is less than 25½ inches.
Formulas extend bars to within 1½ʺ of lower construction joint.




751.12.1.3.3.4 Type H Ending on Shallow Integral End Bents
Use when distance between upper and lower construction joint in wings is less than 25½ inches.
Formulas extend bars to within 1½ʺ of lower construction joint.


751.12.1.3.3.5 Type D Ending on Non-Integral End Bents
Use when distance between upper and lower construction joint in wings is at least 25½ inches.




751.12.1.3.3.6 Type H Ending on Non-Integral End Bents
Use when distance between upper and lower construction joint in wings is at least 25½ inches.

751.12.1.3.3.7 Type D Ending at End of Slab (Redecks)
Splice length of epoxy coated #5 K12 and #5 K13 bars with #5 R-bars shall be 30 inches (25 inches for galvanized bars).




751.12.1.3.3.8 Type H Ending at End of Slab (Redecks)
Splice length of epoxy coated #5 K7 bars with #5 R-bars shall be 30 inches (25 inches for galvanized bars).


751.12.1.4.2 Typical Section Reinforcement
The single R bar adds to the rigidity of the reinforcement during construction and it is believed to help prevent cracking. The single bar also appears to assist maintaining uniform reinforcement cover.
Splice length for horizontal epoxy coated #5 bars in barrier curb shall be 30 inches (25 inches for galvanized bars).
All bent bars are formed using stirrup bends except for the R1 bars.

751.12.1.4.3 End of Barrier Reinforcement
See barrier ending on end bents sheets of the barrier standard drawings for the required details. The bars shown below are for barrier ending on wing walls; see barrier ending at end of slab sheet of the barrier standard drawings for reinforcement details for barrier ending on slabs.
Splice length of #5-K9 bars with #4 K-bars above wing walls shall be 31 inches (embedment of #5 bars controls over splice length of #4 bars).
All bent bars are formed using stirrup bends except for the K4 and K11 bars.
Ending on Integral End Bents and Semi-Deep Abutments
Use when distance between upper and lower construction joint in wings is at least 25½ inches.



- * On skewed integral end bents, if the end K3 bars do not meet the minimum 1 1/2" clearance from the front face of the diaphragm, a K12 bar shall be substituted.
- * Based on no wearing surface, adjust as needed. Example: Add 2ʺ for 2ʺ W.S.
- * Also based on 8½ʺ slab, adjust as needed. Example: Subtract 1ʺ for 7½ʺ slab
Ending on Shallow Integral End Bents
Use when distance between upper and lower construction joint in wings is less than 25½ inches.


Ending on Non-Integral End Bents
Use when distance between upper and lower construction joint in wings is at least 25½ inches.



751.12.1.6 Type A (32ʺ New Jersey Shaped Median)
Note: Use same grade reinforcing steel in barrier as in slab.
- Splice length for epoxy coated #5-R bars in barrier shall be 30 inches (25 inches for galvanized bars).
- Do not use this barrier over precast prestressed panels.

Twin Bridge Median Barrier Details

751.21.3.3.1 Spread Box Beams


Bending Diagrams
Dimensions shown are out to out. Use symmetry for dimensions not shown. Use "ɑ" bars for squared-end beams. Use "b" bars for skewed-end beams.

![]() |
![]() |
For beams that have excessive haunch or beam steps, create new S2 bars and adjust heights in one-inch increments or provide #4 hairpin bars in accordance with EPG 751.10.1.14 Girder and Beam Haunch Reinforcement to ensure at least 2-inch embedment into slab.
751.21.3.6.3 Reinforcement
751.22.2.3 Flexure
Flexure capacity of girders shall be determined as the following.
Flexural resistance at strength limit state
Where:
= | Flexural resistance | |
= | Nominal flexural resistance | |
= | Total factored moment from Strength I load combination | |
= | Flexural resistance factor as calculated in LRFD 5.5.4.2 |
Negative moment reinforcement design
P/S I-girder shall be designed as a reinforced concrete section at regions of negative flexures (i.e., negative moments).
At least one-third of the total tensile reinforcement provided for negative moment at the support shall have an embedment length beyond the point of inflection not less than the specified development length of the bars used.
Slab longitudinal reinforcement that contributes to making the precast beam continuous over an intermediate bent shall be anchored in regions of the slab that can be shown to be crack-free at strength limit states. This reinforcement anchorage shall be staggered. Regular longitudinal slab reinforcement may be utilized as part of the total longitudinal reinforcement required.
Effective Slab Thickness
An effective slab thickness shall be used for design by deducting from the actual slab thickness a 1” integral, sacrificial wearing surface.
Design A1 reinforcement in the top flange
The A1 reinforcement shall resist the tensile force in a cracked section computed on the basis of an uncracked section.
For I girders and bulb-tee girders, A1 reinforcement shall consist of deformed bars (minimum #5 for Type 2, 3 and 4 and minimum #6 for Type 6, 7 and 8).
For NU girders, A1 reinforcement shall consist of the four 3/8-inch diameter reinforcement support strands with deformed bars added only as needed. The WWR in the top flange shall not be used for A1 reinforcement because there is insufficient clearance to splice the WWR.
See guidance on Bridge Standard Drawings (Prestressed I-Girders - PSI) for required lap lengths, if required.
Required steel area is equal to:
Where:
= , allowable tensile stress of mild steel, (ksi) | |
= Resultant of total tensile force computed on the basis of an uncracked section, (kips) |
Limits for reinforcement
The following criteria shall be considered only at composite stage.
Minimum amount of prestressed and non-prestressed tensile reinforcement shall be so that the factored flexural resistance, Mr, is at least equal to the lesser of:
- 1) Mcr LRFD Eq. 5.6.3.3-1
- 2) 1.33Mu
Where:
Mcr | = | Cracking moment, (kip-in.) |
Mu | = | Total factored moment from Strength I load combination, (kip-in.) |
751.22.3.7.2 Reinforcement
The reinforcement shall be detailed on the plan sheets for closed concrete intermediate diaphragms as shown below except:
- Bar marks revised as required.
- Abbreviations used as required.
- Add "(Typ.)" to dimensions and leader notes as appropriate.
All U bar reinforcement shall use stirrup bends.
All reinforcement in diaphragms shall be epoxy coated, except coating of dowel bars shall match the coating of intermediate bent reinforcement.
Coil ties and rods shall also be shown in the section near the diaphragm and the horizontal section near the top of diaphragm in accordance with EPG 751.22.3.10 Coil Inserts and Tie Rods.
Unless specified the details shown are for the same girder heights within a continuous girder series.
I Girders Type 2, 3, 4 and 6
Bulb-Tee Girders Type 7 and 8
![]() |
![]() | |
SECTION NEAR DIAPHRAGM (Normal to centerline of girders) |
||
![]() | ||
SECTION A-A (Skewed over 25°) | ||
![]() |
![]() |
Detailing Guidance: Green items are guidance only and shall not be shown on the plans. See Section A-A for I girders type 2, 3, 4 and 6 for differences in strand tie bars for bents skewed up to 25°. Bars will need to clear any shear blocks required for expansion bents. (ɑ) X equals layers of bent up strands (omit quantity if one layer). (b) 19 inches minimum for #4 bars and full available width for #6 bars. (c) 11" may be used if required for spacing. |
ELEVATION C-C | SECTION B-B (Normal) (Fixed Bent) |
NU Girders
NU 53 girders are shown in the following details. The details for other NU girder types are similar.
![]() |
![]() | ||||||||||||||||||||||||
SECTION NEAR DIAPHRAGM (Normal to centerline of girders) |
|||||||||||||||||||||||||
![]() | |||||||||||||||||||||||||
SECTION A-A (Skewed over 25°) | |||||||||||||||||||||||||
![]() |
![]() |
| |||||||||||||||||||||||
ELEVATION C-C | SECTION B-B (Normal) Fixed Bent | ||||||||||||||||||||||||
Detailing Guidance: Green items are guidance only and shall not be shown on the plans. See Section A-A for I girders type 2, 3, 4 and 6 for differences in strand tie bars for bents skewed up to 25°. Bars will need to clear any shear blocks required for expansion bents. (ɑ) X equals layers of bent up strands (omit quantity if one layer). (b) 19 inches minimum for #4 bars and full available width for #6 bars. |
Change in Girder Height
The following details are based on I Girders Type 2, 3, 4 and 6. The details are appropriate for bulb-tee and NU girders by substituting the appropriate reinforcing details from above. The reinforcement is that of the taller girder with additional #6 bars located under the shorter girder. The section near the diaphragm shall be from the perspective of the shorter girders. The differences from uniform girder height details are highlighted.
![]() |
![]() | ||||||||||||||||||
SECTION NEAR DIAPHRAGM (e) (Looking back station) (Normal to centerline of girders) |
|||||||||||||||||||
![]() | |||||||||||||||||||
SECTION A-A (Skewed over 25°) | |||||||||||||||||||
![]() |
Detailing Guidance: Green items are guidance only and shall not be shown on the plans. See Section A-A for I girders type 2, 3, 4 and 6 for differences in strand tie bars for bents skewed up to 25°. Bars will need to clear any shear blocks required for expansion bents. (ɑ) X equals layers of bent up strands (omit quantity if one layer). (b) 19 inches minimum for #4 bars and full available width for #6 bars. (c) Subtract one row for Type 2 and 3. Add one row for Type 6. (d) For squared bents replace H26 with H25. (e) Only required if shorter girders are down station from taller girders. |
| |||||||||||||||||
ELEVATION B-B (Normal) (Fixed Bent) Change in girder heights not allowed at expansion bents. |
751.22.3.8.2 Reinforcement
The reinforcement shall be detailed on the plan sheets for open concrete intermediate diaphragms as shown below except:
- Bar marks revised as required.
- Abbreviations used as required.
- Add "(Typ.)" to dimensions and leader notes as appropriate.
All U bar reinforcement shall use stirrup bends.
All reinforcement in diaphragms shall be epoxy coated.
Coil ties and rods shall also be shown in the section near the diaphragm and the horizontal section near the top of diaphragm in accordance with EPG 751.22.3.10 Coil Inserts and Tie Rods.
I Girders Type 2, 3, 4 and 6
![]() | |||||||||||||||||||||||||
SECTION NEAR DIAPHRAGM (Normal to centerline of girders) | |||||||||||||||||||||||||
![]() | |||||||||||||||||||||||||
SECTION A-A | |||||||||||||||||||||||||
![]() |
![]() |
| |||||||||||||||||||||||
SECTION B-B (Normal) |
|||||||||||||||||||||||||
Detailing Guidance: Green items are guidance only and shall not be shown on the plans. U21 are varied bars. (ɑ) Hook ends if length of bar is less than 88" (ℓd = 44"). (b) For squared bents replace with pairs of U23 bars. (c) X equals layers of bent up strands (omit quantity if one layer). (d) 19 inches minimum for #4 bars and full available width for #6 bars. |
Bulb-Tee Girders Type 7 and 8
![]() |
![]() | |
SECTION NEAR DIAPHRAGM (Normal to centerline of girders) |
||
![]() | ||
SECTION A-A | ||
![]() |
![]() |
Detailing Guidance: Green items are guidance only and shall not be shown on the plans. U31, U35, U36 & U37 are varied bars. (ɑ) Hook ends if length of bar is less than 88" (ℓd = 44"). (b) Replace with pairs of U36 bars for squared bents. (c) X equals layers of bent up strands (omit quantity if one layer). (d) 19 inches minimum for #4 bars and full available width for #6 bars. |
ELEVATION C-C | SECTION B-B (Normal) |
NU Girders
NU 53 girders are shown in the following details. The details for other NU girder types are similar.
![]() |
![]() | ||||||||||||||||||||||||||||||||||||||||
SECTION NEAR DIAPHRAGM (Normal to centerline of girders) |
|||||||||||||||||||||||||||||||||||||||||
![]() | |||||||||||||||||||||||||||||||||||||||||
SECTION A-A | |||||||||||||||||||||||||||||||||||||||||
![]() |
![]() |
| |||||||||||||||||||||||||||||||||||||||
ELEVATION C-C | SECTION B-B (Normal) |
||||||||||||||||||||||||||||||||||||||||
Detailing Guidance: Green items are guidance only and shall not be shown on the plans. U41, U44, U46 & U47 are varied bars. (ɑ) Hook ends if length of bar is less than 88" (ℓd = 44"). (b) For squared bents replace with pairs of U23 bars. (c) X equals layers of bent up strands (omit quantity if one layer). (d) 19 inches minimum for #4 bars and full available width for #6 bars. (e) NU 78 requires another row. |
751.22.3.9.2 Reinforcement
The reinforcement shall be detailed on the plan sheets for concrete end diaphragms as shown below except:
- Bar marks revised as required.
- Abbreviations used as required.
- Add "(Typ.)" to dimensions and leader notes as appropriate.
All U bar reinforcement shall use stirrup bends.
All reinforcement in diaphragms shall be epoxy coated.
Coil ties and rods shall also be shown in the section near the diaphragm and the horizontal section near the top of diaphragm in accordance with EPG 751.22.3.10 Coil Inserts and Tie Rods.
I Girders Type 2, 3, 4 and 6
![]() | |||||||||||||||||||||||||
SECTION NEAR DIAPHRAGM (Normal to centerline of girders) | |||||||||||||||||||||||||
![]() | |||||||||||||||||||||||||
SECTION A-A | |||||||||||||||||||||||||
![]() |
![]() |
![]() | |||||||||||||||||||||||
Small Expansion Device (End Bend with Sliding Slab Similar) |
Finger Plate Expansion Device | ||||||||||||||||||||||||
SECTION B-B (Normal) | |||||||||||||||||||||||||
Detailing Guidance: Green items are guidance only and shall not be shown on the plans. Use full available width for lap of all stirrup bars except the upper legs at a finger plate expansion device are developed as specified. U21 and U27 are varied bars. (ɑ) Hook ends of H200 bars if length is less than 66" (ℓd = 33"). (b) For squared bents replace both with Pr.-#4-U23. (c) For squared bents replace U24 with U22. (d) For finger plate expansion devices replace with #4-U20 & #4-U26. (e) For finger plate expansion devices replace with #6-U21 & #6-U27. |
|
Bulb-Tee Girders Type 7 and 8
![]() | ||
SECTION NEAR DIAPHRAGM (Normal to centerline of girders) | ||
![]() | ||
SECTION A-A | ||
![]() |
![]() | |
Detailing Guidance: Green items are guidance only and shall not be shown on the plans. See Section B-B for I Girders for differences due to a finger plate expansion device. Lap #4 stirrup bars 19 inches if available otherwise lap all stirrup bars full available width. H301, U301, U304, U306, U308 and U310 are varied bars. (ɑ) Hook ends of H300 bars if length is less than 66" (ℓd = 33"). (b) For squared bents replace both with Pr.-#4-U306. (c) For squared bents replace U307 with U303, U308 with U304 and U309 with U305. | ||
SECTION B-B (Normal) |
NU Girders
NU 53 girders are shown in the following details. The details for other NU girder types are similar.
![]() | |||||||||||||||||||||||||||||||||||||||||
SECTION NEAR DIAPHRAGM (Normal to centerline of girders) | |||||||||||||||||||||||||||||||||||||||||
![]() | |||||||||||||||||||||||||||||||||||||||||
SECTION A-A | |||||||||||||||||||||||||||||||||||||||||
![]() |
![]() |
| |||||||||||||||||||||||||||||||||||||||
SECTION B-B (Normal) |
|||||||||||||||||||||||||||||||||||||||||
Detailing Guidance: Green items are guidance only and shall not be shown on the plans. See Section B-B for I Girders for differences due to a finger plate expansion device. Lap #4 stirrup bars 19 inches if available otherwise lap all stirrup bars full available width. H401, U401, U404, U406, U408 and U410 are varied bars. Do not vary U403 and U407 bars. Horizontal legs are controlled by the minimum allowable space on each end of diaphragm. (ɑ) Hook ends of H400 bars if length is less than 66" (ℓd = 33"). (b) For squared bents replace both with 2 Pr.-#4-U406. (c) For squared bents replace U407 with U403, U408 with U404 and U409 with U405. (d) NU 78 requires another row of H401 and H402 (4-#6-H401 & 3-#6-H402 in Section A-A). |
751.22.3.9.3 Closed Diaphragm
Use only when expansion device connects prestressed girder series and steel girder series, and laminated neoprene pads are used under the prestressed girders in accordance with expansion limits of these bearings and only with the approval of the Structural Project Manager or Structural Liaison Engineer.
The simplified detail below is for I girders. The actual details required on the plans can be developed for all girder types by substituting the dimensions and reinforcement of the corresponding section near the diaphragm detail of EPG 751.22.3.7 and the dimensions from the corresponding Section A-A of EPG 751.22.3.9.1 Dimensions.
![]() |
![]() |
SECTION THRU CLOSED END DIAPHRAGM |
751.31.3.1 Beam Cap
![]() |
![]() |
![]() | |
PART ELEVATION | SECTION A-A | SECTION B-B | |
(Single Stirrups) | |||
![]() |
![]() |
![]() | |
PART PLAN | SECTION A-A | SECTION B-B | |
(Double Stirrups) | |||
![]() |
![]() | ||
TRANSVERSE BEAM STEPS OVER 3 INCHES (Also, steps accumulating over 3 inches) |
SLOPED BEAMS (Steps over 3 inches on high side) | ||
![]() |
![]() |
(1) #4 @ 12” cts. (Min.) See EPG 751.5.9.2.8 for development and lap splice lengths not given or lengths for See EPG 751.5.9.2.2 for epoxy coated reinforcement requirements. See EPG 751.13.1.4 for details of protective coating and sloping top of beam to drain | |
Over 3 Inches Thru 12 Inches | Over 12 Inches | ||
LONGITUDINAL BEAM STEPS | |||
![]() | |||
REINFORCEMENT UNDER BEARINGS |
751.31.3.2 Column
![]() |
![]() | |
MINIMUM SPACING AT LAP SPLICES | ALTERNATE DOWEL PLACEMENT | |
* | Use alternate detail only with approval of Structural Project Manager and then design column reinforcement using the smaller ring diameter. | |
A = | 4 1/2” minimum spacing center-to-center. | |
B = | 2” clear spacing for bar sizes thru #10. | |
2 1/2” clear spacing for bar sizes #11 and #14. | ||
3 1/2” clear spacing for bar size #18. | ||
![]() | ||
STIRRUP LAP DETAIL AND STAGGER NOTE | ||
Lap splices for closed circular ties shall be provided and staggered in accordance with LRFD 5.10.6.3. | ||
Lap length of 1.3 ld (or Class B) for closed stirrup/ties shall be provided in accordance with LRFD 5.11.2.6.4. | ||
Lap length for #4 stirrup bars (4” min. spacing, f’c = 3 ksi, and clear cover = 1½”) equals 24” for uncoated bars and 28” for epoxy coated bars. | ||
For lap length for other scenarios, see EPG 751.5.9.2.8 Development and Lap Splices. |
Column Diameter | Minimum Reinforcement2,3 | Minimum Lap Splice | |
---|---|---|---|
Uncoated (f’c = 3ksi) (Cl. = 1½”) |
Epoxy Coated (f’c = 3ksi) (Cl. = 1½”) | ||
3’-0” | By Design | NA | NA |
3’-6” | By Design | NA | NA |
4’-0” | #6 @ 5” | 47” | 61” |
4’-6” | #5 @ 5” | 34” | 44” |
5’-0” | #4 @ 5” | 24” | 28” |
5’-6” | #4 @ 10” | 24” | 28” |
6’-0” | #4 @ 12” | 24” | 28” |
1 See EPG 751.2.2.6 Other Loads to determine if a pier requires design for collision loads.
3 The shear reinforcement tabulated is adequate for collision but may not be adequate for other design |
- Columns shall be reinforced using stirrup ties, unless excessive reinforcement is required, in which case spirals shall be used.
- Show spiral details of Fig. 751.9.3.1.7.4 on the bridge plans if spirals are used for bridge in non-seismic area. Anchorage of spiral reinforcement shall be provided by 1 ½ extra turns of spiral reinforcement at each end of the spiral unit.
![]() |
(1) Location 2 development length. (2) Check clearance to concrete piles. See EPG 751.5.9.2.8 for development and lap splice lengths not given or lengths for scenarios other than those shown. Provide standard hooks if required. See EPG 751.5.9.2.2 for epoxy coated reinforcement requirements. |
751.31.3.3 Web Beam
![]() |
![]() | |
PART ELEVATION | SECTION THRU WEB BEAM | |
![]() |
(1) L/4 + d, but not less than theoretical cut-off + development length.
(2) Location 2 development length, 4” to 12” spacing, 1½” clear, f'c = 3 ksi:
(3) Location 1 development length, f'c = 3 ksi:
(4) Location 2 development length. (5) Location 2 Class B lap splice. (6) Maximum spacing shall be 6" or 1/5 development length for noncontact lap splice. See EPG 751.5.9.2.8 for development and lap splice lengths See EPG 751.5.9.2.2 for epoxy coated reinforcement requirements. | |
VARIABLE DIAMETER COLUMN (Without Seismic Detailing) |
751.31.3.4 Tie Beam
![]() |
![]() | |
CONSTANT COLUMN DIAMETER | CHANGE IN COLUMN DIAMETER | |
PART ELEVATION AT TIE BEAM AND COLUMN | ||
![]() |
(1) Location 1 development length, f'c = 3 ksi: See EPG 751.5.9.2.8 for development and lap splice lengths not given or for lengths See EPG 751.5.9.2.2 for epoxy coated reinforcement requirements. | |
SECTION THRU TIE BEAM |
751.31.3.5 Hammer Head Type
![]() |
![]() |
PART PLAN | SECTION A-A |
![]() |
![]() |
PART ELEVATION | SECTION B-B |
(1) #4 @ 12” cts. (Min.)
(2) Hook bars if cantilever is less than the required Location 1 development length. (3) Location 2 development length. (4) Location 2 Class B lap splice, f'c = 3 ksi:
(5) Location 1 Class B lap splice, f'c = 3 ksi:
(6) See EPG 751.2.2.6 and 751.31.2.2 for collision requirements. (7) See LRFD 5.10.6.3 for tie requirements. See EPG 751.5.9.2.8 for development and lap splice lengths not given or for lengths See EPG 751.5.9.2.2 for epoxy coated reinforcement requirements. |
751.32.4.1 Typical Pile Cap Bent
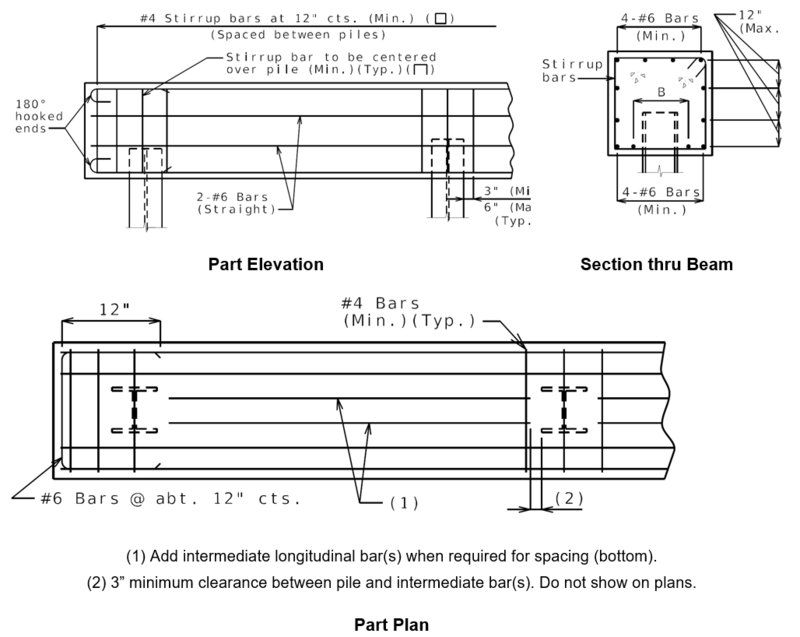
Note: | Locate #4 bars "![]() ![]() |
For epoxy coated reinforcement requirements, see EPG 751.5.9.2.2 Epoxy Coated Reinforcement Requirements. Details of protective coating and sloping top of beam to drain shall be used when below an expansion device. | |
When dimension “B” is required to be greater than 15” to clear piles by 1 ½”, typical when HP14 and CIP14 or larger diameter piles are used, add intermediate longitudinal bar(s) between piles. The spacing between intermediate bar(s) and full length bars shall not be greater than required by crack control provisions. Ends of intermediate bar(s) shall be hooked. |
![]() |
![]() |
(1) 6” (Max.), add #6 bars as needed.
See EPG 751.5.9.2.8 for development and lap splice lengths not given or |
751.35.4.1 Wide Flange Beams & Plate Girders
![]() | ||||
Part Section Near End Bent | ||||
![]() |
![]() | |||
Section A-A | Section B-B | Section C-C | Section D-D | |
![]() |
![]() | |||
Alternate Section A-A | Alternate Section B-B | Alternate Section C-C | Alternate Section D-D | |
Detailing Guidance: | ||||
Green items are guidance only and shall not be shown plans. | ||||
Place all U bars and V pairs parallel to centerline roadway. | ||||
Keep 1 1/2" clearance between the piles and the U1 or U2 bars. | ||||
Keep 1 1/2" clearance between the beams or girders and the U1 or V1 bars. | ||||
Keep 1 1/2" clearance between the angles of girder chairs and the U2 or U3 bars. | ||||
Replace U1 bars with U3 bars at piles under beams or girders. | ||||
Replace U1 bars with V1 bars at piles between beams or girders. | ||||
When dimension “A” is required to be greater than 15” to clear piles by 1 ½”, typical when HP14 and CIP14 or larger diameter piles are used, add intermediate longitudinal bar(s) between piles. The spacing between intermediate bar(s) and full length bars shall not be greater than required by crack control provisions. Ends of intermediate bar(s) shall be hooked. | ||||
See EPG 751.50 G1 Concrete Bents for appropriate notes to be placed with details. | ||||
(1) #6-U bar (![]() | ||||
(2) U4 bars (![]() ![]() ![]() stirrup hooks may be required for U4 bars ( ![]() minus 1” clear. | ||||
(3) U1 bars (![]() lap length requirement across length of diaphragm. For shallow beams stirrup hooks may be required for U1 bars ( ![]() bars ( ![]() | ||||
(4) Stirrups shall clear step by 1 1/2" minimum, if not lengthen step or skew step. | ||||
(5) #6-V bars at no more than 9” centers at the end of girders or beams. | ||||
(6) #5-U bars (15”H x 24”V) @ about 12" centers placed parallel to centerline roadway. When approach slab haunch is expected to be greater than 18” at the roadway crown at the end of slab, slope the approach slab notch providing 12” of constant approach slab haunch or with SPM or SLE approval greater than 18” approach slab haunch may be used but increase vertical leg length of #5-U bars to ensure 12” minimum embedment. For shallow beams where 12” embedment is not available adjust length of vertical leg and extend to top of beam minus 1” clear. | ||||
(7) With SPM or SLE approval a 24” splice may be used in combination with specifying 2” cover to U bars and V bars if doing so avoids the need for using hooked bars. | ||||
(8) See tables for 1 1/16" round hole spacing for #6-H bars. | ||||
(9) Same number of bars as 1 1/16" round holes in beam or girder. | ||||
(10) Add intermediate longitudinal bar(s) when required for spacing. Keep 3” minimum clearance between the pile and intermediate longitudinal bar(s). |
751.35.4.2 Prestressed I-Girders, Bulb-Tee Girders and NU-Girders
![]() | ||||
Part Section Near End Bent | ||||
![]() |
![]() | |||
Section A-A | Section B-B | Section C-C | Section D-D | |
![]() |
![]() | |||
Alternate Section A-A | Alternate Section B-B | Alternate Section C-C | Alternate Section D-D | |
Detailing Guidance: | ||||
Green items are guidance only and shall not be shown plans. | ||||
Place all U bars and V pairs parallel to centerline roadway. | ||||
Keep 1 1/2" clearance between the piles and the U1 or U2 bars. | ||||
Keep 1 1/2" clearance between the beams or girders and the U1 or V1 bars. | ||||
Keep 1 1/2" clearance between the angles of girder chairs and the U2 or U3 bars. | ||||
Replace U1 bars with U3 bars at piles under beams or girders. | ||||
Replace U1 bars with V1 bars at piles between beams or girders. | ||||
When dimension “A” is required to be greater than 15” to clear piles by 1 ½”, typical when HP14 and CIP14 or larger diameter piles are used, add intermediate longitudinal bar(s) between piles. The spacing between intermediate bar(s) and full length bars shall not be greater than required by crack control provisions. Ends of intermediate bar(s) shall be hooked. | ||||
See EPG 751.50 G1 Concrete Bents for appropriate notes to be placed with details. | ||||
(1) #6-U bar (![]() | ||||
(2) U4 bars (![]() ![]() ![]() stirrup hooks may be required for U4 bars ( ![]() minus 1” clear. | ||||
(3) U1 bars (![]() lap length requirement across length of diaphragm. For shallow beams stirrup hooks may be required for U1 bars ( ![]() bars ( ![]() | ||||
(4) Stirrups shall clear step by 1 1/2" minimum, if not lengthen step or skew step. | ||||
(5) #6-V bars at no more than 9” centers at the end of girders or beams. | ||||
(6) #5-U bars (15”H x 24”V) @ about 12" centers placed parallel to centerline roadway. When approach slab haunch is expected to be greater than 18” at the roadway crown at the end of slab, slope the approach slab notch providing 12” of constant approach slab haunch or with SPM or SLE approval greater than 18” approach slab haunch may be used but increase vertical leg length of #5-U bars to ensure 12” minimum embedment. For shallow beams where 12” embedment is not available adjust length of vertical leg and extend to top of beam minus 1” clear. | ||||
(7) With SPM or SLE approval a 24” splice may be used in combination with specifying 2” cover to U bars and V bars if doing so avoids the need for using hooked bars. | ||||
(8) Add intermediate longitudinal bar(s) when required for spacing. Keep 3” minimum clearance between the pile and intermediate longitudinal bar(s). |
751.35.4.3 Wing Reinforcement
![]() |
![]() |
Elevation Of Wing | Typical Section Thru Wing |
![]() | |
Part Plan (Squared) | |
![]() | |
Part Plan (Skewed) | |
Detailing Guidance: | |
Green items are guidance only and shall not be shown plans. | |
Bar marks shown are for these details only. Vary as needed. | |
K bars not shown in the Elevation of Wing for clarity. For details of K bars, see EPG 751.12.1.4.3 End of Barrier Reinforcement for Type B barrier and EPG 751.12.1.3.3 End of Barrier Reinforcement for Type D and H barriers. | |
See EPG 751.35.3.3 for chamfer detail. | |
(a) Use dimension that provides a minimum of 3" center to center spacing between #6 bars placed horizontally and #8 bars placed with grade. See SPM or SLE if spacing at one end exceeds 8 inches due to grade. | |
(b) Use construction joint on steel structures only. | |
(c) 6 3/8” min and 11 3/8” max. If unable to get dimension to fall within this range using 8-inch centers, then use 6 3/8” and use “@ abt. 8” cts.” | |
(d) Use 66.5” for obtuse corner of bents skewed 55 degrees or greater. | |
(e) Use 54.5” for obtuse corner of bents skewed 55 degrees or greater. | |
(f) See 751.50_Standard_Detailing_Notes#G1._Concrete_Bents EPG 751.50 G1 Concrete Bents for note (G1.7) required for the #6-F bars. | |
(g) Use 90 degree standard hook in seismic areas. | |
(h) Adjust as needed if girder web prevents proper placement of bars (i.e., if ALL bars would need to be bent in field according to note G1.7). Rotate leg 90° for box beams. If necessary, the leg may be rotated 90° for other prestressed girder shapes. |
H10a. Cast-In-Place Permanent Barrier
The following notes shall be placed in the General Notes on the elevation sheet.
(H10.0.1) Use note if slip forming is allowed. Add asterisk to all C-bar leader notes and the one fiberglass bar leader note in the elevation of barrier.
- * Slip-formed option only.
(H10.0.2) Both methods may be used unless otherwise specified on Bridge Memorandum.
- Conventional forming or slip forming may shall be used. Saw cut joints may be used with conventional forming.
(H10.1) Exclude underlined part for single span bridges.
- Top of barrier shall be built parallel to grade with barrier joints (except at end bents) normal to grade.
(H10.2)
- All exposed edges of barrier shall have either a 1/2-inch radius or a 3/8-inch bevel, unless otherwise noted.
(H10.3)
- Payment for all concrete and reinforcement, complete in place, will be considered completely covered by the contract unit price for Type A B C D H Barrier per linear foot.
(H10.4)
- Concrete in barrier shall be Class B-1.
(H10.5) Use for Type B, D or H barrier. Include “left” or ”right” and exclude “for each structure” when barriers on each side of the bridge are not the same type.
- Measurement of barrier is to the nearest linear foot for each structure, measured along the left right outside top of slab from end of wing to end of wing slab to end of slab.
(H10.7) Use for Type A or C barriers.
- Measurement of barrier is to the nearest linear foot, measured along the top of slab at centerline median from end of bridge approach slab to end of bridge approach slab.
(H10.7.1) Use for all barriers (see Barrier Wall Delineation).
- Concrete traffic barrier delineators shall be placed on top of the barrier as shown on Missouri Standard Plans 617.10 and in accordance with Sec 617. Delineators on bridges with two-lane, two-way traffic shall have retroreflective sheeting on both sides. Concrete traffic barrier delineators will be considered completely covered by the contract unit price for Type A B C D H Barrier.
Below is additional guidance for using Note H10.7.1: |
Bridges with two-lane, two-way traffic shall have retroreflective sheeting on both sides of the delineators. For two-lane, one-way traffic, retroreflective sheeting may be on one side only unless crossroad or entranceway traffic is just beyond exit to bridge and wrong way driving is to be discouraged with retroreflective sheeting on both sides of the delineators, (white and red in this case). "Delineators on bridges with two-lane, two-way traffic shall have retroreflective sheeting on both sides" may be modified, as required. For Type A and C barriers, retroreflective sheeting should be used on both sides of the delineators where there is not more than four lanes divided. |
On bridges with more than two lanes, retroreflective sheeting is not required on both sides of the delineators. The perception of a narrowing roadway at the bridge is of lesser consequence in terms of requiring guidance devices and does not warrant retroreflective sheeting on both sides of the delineators. "Delineators on bridges with two-lane, two-way traffic shall have retroreflective sheeting on both sides" may be removed at the discretion of the design team. |
(H10.7.2)
- Joint sealant and backer rods shall be in accordance with Sec 717 for silicone joint sealant for saw cut and formed joints.
(H10.7.3) Use note if slip forming is allowed.
- For slip-formed option, both sides of barrier shall have a vertically broomed finish and the top shall have a transversely broomed finish.
(H10.7.4) Use for all grade separations except over railroads and county roads.
- Plastic waterstop shall not be used with saw cut joints.
The following three notes shall be placed under section thru barrier.
(H10.8)
- Use a minimum lap of 2'-6" for #5 horizontal barrier bars.
(H10.9) Areas shown are for standard barrier heights and a two percent cross slope.
- The cross-sectional area above the slab is * square feet.
* 2.98 for a Type A barrier. 2.27 for a Type B barrier. 4.69 for a Type C barrier. 3.52 for a Type D barrier. 3.59 for a Type D barrier used as a median. 2.89 for a Type H barrier
(H10.9.1) Add (2) to the dimension for the top of slab to top of the R2 bar.
- (2) To top of bar
The following three notes shall be used for double-tee structures.
(H10.10)
- Coil inserts shall have a concrete ultimate pullout strength of not less than 36,000 pounds in 5000 psi concrete and an ultimate tensile strength of not less than 36,000 pounds.
(H10.11)
- Threaded coil rods shall have an ultimate capacity of 36,000 pounds. All coil inserts and threaded coil rods shall be galvanized in accordance with AASHTO M 232 (ASTM A153), Class C.
(H10.12)
- Payment for furnishing and installing coil inserts and threaded coil rods will be considered completely covered by the contract unit price for Type A B C D H Barrier.
The following two notes, when appropriate, shall be placed under the title of the elevation of barrier.
(H10.12.1) Dimensions shall be horizontal unless otherwise specified on Bridge Memorandum.
- Longitudinal dimensions are horizontal arc dimensions.
(H10.12.2)
- Longitudinal dimensions are along top of barrier outside edge of slab parallel to grade.
The following two notes shall be placed under the permissible alternate bar shape detail.
(H10.13) Use R2 for Type D or H barriers, R3 for Type B barrier and M2 for two separate Type D barriers used as a median. Add (4) to the combined #5 bar leader note. Exclude note and associated detail for CIP slabs.
- (4) The R2 R3 M2 bar and #5 bottom transverse slab bar in cantilever (prestressed panels only) combination may be furnished as one bar as shown, at the contractor's option.
(H10.14) Use R1 for Type B, D or H barriers. Use M1 for two separate Type D barriers used as a median. Add (3) to the two separated #5 bar leader notes.
- (3) The R1 M1 bar may be separated into two bars as shown, at the contractor's option, only when slip forming is not used. (All dimensions are out to out.)
(H10.15) Use note if slip forming is allowed. Place under the part elevation of barrier and add (1) to fiberglass bar leader notes in the section thru saw cut joint and part elevation of barrier.
- (1) Four feet long, centered on joint, slip-formed option only
Place general notes H10.19, H10.20 and H10.7.1 on the barrier at end bents sheet with notes H10.19 and H10.20 under the Reinforcing Steel heading.
(H10.19)
- Minimum clearance to reinforcing steel shall be 1 1/2" except as shown for bars embedded into end bent.
(H10.20) Use for Type B barrier only. Use 2’-4” and K10 bars for barrier ending on wing walls adding K13 bars with two different wing lengths. Will need to add more bars if more than two different wing lengths exist. Use 2’-6” and R6 bars for barrier ending on bridge deck.
- Use a minimum lap of 2'-4" 2’-6” between K9 and K10 or K13 R6 bars.
(H10.21) Place note under the K Bar Permissible Alternate Shape detail on the barrier at end bents sheet. Use K1 and K2 for Type B barrier; K9 and K10 for Type D barrier; K3 and K5 for Type H barrier.
- The K1 and K2 K9 and K10 K3 and K5 bar combination may be furnished as one bar as shown, at the contractor's option.
K1. General
(K1.1) Use for Bridge Approach Slab (Major Road) and omit underlined part for concrete sub-class Bridge Approach Slab (Minor Road).
- All concrete for the bridge approach slab and sleeper slab shall be in accordance with Sec 503 (f'c = 4,000 psi).
(K1.2)
- All joint filler shall be in accordance with Sec 1057 for preformed fiber expansion joint filler, except as noted.
(K1.3) Use for Bridge Approach Slab (Major Road) and omit underlined part for concrete sub-class Bridge Approach Slab (Minor Road).
- The reinforcing steel in the bridge approach slab and the sleeper slab shall be epoxy coated Grade 60 with Fy = 60,000 psi.
(K1.4)
- Minimum clearance to reinforcing steel shall be 1 1/2", unless otherwise shown.
(K1.5.1) Use for Bridge Approach Slab (Major Road).
- The reinforcing steel in the bridge approach slab and the sleeper slab shall be continuous. The transverse reinforcing steel may be made continuous by providing a minimum lap splice of 24 inches for #5 bars and 40 inches for #6 bars, or by mechanical bar splice.
(K1.5.2) Use for Bridge Approach Slab (Minor Road).
- The reinforcing steel in the bridge approach slab shall be continuous. The transverse reinforcing steel may be made continuous by providing a minimum lap splice of 26 inches for #4 bars, or by mechanical bar splice.
(K1.6) Use underline portion when mechanical bar splices are required due to staged construction.
- Mechanical bar splices shall be in accordance with Sec 710. (Estimated ____ splices per slab)
(K1.7)
- Seal joint between vertical face of approach slab and wing with sealant in accordance with Sec 717 for silicone joint sealant for saw cut and formed joints.
(K1.11)
- The contractor shall pour and satisfactorily finish the bridge semi-deep slab before placing the bridge approach slab.
(K1.12)
- Longitudinal construction joints in approach slab and sleeper slab shall be aligned with longitudinal construction joints in bridge semi-deep slab.
(K1.13) Use for Bridge Approach Slab (Major Road)
- Payment for furnishing all materials, labor and excavation necessary to construct the approach slab, including the timber header, sleeper slab, underdrain, Type 5 aggregate base, joint filler and all other appurtenances and incidental work as shown on this sheet, complete in place, will be considered completely covered by the contract unit price for Bridge Approach Slab (Major Road) per square yard.
(K1.14a) Use for Bridge Approach Slab (Minor) – Concrete Slab Only
- Payment for furnishing all materials, labor and excavation necessary to construct the concrete bridge approach slab, including the timber header, underdrain, Type 5 aggregate base, joint filler and all other appurtenances and incidental work as shown on this sheet, complete in place, will be considered completely covered by the contract unit price for Bridge Approach Slab (Minor) per square yard.
(K1.14b) Use for Bridge Approach Slab (Minor) – Asphalt Slab Only
- Payment for furnishing all materials, labor and excavation necessary to construct the asphalt bridge approach slab, including tack, curb and Type 5 aggregate base within the pay limits shown, complete in place, will be considered completely covered by the contract unit price for Bridge Approach Slab (Minor) per square yard.
(K1.15) Use for Bridge Approach Slab (Major Road) and Bridge Approach Slab (Minor Road) – Concrete Slab Only
- For concrete approach pavement details, see roadway plans.
(K1.16) Use for Bridge Approach Slab (Major Road)
- See Missouri Standard Plan 609.00 for details of Type A curb.
(K1.17) Use for Bridge Approach Slab (Minor Road) – Asphalt Slab Only
- See Missouri Standard Plan 609.00 for details of Type S curb.
(K1.18)
- With the approval of the engineer, the contractor may crown the bottom of the approach slab to match the crown of the roadway surface.
(K1.19) [MS Cell] Use boxed note for Bridge Approach Slab (Minor Road)
MoDOT Construction personnel will indicate the bridge approach slab used for this structure: | |
□ Concrete Bridge Approach Slab | |
□ Asphalt Bridge Approach Slab |
(K1.20)
- Drain pipe may be either 6" diameter corrugated metallic-coated pipe underdrain, 4" diameter corrugated polyvinyl chloride (PVC) drain pipe, or 4" diameter corrugated polyethylene (PE) drain pipe.
REVISION REQUEST 4030
620.5.4 Delineator Placement and Spacing (MUTCD Section 3F.04)
Guidance. Delineators should be mounted on suitable supports at a mount height, measured vertically from the bottom of the lowest retroreflective device to the elevation of the near edge of the roadway, of approximately 4 ft., see Standard Plans 903.00.
Option. When mounted on the face of or on top of guardrails or other longitudinal barriers, delineators may be mounted at a lower elevation than the normal delineator height recommended in the preceding paragraph.
Delineators should be placed 2 to 8 ft. outside the outer edge of the shoulder, or if appropriate, in line with the roadside barrier that is 8 ft. or less outside the outer edge of the shoulder.
Delineators should be placed at a constant distance from the edge of the roadway, except that where an obstruction intrudes into the space between the pavement edge and the extension of the line of the delineators. The delineators should be transitioned to be in line with or inside the innermost edge of the obstruction. If the obstruction is a guardrail or other longitudinal barrier, the delineators should be transitioned to be just behind, directly above (in line with), or on the innermost edge of the guardrail or longitudinal barrier. Channel post mounted delineators should not be installed behind guardrail if guardrail delineation is present.
Delineators should be spaced 200 ft. to 530 ft. apart on mainline tangent sections. Delineators should be spaced 100 ft. apart on ramp tangent sections.
Support. Examples of delineator installations are shown in Fig. 620.5.4.1, Examples of Delineator Placement.
Option. When uniform spacing is interrupted by such features as driveways and intersections, delineators which would ordinarily be located within the features may be relocated in either direction for a distance not exceeding one quarter of the uniform spacing. Delineators still falling within such features may be eliminated.
Delineators may be transitioned in advance of a lane transition or obstruction as a guide for oncoming traffic.
Guidance. The spacing of delineators should be adjusted on approaches to and throughout horizontal curves so that several delineators are always simultaneously visible to the road user. The approximate spacing is shown in the Approximate Spacing for Delineators on Horizontal Curves Table.
Radius of Curve, R ft. | Approximate Spacing on Curve, S ft. |
---|---|
50 | 20 |
115 | 25 |
180 | 35 |
250 | 40 |
300 | 50 |
400 | 55 |
500 | 65 |
600 | 70 |
700 | 75 |
800 | 80 |
900 | 85 |
1,000 | 90 |
Distances were rounded to the nearest 5 ft. |
Spacing for specific radii may be interpolated from table. The minimum spacing should be 20 feet. The spacing on curves should not exceed 300 feet. In advance of or beyond a curve, and proceeding away from the end of the curve, the spacing of the first delineator is 2S, the second 3S, and the third 6S but not to exceed 300 feet. S refers to the delineator spacing for specific radii computed from the formula (Formula applies to measurements in feet only). |
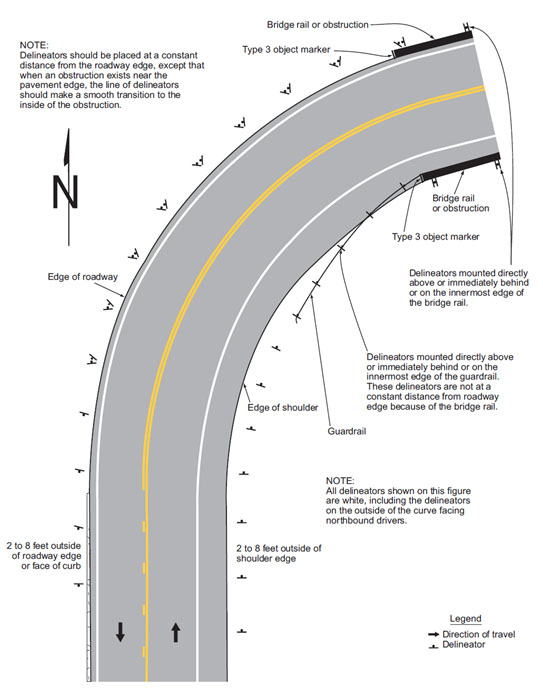
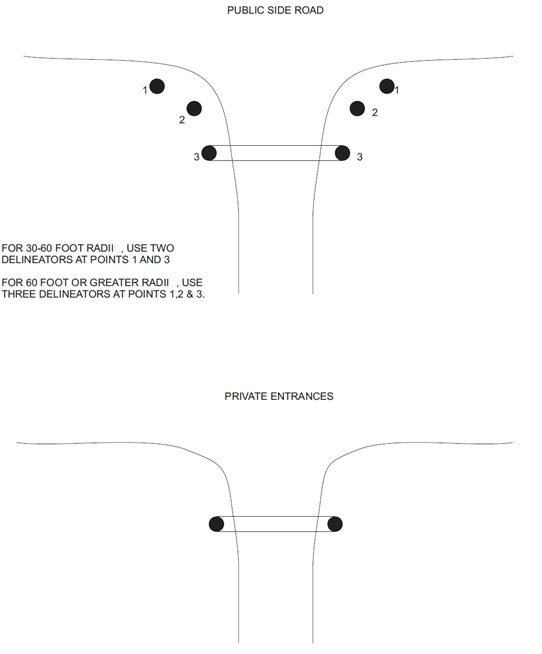
620.5.5 Guardrail Delineation
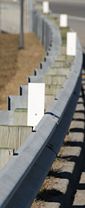
Standard. All guardrail shall be delineated in accordance with Section 606.10.2.3 of the Standard Specifications. The design of the guardrail delineators shall be in accordance with Standard Plans 903.00 and Standard Specification Sec 1065. The color of the retroreflective sheeting used shall match the color of the adjacent edgeline. If no edgeline is present, white shall be used on the right side facing approaching traffic.
On two-lane roads with two-way traffic the guardrail shall be delineated with white retroreflecitve sheeting on both sides of the delineator, including at bridge approaches.
Standard. If guardrail is present at off ramps, the back side of the guardrail delineator shall be red retroreflective sheeting. The red sheeting is used on the back side of guardrail delineators from the crossroad to the start of the deceleration lane on the main line.
Option. The use of the red sheeting on the back side of guardrail delineators may be used wherever there is a need to discourage wrong way driving.
620.5.6 Barrier Wall Delineation
Standard. Permanent barrier walls and bridge barrier walls shall be delineated in accordance with Section 617.30 of the Standard Specifications. The design of barrier wall delineators shall be in accordance with Standard Plan 903.00 and Standard Specification Sec 1065. The color of the barrier delineators shall match the color of the adjacent edgeline.
Guidance. Where there is traffic on both sides of a barrier wall, a two sided delineator with retroreflective sheeting on both sides, should be used. On two-lane roads the bridge barrier walls should be delineated with white retroreflective sheeting on both sides of the delineator.
Standard. If a barrier wall is present at off ramps, the back side of the barrier wall delineator shall be red retroreflective sheeting. The red sheeting is used on the back side of barrier wall delineators from the crossroad to the start of the deceleration lane on the main line.
Option. The use of the red sheeting on the back side of barrier wall delineators may be used wherever there is a need to discourage wrong way driving.
903.2.25.4 Quantity Computations
Standard. Signs and posts will each be paid for individually. This includes emergency reference markers and object markers. Combined unit prices for sign and support combinations have been discontinued. All signs including stop signs, object markers, emergency reference markers and signal signs shall be totaled on Form D-30 in four categories: Flat Sheet (FS), Flat Sheet Fluorescent (FSF), Structural (ST) and Structural Fluorescent. Structural signs’ width and height are designed to the nearest foot. Each standard, non-standard or special sign shall be calculated to the nearest 0.1 sq. ft., subtotaled to the nearest 0.1 sq. ft., and final pay total should be to the nearest 1.0 sq. ft.
All post quantities shall be calculated and totaled on Form D-29. All post lengths shall be calculated in increments of 0.25 ft. including the length that extends into the concrete footing or ground as shown on the standard plans. All U-channel post lengths shall include the full length of both pieces when overlaps are required. The post length for wide flange and pipe posts shall be multiplied by the pounds per foot (lb/ft) factor, as shown in the standard plans; each sign's posts are subtotaled to the nearest pound; all sign posts are subtotaled; and the final pay totals are shown to the nearest 10 pounds. All U-channel, wood and perforated square steel tube post length quantities shall be totaled and rounded to the nearest foot. For perforated square steel tube posts, an additional pay item shall be included for the anchor sleeve which is paid for by the linear foot for each post used (and may also include a soil plate). See the Post and Anchor Data Table in Standard Plan 903.03 to select the necessary anchor size. Omni-Directional anchors may be used for installation in weak or loose soil conditions.
Concrete for sign support structures shall be totaled on Form D-29. Concrete for overhead structure foundations shall be bolted down. Concrete for all post-mounted sign foundations shall be embedded. Bolted down and embedded quantities shall be calculated for each sign to the nearest 0.01 cubic yard, subtotaled to the nearest 0.01 cubic yard and a final pay total is shown to the nearest 0.1 cubic yard.
Cantilever and butterfly tubular support trusses shall have standard pay items. Span tubular trusses shall require special pay items. Information in the description shall include span length, truss number and span design type. Structure pay items shall include costs for all labor and materials associated with the structure, from the bottom of the base plate up, on up, as a lump sum item. Each span structure shall have a separate pay item. Structure data shall be provided on Form D-34.
All box trusses shall require a special pay item for each truss. All pay item descriptions shall include span length and truss number. Truss pay items shall include costs for all labor and materials associated with the truss, from the bottom of the base plate up, as a lump sum item. Each box truss, regardless of type, shall have a separate pay item.
See Standard Plan 903.00 for payment of delineators. Delineators shall be paid for per each on Form D-29, and include installation, bolts, post and sign.
Perforated Square Steel Tube Post Breakaway assemblies shall be totaled on Form D-29. Breakaway assemblies are incidental for pipe and structural steel posts.
Backing bar lengths and weights shall be shown on Form D-29, and are totaled with the pay item for structural steel posts. No weight deductions shall be made for punched or drilled holes. If no structural steel posts are used on a project, backing bar weights shall be added to pipe post weights.
Signal Sign Mounting Hardware shall be paid for per each on Form D-37A separate from signal signs, which will be paid for by square feet. Signal Sign Hardware will include all mounting hardware necessary to install one sign on the mast arm.
Special pay items shall not be included for items considered to be small amounts of work such as: strapping signs to lighting or signal posts or truss columns; covering inappropriate legends; "EXIT ONLY" panels on new signs; any symbol, arrow, shield or legend on new guide signs; hinge plates; aluminum wide flange posts for connecting service signs and exit number panels to structural guide signs; etc. No additional payment shall be made for hardware. Other than the above, it shall be left to the designer to decide which items require direct pay.
Option. Special pay items for signing may be required. Some examples of special work include: modifying legends, relocating existing signs to new posts, temporary ground mounting guide signs, bridge mounted support brackets, truss painting, pedestal repair, etc. It is left to the designer to decide which items require special pay items.
Support. Most jobs include the removal of existing signs and/or trusses. All removals are listed with other roadway Removal of Improvements. It is preferred to list the type of truss to be removed, number of pedestals, posts, footings and a rough estimate of sign area. Consult the District Traffic Engineer or District Constructions and Materials Engineer about which removals to salvage and where the contractor should deliver the salvaged materials. Items to be salvaged and delivery of these items are mentioned in the job special provisions and this work is paid for under Removal of Improvements.
903.17.1 Delineators
Support. Refer to Standard Plan 903.00 for delineator placement and use. Refer to EPG 620.5 for more information on delineators.
Delineators are placed on all divided highways, expressways, non-interstate freeways and interchanges. It is not necessary to spot each delineator on the sign location plan, unless the geometrics are unusual, and placement is not readily apparent when referencing the standard plans. Totals are estimated and shown on Form D-29.
903.17.5 Object Markers for Ends of Roadways (MUTCD Section 2C.66)

Support. The Type 4 object marker is used to warn and alert road users of the end of a roadway in other than construction or maintenance areas.
Standard. If object markers are used to mark the end of a roadway, four Type 4 object marker shall be used. See Standard Plan 903.00 for installation details.
Option. The Type 4 object marker may be used in instances where there are no alternate vehicular paths.
Standard. The minimum mounting height, measured vertically from the bottom of a Type 4 object marker to the elevation of the near edge of the traveled way, shall be 4 feet.
Guidance. Appropriate advance warning signs should be used.
1044.2.1 Mile and Object Marker, and Delineator Posts
The required shape, length, weight (mass) and hole punching diagram for mile marker and delineator posts may be found on Standard Plan 903.00. The inspector should be aware that minimum and maximum weights (masses) and shape dimensions found on the Standard Plan are absolute and no additional tolerance is allowed. The specified weight (mass) of these posts is before galvanizing and before fabrication. Therefore, if the posts are weighed after fabrication and galvanizing and the weight (mass) per linear ft. (meter) is found to be at the specified limit or slightly out, the weight (mass) of the steel in the post will have to be calculated by adding the theoretical weight (mass) of the steel punched out to form the holes and deducting the theoretical weight of the galvanized coating. An example calculation is available.
Field determination of weight (mass) of coating is to be made. The magnetic gauge is to be operated and calibrated in accordance with ASTM E376. A single-spot test is to be comprised of five readings of the magnetic gauge taken in a small area and averaged to obtain a single test result. Three such areas should be tested, one area near each end and one near the center. This would yield three single-spot test results for that specimen. Average the three test results to obtain the average coating weight (mass) for that specimen. Average all test results from all specimens to obtain the average coating weight (mass) to be reported. The minimum result would be the lowest average coating weight (mass) found on any one specimen. Material may be accepted or rejected for galvanized coating on the basis of magnetic gauge results. If a test result fails to comply with the specifications, that lot should be re-sampled at double the original rate. If any of the re-samples fail to comply with the specifications, that lot is to be rejected. The contractor or supplier is to be given the option of sampling for Laboratory testing if the magnetic gauge test results are within minus 15 percent of the specified coating weight (mass).
1044.5.1.2 Physical Tests
Dimensions, shape, mass, length, and hole punching shall be measured for conformance to Standard Plan 903.00. To determine the mass per linear foot (linear meter) of a galvanized steel post after fabrication, refer to 1044.3 Calculations. Test results shall be recorded through AWP.
REVISION REQUEST 4033
751.5.9.2.5 Spacing Limits
Reinforcement spacing shall be in accordance with LRFD 5.10.3, unless modified by the following criteria or elsewhere shown in the EPG.
Minimum Spacing - Moment Reinforcement | |
---|---|
Preferred Min. - Footings | 6" centers |
Preferred Min. - Slabs, Culvert Walls and Retaining Walls | 6" centers |
Absolute Min. - Slabs, Culvert Walls and Retaining Walls | 5” centers |
Preferred Min. - All Other | 4” centers |
Absolute Min. | 2 1/2” clear |
Maximum Spacing - Moment Reinforcement | |
Absolute Max. - Slabs | 1.5(slab thickness) |
Absolute Max. - All Other | 18" |
Minimum Spacing - Shear Reinforcement | |
Absolute Min. - Substructure Beams (single stirrups) | 5" centers |
Absolute Min. - Substructure Beams (double Stirrups) | 6" centers |
Absolute Min. - Prestressed Slab Beams, Box Beams and I Girders | 5" centers |
Maximum Spacing - Shear Reinforcement | |
Absolute Max. - Substructure Beams | 12" centers |
Absolute Max. - Prestressed Slab Beams, Box Beams and I Girders | Refer to EPG 751.22 P/S Concrete I Girders |
Minimum Spacing - Longitudinal Compression Reinforcement (Include 1/2-inch buffer for mechanical bar splices) | |
Absolute Min. | 4 1/2" centers (5" centers) |
Absolute Min. - Cols. (thru #10) | 2" clear (2 1/2" clear) |
Absolute Min. - Cols. (#11, #14) | 2 1/2" clear (3" clear) |
Absolute Min. - Cols (#18) | 3 1/2” clear (4" clear) |
For Drilled Shafts and Rock Sockets, see EPG 751.37.6.1 Reinforcement Design. | |
Minimum Pitch - Spiral Reinforcement for Compression Members (Static) | |
For Columns, Drilled Shafts, Rock Sockets | See EPG 751.31.3.2 Column |
Minimum Spacing- Ties (Transverse) Reinforcement for Compression Members (Static) | |
For Columns | See EPG 751.31.3.2 Column |
For Drilled Shafts and Rock Sockets, see EPG 751.37.6.1 Reinforcement Design. | 6” centers for #4 bars |
Maximum Spacing - Longitudinal Compression Reinforcement | |
Absolute Max. - the minimum number of longitudinal reinforcing bars shall be six for circular members and four for bars in a rectangular arrangement. For other requirements, see LRFD | |
Maximum Pitch - Spiral Reinforcement for Compression Members (Static) | |
Absolute Max. - Spirals | 6” pitch |
Maximum Spacing - Ties (Transverse) Reinforcement for Compression Members (Static) | |
Absolute Max. - Ties | 12" centers |
Minimum & Maximum Pitch- Spiral Reinforcement for Compression Members (Seismic) | |
See EPG 751.9.1.2 LRFD Seismic Details |
751.5.9.2.6 Cover Limits
Situation | Minimum Cover | |
---|---|---|
Concrete cast against and permanently exposed to earth: | ||
- primary reinforcement | 3" | |
- stirrups, ties, spirals | 2 1/2" | |
Conc. exposed to earth or weather: | ||
- primary reinforcement | 2" | |
- stirrups, ties, spirals | 1 1/2" | |
Conc. slabs which have no positive corrosion protection: | ||
- top reinforcement | 3" * | |
- bottom reinforcement | 1" | |
Conc. not exposed to weather or in contact with ground: | ||
- primary reinforcement (thru #11) | 1 1/2" | |
- stirrups, ties, spirals | 1" | |
Conc. piles cast against or permanently exposed to earth | 2" | |
* Absolute minimum cover shall be 2½ inches by LRFD 5.12.3. The minimum cover for stirrup and tie steel shall be 1½ inches unless otherwise specified. For minimum cover for drilled shafts and rock sockets, see EPG 751.37.6.1 Reinforcement Design. |
751.9.1.2 LRFD Seismic Details
751.9.1.2.1 Seismic Details for Column Supported on Footing
Seismic Design Category, SDC B | |||||||||||
---|---|---|---|---|---|---|---|---|---|---|---|
Shear Reinf. |
Diameter (inch) |
Min. cover (inch) |
Core D' (inch) |
spiral/hoop size1 | Area of spiral/hoop bar Asp (sq. inch) |
Pitch or space s (inch) |
f'c (ksi) |
Ro = 4Asp/(D'*s) SGS Eq 8.6.2‐7 |
Ro min SGS 8.6.5 |
||
Spiral | 36 | 1.5 | 32.375 | 5 | 0.307 | 4 | 3 | 0.0095 | ≥ | 0.003 | OK |
Spiral | 42 | 1.5 | 38.375 | 5 | 0.307 | 4 | 3 | 0.0080 | ≥ | 0.003 | OK |
Spiral | 48 | 1.5 | 44.375 | 5 | 0.307 | 4 | 3 | 0.0069 | ≥ | 0.003 | OK |
Spiral | 54 | 1.5 | 50.375 | 5 | 0.307 | 4 | 3 | 0.0061 | ≥ | 0.003 | OK |
Hoop | 60 | 1.5 | 56.375 | 5 | 0.307 | 4 | 3 | 0.0054 | ≥ | 0.003 | OK |
Hoop | 66 | 1.5 | 62.375 | 5 | 0.307 | 4 | 3 | 0.0049 | ≥ | 0.003 | OK |
Hoop | 72 | 1.5 | 68.375 | 5 | 0.307 | 4 | 3 | 0.0045 | ≥ | 0.003 | OK |
Seismic Design Category, SDC C and D | |||||||||||
---|---|---|---|---|---|---|---|---|---|---|---|
Shear Reinf. |
Diameter (inch) |
Min. cover (inch) |
Core D' (inch) |
spiral/hoop size1 | Area of spiral/hoop bar Asp (sq. inch) |
Pitch or space s (inch) |
f'c (ksi) |
Ro = 4Asp/(D'*s) SGS Eq 8.6.2‐7 |
Ro min SGS 8.6.5 |
||
Spiral | 36 | 1.5 | 32.375 | 5 | 0.307 | 4 | 3 | 0.0095 | ≥ | 0.005 | OK |
Spiral | 42 | 1.5 | 38.375 | 5 | 0.307 | 4 | 3 | 0.0080 | ≥ | 0.005 | OK |
Spiral | 48 | 1.5 | 44.375 | 5 | 0.307 | 4 | 3 | 0.0069 | ≥ | 0.005 | OK |
Spiral | 54 | 1.5 | 50.375 | 5 | 0.307 | 4 | 3 | 0.0061 | ≥ | 0.005 | OK |
Hoop | 60 | 1.5 | 56.375 | 5 | 0.307 | 4 | 3 | 0.0054 | ≥ | 0.005 | OK |
Hoop | 66 | 1.5 | 62.25 | 6 | 0.442 | 4 | 3 | 0.0071 | ≥ | 0.005 | OK |
Hoop | 72 | 1.5 | 68.25 | 6 | 0.442 | 4 | 3 | 0.0065 | ≥ | 0.005 | OK |
Note: | 1For simplification use minimum #5 spiral/hoop bar. | SGS 8.8.9 |
Ro shall be ≥ 0.003 in SDC B and 0.005 in SDC C and D. No need to meet LRFD 5.6.4.6‐1 & 5.11.4.1.4‐1 minimum Ro requirements. | SGS 8.6.5 | |
Use 4" spiral pitch/hoop spacing for column to meet long. bar splice area requirements. | LRFD 5.11.4.1.6 | |
Use spiral or hoop but combination of spiral reinforcement with hoops shall not be used except in the footing or bent cap. | SGS 8.8.7 | |
Closed tie (Hoop) shall use 135‐degree hook with an extension of 6 bar diameters but not less than 3". | SGS 8.8.9 | |
Welding of reinforcing steel (spiral, hoop and longitudinal) is not permitted due to the prohibitive cost of weld inspection. | ||
Spiral does not need to meet end tail requirements of SGS 8.8.7. | ||
(1) Anchorage of spiral reinforcement shall be provided by 1 1/2 extra turns of spiral reinforcement at end of the spiral unit. | ||
(2) Lac = max(Lac from SGS 8.8.4, 1.25 Ld) or Ldh, but shall be extended to the clear cover specified herein. | ||
(3) 11 inches for #8 thru #11 bars and 14 inches for #14 bars. | ||
(4) Plastic hinge area for SDC B: Lpr ≥ max(1.0 * col dia, 1/6 clear col ht., 18") | SGS C8.8.9 & LRFD C5.11.4.1.4 | |
(4) Plastic hinge area for SDC C and D: Lpr ≥ max(1.5 * col dia, Lp, 1/6 clear column ht.) | SGS 4.11.6 and 4.11.7 | |
(4) Long reinf. and spiral bar shall not be spliced in plastic hinge area. If splice is unavoidable, a mechanical bar splice shall be used. | SGS 8.8.3 LRFD 5.11.4.1.6 | |
(5) Minimum lap: Use greater of EPG 751.5.9.2.8.2 Class B lap splice or 60 bar diameters. Lap splices and mechanical bar splices are to be alternately staggered at least 24”at two different locations. | LRFD 5.10.8.4.3b | |
For dowel bar in beam cap, See EPG 751 .22.2.7 Dowel Bars | ||
For additional requirements of column joints in SDC C and D, See EPG 751 .9.1.2.4 T-Joint (Column Joint) Connections for Seismic Design Category C and D. | ||
Use Figure 751.9.1.2.1.1 and Figure 751.9.1.2.1.2 for seismic detail option. For complete seismic design option spiral/hoop bar size shall be increased up to #6 and pitch/spacing shall be reduced as needed by design. Absolute minimum clearance is 1.5 inches. |
-
Figure 751.9.1.2.1.1 Seismic Details for Column Supported on Footing
-
Figure 751.9.1.2.1.2 Seismic Bar Details
751.9.1.2.2 Seismic Details for Non-oversized Drilled Shaft
Seismic Design Category, SDC B | ||||||||||||
---|---|---|---|---|---|---|---|---|---|---|---|---|
Shear Reinf. |
Diameter (inch) |
Min. cover (inch) |
Core D' (inch) |
spiral/hoop size1 | 1 for single bar 2 for bundle hoop bars |
Area of spiral/hoop bar Asp (sq. inch) |
Pitch or space s (inch) |
f'c (ksi) |
Ro = 4Asp/(D'*s) SGS Eq 8.6.2‐7 |
Ro min SGS 8.6.5 |
||
Spiral | 36 | 6 | 23.375 | 5 | 1 | 0.307 | 6 | 4 | 0.0087 | ≥ | 0.003 | OK |
Spiral | 42 | 6 | 29.375 | 5 | 1 | 0.307 | 6 | 4 | 0.0070 | ≥ | 0.003 | OK |
Spiral | 48 | 6 | 35.375 | 5 | 1 | 0.307 | 6 | 4 | 0.0058 | ≥ | 0.003 | OK |
Spiral | 54 | 6 | 41.375 | 5 | 1 | 0.307 | 6 | 4 | 0.0049 | ≥ | 0.003 | OK |
Spiral | 60 | 6 | 47.375 | 5 | 1 | 0.307 | 6 | 4 | 0.0043 | ≥ | 0.003 | OK |
Hoop | 66 | 6 | 53.375 | 5 | 1 | 0.307 | 6 | 4 | 0.0038 | ≥ | 0.003 | OK |
Hoop | 72 | 6 | 59.375 | 5 | 1 | 0.307 | 6 | 4 | 0.0034 | ≥ | 0.003 | OK |
Hoop | 78 | 6 | 65.25 | 6 | 1 | 0.442 | 6 | 4 | 0.0045 | ≥ | 0.003 | OK |
Seismic Design Category, SDC C and D | ||||||||||||
---|---|---|---|---|---|---|---|---|---|---|---|---|
Shear Reinf. |
Diameter (inch) |
Min. cover (inch) |
Core D' (inch) |
spiral/hoop size1 | 1 for single bar 2 for bundle hoop bars |
Area of spiral/hoop bar Asp (sq. inch) |
Pitch or space s (inch) |
f'c (ksi) |
Ro = 4Asp/(D'*s) SGS Eq 8.6.2‐7 |
Ro min SGS 8.6.5 |
||
Spiral | 36 | 6 | 23.375 | 5 | 1 | 0.307 | 6 | 4 | 0.0087 | ≥ | 0.005 | OK |
Spiral | 42 | 6 | 29.375 | 5 | 1 | 0.307 | 6 | 4 | 0.0070 | ≥ | 0.005 | OK |
Spiral | 48 | 6 | 35.375 | 5 | 1 | 0.307 | 6 | 4 | 0.0058 | ≥ | 0.005 | OK |
Spiral | 54 | 6 | 41.25 | 6 | 1 | 0.442 | 6 | 4 | 0.0071 | ≥ | 0.005 | OK |
Spiral | 60 | 6 | 47.25 | 6 | 1 | 0.442 | 6 | 4 | 0.0062 | ≥ | 0.005 | OK |
Hoop | 66 | 6 | 53.25 | 6 | 1 | 0.442 | 6 | 4 | 0.0055 | ≥ | 0.005 | OK |
Hoop | 72 | 6 | 59.375 | 5 | 2 | 0.614 | 8 | 4 | 0.0052 | ≥ | 0.005 | OK |
Hoop | 78 | 6 | 65.25 | 6 | 2 | 0.884 | 8 | 4 | 0.0068 | ≥ | 0.005 | OK |
Note: | 1For simplification use minimum #5 spiral/hoop bar. | SGS 8.8.9 |
Ro shall be ≥ 0.003 in SDC B and 0.005 in SDC C and D. No need to meet LRFD 5.6.4.6‐1 & 5.11.4.1.4‐1 minimum Ro requirements. | SGS 8.6.5 | |
Closed tie (Hoop) shall use 135‐degree hook with an extension of 6 bar diameters but not less than 3". | SGS 8.8.9 | |
Spiral does not need to meet end tail requirements of SGS 8.8.7. | ||
(6) Anchorage of spiral reinforcement shall be provided by 1 1/2 extra turns of spiral reinforcement at end of the spiral unit. | ||
(7) Plastic hinge area for SDC B: Lpr ≥ drilled shaft diameter. | SGS C8.8.9 and LRFD C5.11.4.1.4 | |
(7) Plastic hinge area for SDC C and D: Lpr ≥ max(1.5 * Column dia., Lp, drilled shaft diameter). | SGS 4.11.6 and 4.11.7 | |
(7,8) Long reinforcement and spiral bar shall not be spliced in plastic hinge area. If splice is unavoidable, a mechanical bar splice shall be used. | SGS 8.8.3 and LRFD 5.11.4.1.6 | |
(8) Plastic hinge area : Lpr ≥ drilled shaft diameter. | ||
(9) Minimum lap: Use greater of EPG 751.5.9.2.8.2 Class B lap splice or 60 bar diameters. Lap splices and mechanical bar splices are to be alternately staggered at least 24”at two different locations. | LRFD 5.10.8.4.3b | |
(10) Use spiral or hoop but combination of spiral reinforcement with hoops shall not be used except in the bent cap. From above table if hoop required for drilled shaft than hoop shall be used in the column and if spiral required for drilled shaft than spiral shall be used in column. Use spiral or hoop bar size and pitch or spacing per EPG 751.9.1.2.1 | SGS 8.8.7 | |
Welding of reinforcing steel (spiral, hoop and longitudinal) is not permitted due to the prohibitive cost of weld inspection. | ||
For detail simplification consider drilled shaft 6” larger than column. Avoid sizing shafts 12” larger than column. | ||
For column and beam detail requirements, see EPG 751.9.1.2.1. | ||
For oversized shaft (generally 18" minimum larger than column), see EPG 751.9.1.2.3 Seismic Details for Oversized Drilled Shaft. | ||
For additional requirements of column joints in SDC C and D, See EPG 751.9.1.2.4 T-Joint (Column Joint) Connections for Seismic Design Category C and D. | ||
Use Figure 751.9.1.2.2 for seismic detail option. For complete seismic design option spiral/hoop bar size shall be increased up to #6 and pitch/spacing shall be 6” by design. Absolute minimum clearance is 5 inches. If #6 at 6” spiral or hoop do not meet design requirements, then use 2-#6 hoop bars @ 8” spacing. | ||
For seismic bar details (spiral and hoop), see Figure 751.9.1.2.1.2 |
-
Figure 751.9.1.2.2 Seismic Details for Non-oversized Drilled Shaft
751.9.1.2.3 Seismic Details for Oversized Drilled Shaft
Seismic Design Category, SDC B | ||||||||||||
---|---|---|---|---|---|---|---|---|---|---|---|---|
Shear Reinf. |
Diameter (inch) |
Min. cover (inch) |
Core D' (inch) |
spiral/hoop size1 | 1 for single bar 2 for bundle hoop bars |
Area of spiral/hoop bar Asp (sq. inch) |
Pitch or space s (inch) |
f'c (ksi) |
Ro = 4Asp/(D'*s) SGS Eq 8.6.2‐7 |
Ro min SGS 8.6.5 |
||
Spiral | 36 | 6 | 23.375 | 5 | 1 | 0.307 | 6 | 4 | 0.0087 | ≥ | 0.003 | OK |
Spiral | 42 | 6 | 29.375 | 5 | 1 | 0.307 | 6 | 4 | 0.0070 | ≥ | 0.003 | OK |
Spiral | 48 | 6 | 35.375 | 5 | 1 | 0.307 | 6 | 4 | 0.0058 | ≥ | 0.003 | OK |
Spiral | 54 | 6 | 41.375 | 5 | 1 | 0.307 | 6 | 4 | 0.0049 | ≥ | 0.003 | OK |
Spiral | 60 | 6 | 47.375 | 5 | 1 | 0.307 | 6 | 4 | 0.0043 | ≥ | 0.003 | OK |
Spiral/Hoop | 66 | 6 | 53.375 | 5 | 1 | 0.307 | 6 | 4 | 0.0038 | ≥ | 0.003 | OK |
Spiral/Hoop | 72 | 6 | 59.375 | 5 | 1 | 0.307 | 6 | 4 | 0.0034 | ≥ | 0.003 | OK |
Spiral/Hoop | 78 | 6 | 65.25 | 6 | 1 | 0.442 | 6 | 4 | 0.0045 | ≥ | 0.003 | OK |
Seismic Design Category, SDC C and D | ||||||||||||
---|---|---|---|---|---|---|---|---|---|---|---|---|
Shear Reinf. |
Diameter (inch) |
Min. cover (inch) |
Core D' (inch) |
spiral/hoop size1 | 1 for single bar 2 for bundle hoop bars |
Area of spiral/hoop bar Asp (sq. inch) |
Pitch or space s (inch) |
f'c (ksi) |
Ro = 4Asp/(D'*s) SGS Eq 8.6.2‐7 |
Ro min SGS 8.6.5 |
||
Spiral | 36 | 6 | 23.375 | 5 | 1 | 0.307 | 6 | 4 | 0.0087 | ≥ | 0.005 | OK |
Spiral | 42 | 6 | 29.375 | 5 | 1 | 0.307 | 6 | 4 | 0.0070 | ≥ | 0.005 | OK |
Spiral | 48 | 6 | 35.375 | 5 | 1 | 0.307 | 6 | 4 | 0.0058 | ≥ | 0.005 | OK |
Spiral | 54 | 6 | 41.25 | 6 | 1 | 0.442 | 6 | 4 | 0.0071 | ≥ | 0.005 | OK |
Spiral | 60 | 6 | 47.25 | 6 | 1 | 0.442 | 6 | 4 | 0.0062 | ≥ | 0.005 | OK |
Spiral/Hoop | 66 | 6 | 53.25 | 6 | 1 | 0.442 | 6 | 4 | 0.0055 | ≥ | 0.005 | OK |
Hoop | 72 | 6 | 59.375 | 5 | 2 | 0.614 | 8 | 4 | 0.0052 | ≥ | 0.005 | OK |
Hoop | 78 | 6 | 65.25 | 6 | 2 | 0.884 | 8 | 4 | 0.0068 | ≥ | 0.005 | OK |
Note: | 1For simplification use minimum #5 spiral/hoop bar. | SGS 8.8.9 |
Ro shall be ≥ 0.003 in SDC B and 0.005 in SDC C and D. No need to meet LRFD 5.6.4.6‐1 & 5.11.4.1.4‐1 minimum Ro requirements. | SGS 8.6.5 | |
Closed tie (Hoop) shall use 135‐degree hook with an extension of 6 bar diameters but not less than 3". | SGS 8.8.9 | |
Spiral does not need to meet end tail requirements of SGS 8.8.7. | ||
(11) Anchorage of spiral reinforcement shall be provided by 1 1/2 extra turns of spiral reinforcement at end of the spiral unit. | ||
(12) Plastic hinge area for SDC B: Lpr ≥ drilled shaft diameter. | SGS C8.8.9 and LRFD C5.11.4.1.4 | |
(12) Plastic hinge area for SDC C and D: Lpr ≥ max(1.5 * Column dia., Lp, drilled shaft diameter). | SGS 4.11.6 and 4.11.7 | |
(12) Long reinforcement and spiral bar shall not be spliced in plastic hinge area. If splice is unavoidable, a mechanical bar splice shall be used. | SGS 8.8.3 and LRFD 5.11.4.1.6 | |
(13) Plastic hinge area : Lpr ≥ drilled shaft diameter. | ||
(14) Minimum lap: Use greater of EPG 751.5.9.2.8.2 Class B lap splice or 60 bar diameters. Lap splices and mechanical bar splices are to be alternately staggered at least 24”at two different locations. | LRFD 5.10.8.4.3b | |
(15) Since column reinforcement embedded into drilled shaft, clear spacing between column reinforcement shall be 5” min. | ||
(16) Spiral pitch or hoop bar spacing shall be same as drilled shaft requirements. | ||
Use spiral or hoop but combination of spiral reinforcement with hoops shall not be used in a reinforcement cage except in bent cap. Spirals in the column cage and hoops in the drilled shaft cage can be used for oversized drilled shaft | SGS 8.8.7 | |
Welding of reinforcing steel (spiral, hoop and longitudinal) is not permitted due to the prohibitive cost of weld inspection. | ||
Hoops are preferred for drilled shafts with diameters at least 2’-6” larger than column. Spirals shall be used in drilled shafts that are oversized by 18” or 24” due to potential interference between the hooks and the column reinforcing cage. | ||
Column confinement: | ||
For column use spiral/pitch or hoop/spacing and bar size per column shear reinforcement requirements. | ||
Drilled shaft confinement: | ||
Exterior cage: From above table use spiral/pitch or hoop/spacing for drilled shaft. | ||
Interior cage: Column confinement reinforcement bar size from column shear reinforcement table shall be spaced or pitched same as drilled shaft and provided over entire embedded length of column steel in drilled shaft. |
||
For column and beam detail requirements, see column shear reinforcement. | ||
For additional requirements of column joints in SDC C and D, See EPG 751.9.1.2.4 T-Joint (Column Joint) Connections for Seismic Design Category C and D. | ||
Use Figure 751.9.1.2.3 for seismic detail option. For complete seismic design option spiral/hoop bar size shall be increased up to #6 and pitch/spacing shall be 6” by design. Absolute minimum clearance is 5 inches. If #6 at 6” spiral or hoop do not meet design requirements, then use 2-#6 hoop bars @ 8” spacing. | ||
For seismic bar details (spiral and hoop), see Figure 751.9.1.2.1.2 |
-
Figure 751.9.1.2.3 Seismic Details for Oversized Drilled Shaft
751.9.1.2.4 T-Joint (Column Joint) Connections for Seismic Design category C and D
Minimum joint reinforcement shall be provided as shown below. Reinforcement marked as “additional” shall not be used to satisfy other load requirements.
751.9.1.2.4.1 Bent Cap Joint Shear Reinforcement
1. | Additional Vertical Stirrups Outside the Joint Region | SGS 8.13.5.1.1 |
Total area of column longitudinal reinforcement anchored in the joint = Total area of column longitudinal reinforcement anchored in the joint | ||
Minimum total area of additional vertical stirrups on each side of joint | ||
Total area of vertical stirrups shall be provided transversely within a distance equal to the column diameter extending from each face of the column as shown in Figure 751.9.1.2.4.1a. For additional vertical stirrups size and spacing limitations, see EPG 751.31.3.1. | ||
2. | Additional Vertical Stirrups Inside the Joint Region | SGS 8.13.5.1.2 |
Where, | ||
Total area of column longitudinal reinforcement anchored in the joint | ||
Minimum total area of vertical stirrups inside the joint region | ||
Total area of vertical stirrups spaced evenly over the column inside the joint region as shown in Figure 751.9.1.2.4.1a. For additional vertical stirrups size and spacing limitations, see EPG 751.31.3.1. | ||
3. | Additional Longitudinal Cap Beam Reinforcement | SGS 8.13.5.1.3 |
Where, | ||
Total area of column longitudinal reinforcement anchored in the joint | ||
Minimum total area of additional longitudinal reinforcement in top and bottom faces of the cap beam | ||
The additional longitudinal reinforcement shall be extended at least one column diameter plus development length from face of the column as shown in Figure 751.9.1.2.4.1a | ||
4. | Horizontal J-Bars | SGS 8.13.5.1.4 |
#4 Horizontal J-bars shall be hooked around the longitudinal reinforcement on each face of the cap beam at every other stirrup inside the joint as shown in Figure 751.9.1.2.4.1b. | ||
When complete seismic analysis is required per bridge seismic design flowchart, joint shear reinforcement shall be provided in accordance with AASHTO Guide Specifications for LRFD Seismic Bridge Design (SGS). Modify above information and provide additional reinforcement as needed by design. | SGS 8.12 and 8.13 |
-
Figure 751.9.1.2.4.1a Elevation Showing Column and Beam Cap Reinforcement
(SDC C and D only)
-
Figure 751.9.1.2.4.1b Section Showing Column and Beam Cap Reinforcement
(SDC C and D only)
751.9.1.2.4.2 Footing (Spread Footing and Pile Cap Footing) Joint Shear Reinforcement
For seismic detail option, use following information for spread footing and pile cap footing | SGS 6.4.7 | ||
Vertical shear reinforcement #5 at about 12” each way shall be placed around the column perimeter within a horizontal dimension from face of the column equal to minimum as shown in Figure 751.9.1.2.4.2a and Figure 751.9.1.2.4.2b. #6 maximum bar size shall be used for vertical shear reinforcement. | |||
Effective depth from top of footing to lower reinforcement mat. | |||
Additional longitudinal horizontal reinforcement at top of footing, : | |||
= | |||
Where, | |||
= Total area of column longitudinal reinforcement anchored in the joint | |||
= Expected yield stress of column longitudinal reinforcement | |||
= 68 ksi for ASTM A706 and ASTM A615 | SGS Table 8.4.2-1 | ||
= Minimum yield stress of column longitudinal reinforcement | |||
= 60 ksi for ASTM A706 and ASTM A615 | SGS Table 8.4.2-1 | ||
The additional longitudinal reinforcement shall be extended at least up to a distance plus development length from face of the column and must be placed so that the reinforcement goes through the column reinforcement as shown in Figure 751.9.1.2.4.2b shall be provided in both directions in the footing. | |||
When complete seismic analysis is required per bridge seismic design flowchart, joint shear reinforcement shall be provided in accordance with AASHTO Guide Specifications for LRFD Seismic Bridge Design (SGS). Modify above information and provide additional reinforcement as needed by design. | SGS 6.4.5, 6.4.6 and 6.4.7 |
-
Figure 751.9.1.2.4.2a Spread Footing Joint Shear Reinforcement
-
Figure 751.9.1.2.4.2b Pile Footing Joint Shear Reinforcement
751.9.3.1.7 T- Joint Connections for LFD
For LFD T-Joint connection requirement, see EPG 751.40.8.11.5 T- Joint Connections.
!!! MOVE TO NEW ARTICLE NUMBER DARREN CHECK THIS SECTION AND MAKE SURE I FOUND AND FIXED ALL THE FIGURE NUMBERS !!!
751.40.8.11.5 T- Joint Connections
Principal Tension and Compression Stresses in Beam-Column Joints
The connections where columns and beams join, or where columns and footings join, should be based on the capacity design for shear and diagonal tension. For most locations, this is a “T”-shaped joint. For the analysis of “knee joints”, see Priestley and Seible, 1996.

In the capacity design of connection joints, the column moment, M0, will be the moment that is known and which will correspond to flexural overstrength of the column plastic hinges, i.e. M0 = 1.3Mp of the column. If the columns are designed based on plastic hinging, the beam and footings shall be designed with capacities greater than or equal to 1.3Mp.
At each joint, the principal tension and compression stresses are defined and checked as follows:
- (1)
- (2)
- (3)
- (4)
- (5)
- (6)
- (7)
- (8)
- in which:
- Vjh = Average horizontal shear force within a joint.
- Vjv = Average vertical shear force within a joint.
- vjh = Average horizontal shear stress within a joint.
- vjv = Average vertical shear stress within a joint.
- hb = Beam depth.
- hc = Column diameter or rectangular column cross-section height.
- bje = The effective width of a joint, defined in Fig. 751.40.8.11.5.2.
- D = Round column diameter.
- fv = Average vertical axial stress due to column axial force Pc, including the seismic component.
- Pc = Column axial force.
- fh = Average horizontal axial stress at the center of the joint.
- pc = Nominal principal compression stress in a joint. (positive)
- pt = Nominal principal tensile stress in a joint. (negative)
- bb = Beam width
- bc = Column cross-section width
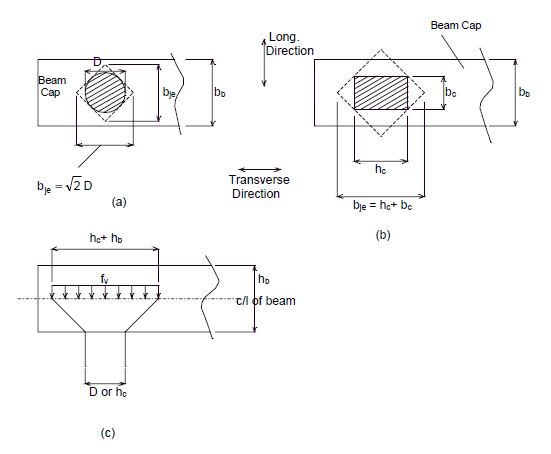
In Fig. 751.40.8.11.5.2(c), the effective width is taken at the center of the column section, allowing a 45° spread from boundaries of the column section into the beam cap. In the transverse direction, the effective width will be the smaller of the value given by eq. (3) and the beam cap width bb. Experimental evidence indicates that diagonal cracking is initiated in the joint region when psi. The principle compression stress pc shall be limited to .
Design of Reinforcement for Beam-Column Joints
When the principal tension stress, pt, exceeds psi, joint cracking occurs and the following reinforcement shall be provided:
a) Vertical beam stirrup reinforcement shall be placed throughout the distance of hb/2 from the column face on each side of the column. The required amount of vertical beam stirrup reinforcement, Ajv, is:
- (9)
- Where:
- Asc = The total area of longitudinal steel
- f°yc = overstrength stress in the column reinforcement use
- f°yc = 1.1f
- fyv = yield stress of vertical stirrup reinforcement.
b) Vertical beam stirrup reinforcement within the joint, Avi, is
- (10)
c) The additional beam bottom longitudinal reinforcement required is
- (11)
- where fyb = the yield stress of the beam bottom longitudinal reinforcement. This additional reinforcement must be carried a sufficient distance to develop its yield strength a distance hb/2 from the column face.
d) The horizontal hoop reinforcement within a joint requires
- (12)
which for F = 0 simplifies to
- (13)
- Where
- F = The beam cap prestress force.
- fyh = The yield stress of the horizontal hoops.
- La = The Anchorage length in the joint.
The minimum amount of horizontal hoop reinforcement shall be
- (14)
The spacing of the horizontal hoop can be based on:
(15)
- Where
- As = The cross-sectional area of the hoop bar.
- D’ = The hoop diameter.
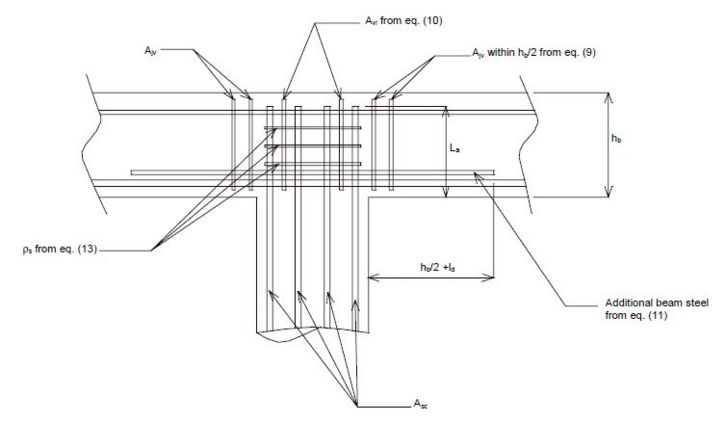
When the principal tension stress, pt, does not exceed psi, no joint cracking is expected. However, the following minimum reinforcement shall be provided:
- a) Vertical beam stirrup reinforcement within the joint based on eq. (10)
- b) Minimum horizontal hoop reinforcement based on eq. (14)
Note that the bending of any hooked reinforcement outward, away from the column core, shall not be used because it directs the anchorage force away from the joint. Inward bending of the column reinforcement is allowed. However, it is likely to cause a congestion problem. The use of straight column reinforcement embedded into the beam-column joint is recommended. The standard T-joint reinforcement details are shown in Figs. 751.40.8.11.5.4 - 751.40.8.11.5.6. If any reinforcement requirement based on eqs. (9) through (14) is greater than that shown in Figs. 751.40.8.11.5.4 - 751.40.8.11.5.6, the greater requirement shall be used.
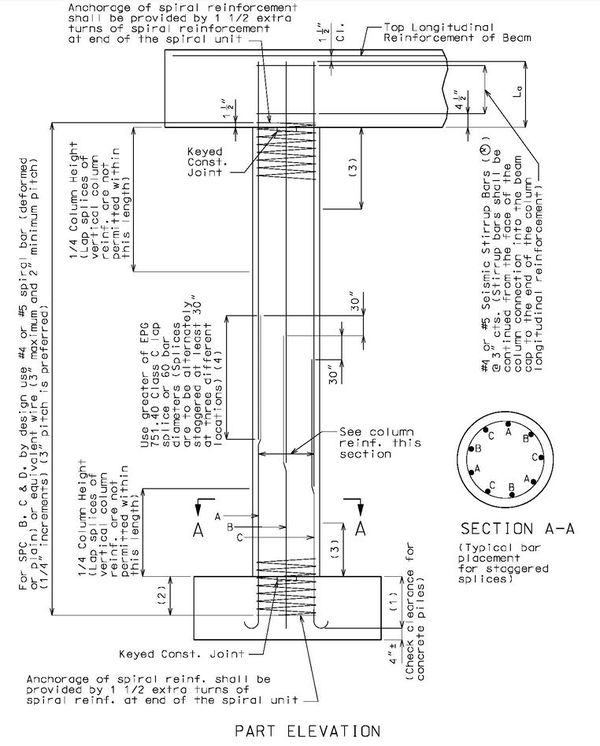
- (1) Increase by 25% the development length (other than top bars) or the standard hook in tension “Ldh” of EPG 751.40.8.4.2.
- (2) The spiral bars or wire shall be continued for a distance equal to ½ the column diameter but not less than 15” from the face of the column connection into the footing.
- (3) Use the greatest length of the following: column diameter of 1/6 of the clear height of column. Lapping of spiral reinforcement in this region is not permitted.
- (4) Splices may be eliminated when the column height is 20’-0” or less or restrictions do not practically allow for lap splices.
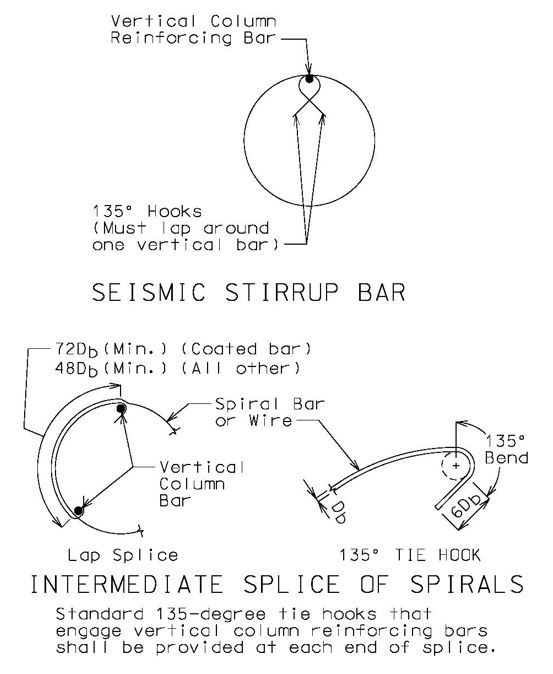
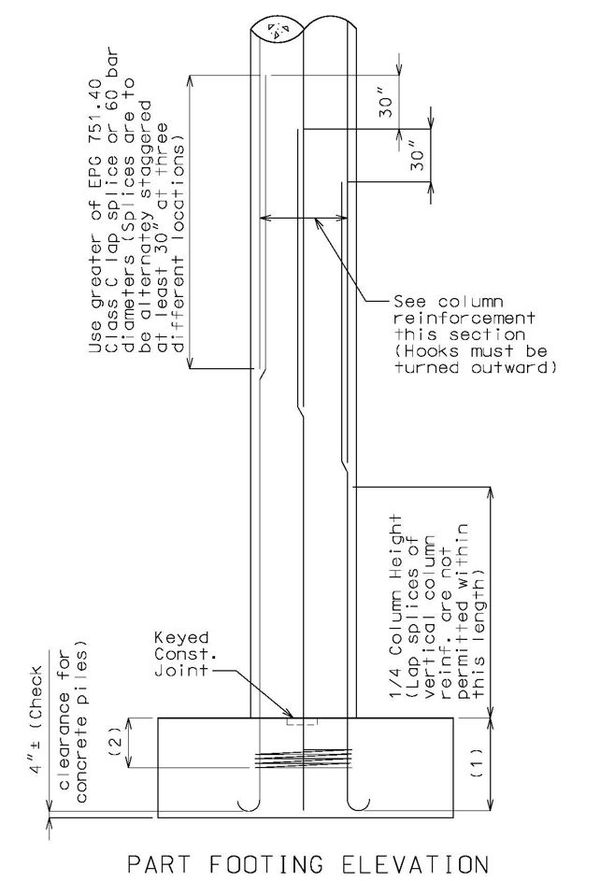
- See additional guidance in EPG 751.9.3.1.7, below, for footing reinforcement not shown.
- (1) Increase by 25% the development length (other than top bars) or the standard hook minimum in tension “Ldh” of EPG 751.40.8.4.2.
- (2) The spirals shall be continued for a distance equal to ½ the column diameter but not less than 15” from the face of the column connection into the footing.
Example 751.9.3.1.7.1: A column is subjected to an axial load (due to dead and seismic earthquake loads) of 520 kips. The column diameter is 36 in. with 20 #8 bars for longitudinal reinforcement. The beam cap dimensions are 3 ft. 9 in. wide by 3 ft. 7 in. deep with 5 #11 bars for the top reinforcement and 7 #10 bars for the bottom reinforcement as shown in Fig. 751.40.8.11.5.7. The column overstrength moment-axial load curve is shown in Fig. 751.40.8.11.5.8. Design the reinforcement details for the beam-column joint.
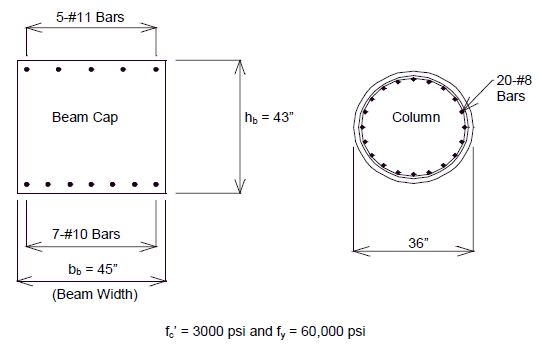
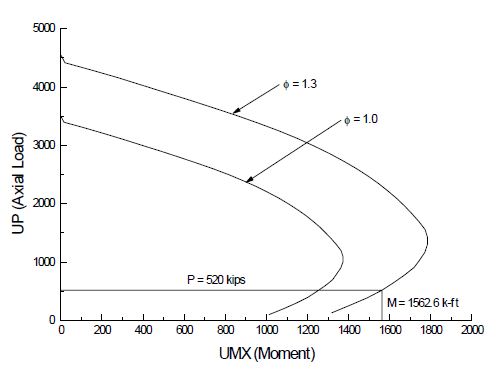
Solution:
The axial load for the column = 520 kips.
From Fig. 751.40.8.11.5.8, M0 = 1562.6 k-ft.
From eq. (1): = 436.07 kips
From eq. (3): = 45 in.
From eq. (2): = 269.18 psi.
Vertical Axial Stress:
From eq. (6):
- = 146.27 psi.
Horizontal Stress:
- fh = 0 psi.
From eq. (7):
pc = 352.07 psi ≤ 0.3(3000 psi) = 900 psi O.K.
From eq. (8):
pt = -205.80 psi ≥ 3.5 3000 = 191.7 psi Not O.K.
Since pt is greater than , special joint reinforcement based on eqs. (9) through (14) are needed.
Check if moment capacity of the beam is greater than the overstrength moment capacity of the column.
Neglect the effect of the compression steel (conservative).
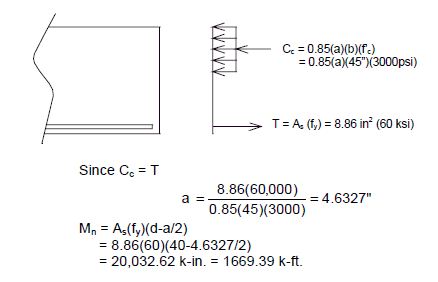
Compare moment capacity of beam versus overstrength moment capacity of the column:
- 1669.39 k-ft. > 1562.60 k-ft.
Moment capacity of beam is greater than the overstrength moment capacity of the column. O.K.
Design of reinforcement for the beam-column joint
- - Vertical reinforcement should be placed throughout a distance of hb/2 from the column face on each side of the column.
- From eq.(9):
- Asc = 15.70 in2
- From eq.(9):
- = 1.1f = 66 ksi.
- fyv = 60 ksi.
- Ajv = 0.125 (15.70) 66 / 60 = 2.16 in2
- - Reinforcement within the joint confines:
- From eq. (10):
- = 0.0625 (15.70) 66 / 60 = 1.08 in2
- From eq. (10):
- - Additional bottom of beam longitudinal reinforcement:
- From eq. (11):
- = 0.0625 (15.70) 66 / 60 = 1.08 in2
- From eq. (11):
- This reinforcement must be developed at a distance hb/2 away from the face of the column.
- - Hoop Reinforcement:
- From eq. (13):
- La = 40 in.
- fyh = 60 ksi
- ∴use ρs
- use #4 hoop reinforcement
- As = 0.1963 in2
- D’ = 36 – 2(2) – 4/8 = 31.5 in.
- ρs = 0.003238
- From eq. (15): = 7.70” spacing > 3” max. from Fig. 751.40.8.11.5.4. Therefore, Use S = 3”
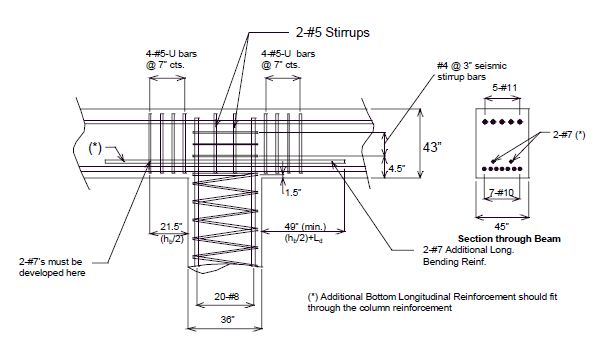
Principal Tension and Compression Stresses in Column-Footing Joints
Column – Footing joints are essentially the same as inverted beam-column T joints. Eqs. (1) through (8) are applicable to column-footing joints except the beam height, hb, shall be changed to the footing height, hf.
Design of Reinforcement for Column-Footing Joint
The design of the reinforcement for column-footing joints is similar to that for beam-column T joint. From a joint performance viewpoint, it is desirable to bend the column bars inward toward the joint by using 90° hook bars, but this will cause undue congestion. Bending column bars away from the joint will increase the diagonal tension stress within the joint region. However, it makes a stable platform for supporting the column cage and prevents congestion. When the column reinforcement is bent outward, eqs. (9) through (14) shall be applied. Since the column inelastic action may develop in directions other than parallel to one of the principal axes of the footing, the amount of vertical reinforcement in eq. (9) shall be placed in each of the four quadrant areas outside the joint. In other words, a total vertical stirrup area of:
- (16)
shall be placed around the column.
Extra top reinforcement in the footing is also required in accordance with eq. (11). This reinforcement should pass through the column reinforcement or be placed as close as possible to the sides of the column and extend a distance of not less than l = 0.5*D + Ld, where Ld is the bar development length, beyond the face on both sides of the column.
Example 751.9.3.1.7.2: A column is subjected to an axial load (due to dead and seismic loads) of 520 kips. The column diameter is 36 in. with 20 #8 bars for longitudinal reinforcement. All column reinforcement is bent outward into the footing away from the joint. The footing depth is 39 inches. The top and bottom reinforcement for the footing is shown in Fig. 751.40.8.11.5.10, below. Design the reinforcement details for the column-footing joint.
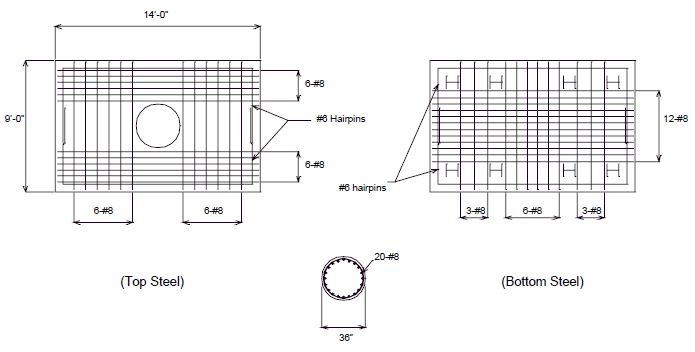
Solution:
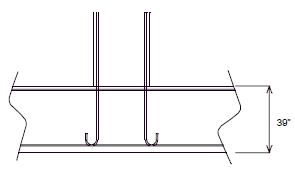
The axial load for the column = 520 kips.
From Fig. 751.40.8.11.5.8 in Example 751.9.3.1.7.1, M0 = 1562.6 k-ft.
From eq.(1): = 480.8 kips
From eq. (3):
From eq. (2): =262.39 psi.
Vertical Axial Stress:
From eq. (6):
- = 136.21psi.
Horizontal Axial Stress:
- fh = 0 psi.
Principal Stresses:
From eq. (7):
- = 339.19 psi. ≤ 0.3(3000psi.) = 900 psi. O.K.
From eq. (8):
- = -202.98 psi. > 3.5 = 191.7 psi. Not O.K.
Since pt is greater than allowed, special joint reinforcement based on eqs. (9)through (14) are needed.
Check moment capacity
Check the moment capacity of footing in the long direction to see if it is greater than the overstrength moment capacity of the column.
Neglect the effect of the compression reinforcement.
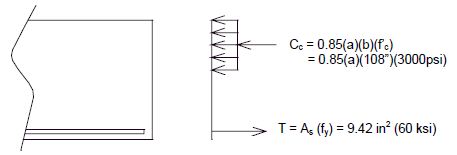
- Since Cc = T
- = 2.0523"
- Mn = As(fy)(d - a/2)
- = 9.42(60)(35-(2.0523/2))
- = 1600.17 k-ft.
Compare moment capacity of footing overstrength moment capacity of the column:
- 1600.17 k-ft > 1562.60 k-ft.
Moment capacity of the footing is greater than the overstrength moment of capacity of the column. O.K.
Check the moment capacity of the footing in the short direction to see if it is greater than the overstrength moment capacity of the column.
Neglect the effect of the compression reinforcement.
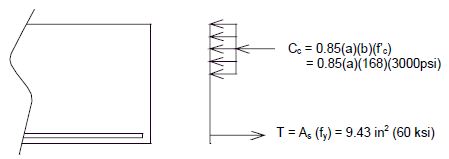
- Since Cc = T
- = 1.3207"
- Mn = As(fy)(d - a/2)
- = 9.43(60)(35-(1.3207/2))
- = 1619.11 k-ft.
Compare moment capacity of footing overstrength moment capacity of the column:
- 1619.11 k-ft > 1562.60 k-ft.
Moment capacity of the footing is greater than the overstrength moment of capacity of the column. O.K.
Design of reinforcement for the column-footing joint
- - Vertical reinforcement should be placed throughout a distance of hf/2 from the column face on each side of the column.
- From eq. (16):
- Asc = 15.71 in2
- = 1.1 fy = 66 ksi.
- fyv = 60 ksi.
- Ajv = 0.5 (15.71) (66 / 60) = 8.641 in2
- From eq. (16):
- - Reinforcement within the joint confines:
- From eqs. (9),(10) & (16):
-
- = 0.25 (15.71)(66/60) = 4.320 in2
-
- From eqs. (9),(10) & (16):
- - Additional top of footing longitudinal reinforcement:
-
- = 0.0625 (15.70)(66 / 60) = 1.08 in2
-
- This reinforcement must be developed at a distance hb/2 away from the face of the column and must be placed so that the reinforcement goes through the column reinforcement. Asb is required in both directions in the footing.
- - Hoop Reinforcement:
- From eq. (13):
- La = 35 in.
- fyh = 60 ksi
- = 0.004232
- = 0.003195
- ρs > ρs, min ∴use ρs
- Use #5 hoop reinforcement
- As = 0.3068
- D’ = 36 - 2(2) - 5/8” = 31.375”
- ρs = 0.004232
- From eq. (15): = 9.24"
- Use 9” Spacing
- Note: By adding 3 in. to footing depth in this example problem, the principal tensile stress in the joint would have been less than the maximum allowed tensile stress, thus eliminating the need for the special joint reinforcement other than the minimum required reinforcement. However, the practice of increasing footing depth to eliminate the need for the special joint reinforcement should be limited to increasing the footing depth a maximum of 6 inches.
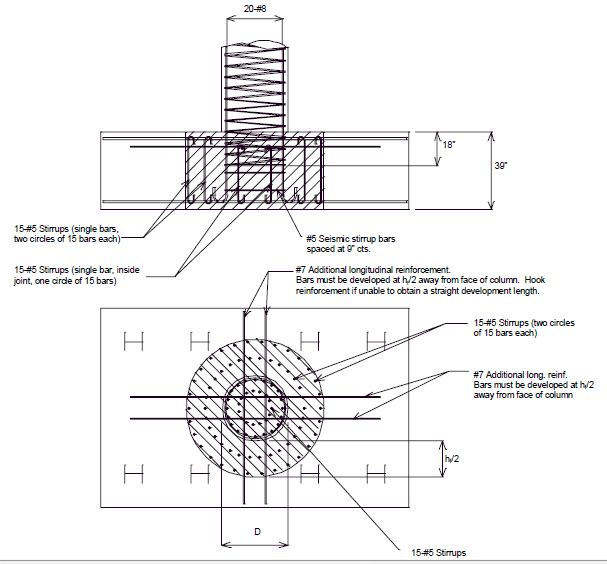
751.11.2.1 Elastomeric Bearings
General
Elastomeric Bearing design shall follow AASHTO LRFD “Method A”.
The elastomeric expansion bearings and fixed bearings for steel girders consist of a sole plate and elastomeric bearing pad. Elastomeric bearings at integral end bents and fixed bearings for prestressed girders at intermediate bents consist of elastomeric bearing pad without a sole plate.
The sole plates are flat or beveled to match the profile grade of the roadway surface along the centerline of the girder. If the profile grade is equal to or less than 0.01 or the total drop across the bearing is equal to or less than 1/8 inch, then a flat sole plate may be used and if necessary, elastomer thickness increased to address the bearing rotation due to the profile grade. Sole plates are used to anchor girders, ensure uniform distribution of the compressive stress and strain over bearing area and reduce dead load bearing rotations.
At fixed bearings, girder chairs may be considered as an alternate if roadway slope, rotation or bearing pressure is requiring tall or large bearing pads.
The elastomer bearing pad shall be 60 durometer hardness and reinforced with 1/8 inch steel shim plates when laminated pads are required by design.
When rectangular bearings are used, increased rotation bearing capacity can be achieved by orientating the pad with the shorter dimension of the pad parallel with the span of the girder.
Plain elastomeric bearing pads should be utilized where vertical loads, translations and rotations are relatively small. For integral end bents, use ½” fixed plain pads when taper due to girder slope or grade is less than 1/8”, or use a laminated bearing pad when taper equals or exceeds 1/8” due to girder slope or grade. In the rare circumstance when intermediate bents are made integral by extending the beam cap stirrups into the diaphragm, consideration can be given to utilizing ½” plain pads under similar conditions of slope.
Laminated elastomeric bearing pads should be utilized where there is greater need for vertical loading, translational and rotational capacity. For non-integral end bents, non-integral intermediate bents and for integral end bents when taper exceeds 1/8” due to girder slope or grade use laminated elastomeric bearing pads where the pad thickness and number of laminates is based on design that should account for larger vertical loads, translation, rotation and meet slope of girder and grade requirements.
Size Limitations
Use the values in the standard bearing pad tables if possible.
Bearing pad length shall be 8” minimum for MoDOT Standard Prestressed (P/S) I-Girders, Adjacent P/S Box Beams and Steel I-Girders.
Bearing pad length shall be 5” minimum for P/S NU Girders and P/S Spread Box Beams. Not preferred but for consideration of some lower bound limits as used by the Nebraska Department of Roads (NDOR) that developed the NU I-Girder, for P/S NU Girders only, and based on NDOR guidelines, a 4” minimum bearing pad length and/or 2 ft. minimum bearing pad width can be used with Structural Project Manager or Structural Liaison Engineer approval.
Plain Fixed for P/S I-Girder:
W, width of bearing ≤ Bottom flange width – 1.5”
Plain Fixed for steel girders:
Bottom flange width – 2” ≤ W ≤ Bottom flange width
Laminated Fixed for P/S I-Girder:
W = Bottom Flange width – 1.5”
Laminated Expansion Bearing Pads for PS I-Girders and
Laminated Fixed and Expansion Pads for Steel Girders:
9” ≤ W ≤ Bottom flange width + 7”
Stability
The following requirement shall be met for ensuring stability of the bearing pad:
Rectangular Pads
Circular Pads
Temperature Movement
Determining temperature movements for bearings requires the calculation of the thermal origin of the bridge. To accomplish this, the stiffness of each bent must be calculated. Once the thermal origin is established, the total temperature movement for each bearing location can be found by the following equations:
(temperature range)x(distance from thermal origin)(0.65)
Where:
= maximum shear deformation of the pad | |
= 1.2 for laminated pads | |
= 1.0 for PTFE bearings | |
= coefficient of thermal expansion | |
= 0.0000065 IN/IN/ºF (steel superstructure) | |
= 0.000006 IN/IN/ºF (concrete superstructure) | |
(0.65) | = 65% reduction due to forgiving nature of elastomer (LRFD 14.7.6.3.4) |
temperature range | = 150ºF (steel superstructure) |
= 120ºF (concrete superstructure) |
Shear Deformation
Both plain elastomeric and laminated elastomeric shall meet the following criteria for shear deformation.
Where:
= total elastomer thickness, in.
The following table represents the available heights of laminated expansion pads that are required due to the shear deformation criteria. PTFE type bearings shall be used if
Laminated Expansion Pads | |||||
---|---|---|---|---|---|
, in. | Interior layer thickness, in. | Exterior layer thickness, in. | , in. | n | C, in. |
1/2 | 1/2 | 1/4 | 1 | 2 | 1 1/4 |
3/4 | 1/2 | 1/4 | 1 1/2 | 3 | 1 7/8 |
1 | 1/2 | 1/4 | 2 | 4 | 2 1/2 |
1 1/4 | 1/2 | 1/4 | 2 1/2 | 5 | 3 1/8 |
1 1/2 | 1/2 | 1/4 | 3 | 6 | 3 3/4 |
1 3/4 | 1/2 | 1/4 | 3 1/2 | 7 | 4 3/8 |
2 | 1/2 | 1/4 | 4 | 8 | 5 |
2 1/4 | 1/2 | 1/4 | 4 1/2 | 9 | 5 5/8 |
2 1/2 | 1/2 | 1/4 | 5 | 10 | 6 1/4 |
Where:
C | = total thickness of bearing including steel shims, in. |
n | = total number of interior layers of elastomer + 1* |
* The additional “1” is accounting for the two exterior layers as per LRFD 14.7.5.3.5
Compressive Stress
Service loads without including dynamic load allowance shall be used for design checks.
At intermediate bents with 2 bearing pads per girder line (i.e. PS I-girders), use ½ of the live load reaction for each pad.
Total Load
Plain Elastomeric Pad
Laminated Elastomeric Pad
and
Minimum Dead Load
The 200 psi minimum requirement is intended for preventing the horizontal crawling of the bearing when it is not attached to the top surface. This requirement has been applied to the bearing designs detailed in EPG 751 even though these bearings are detailed with positive attachment to the flange of the girder. Compliance with the requirement is desirable but is not mandatory if it results in a special bearing design or special superstructure treatments.
Where:
= compressive stress due to total load = | |
=compressive stress due to maximum dead load = | |
=compressive stress due to minimum dead load = | |
G | = shear modulus = 0.130 ksi for compressive stress calculations |
S | = shape factor for thickest layer of elastomer = |
S | = shape factor for circular pads = |
= thickness of the ith elastomer layer, in. |
Rotation
Rotations shall be taken as the maximum possible change in slope between the top and bottom surfaces of the bearing caused by the initial lack of parallelism between the bottom of girder flange and top of bearing and the girder end rotation due to imposed loads and movements. Rotations may be calculated by a straight-line approximation of dead and live load deflections taken at 1/10 or 1/4 points. The following equation must be satisfied to ensure that uplift does not occur under any combination of loads and corresponding rotation:
Rectangular Laminated Elastomeric Pad
Where:
L | = length of bearing pad in the direction of traffic |
W | = width of bearing pad in the direction perpendicular to traffic |
G | = shear modulus = 0.200 ksi for rotation calculations |
= maximum rotation about the transverse axis due to initial lack of parallelism and total service load, rad | |
n | = total number of interior layers of elastomer + 1* |
* The additional “1” is accounting for the two exterior layers as per LRFD 14.7.5.3.5
Plain elastomeric pads contained within integral concrete diaphragms are not subject to this rotation requirement.
This criteria is intended as an uplift check. If uplift is not possible at the bearing due to an integral diaphragm/beam at the abutment or an integral diaphragm/beam at an intermediate bent, then this criteria would not be applicable.
Circular Laminated Elastomeric Pad
Where:
D = diameter of pad
Compressive Deflection
Deflections of elastomeric bearings should be limited to ensure that deck joints and seals are not damaged. Also, bearings that are too flexible can produce a small step across a deck joint giving rise to a high impact loading when traffic passes from one girder to the other. The maximum relative deflection across a joint is suggested to be less than 1/8”.
Initial compressive deflection of plain elastomeric or in any layer of steel reinforced elastomeric bearing at the service limit state without impact shall not exceed .
Values for compressive strain can be calculated by using LRFD Figure C14.7.6.3.3-1 for 60 durometer reinforced bearings.
There is a code check for compressive deflection of a single layer but no code check for total compressive deflection.
Taper
When the difference between the slope of the girder and the slope of a bearing pad exceeds 1/8” taper shall be considered. For laminated expansion pads for both PS I-Girders and steel girders and for laminated fixed pads for steel girders where sole plates are required, sole plates shall be tapered to account for the girder slope. Sole plates shall have a minimum thickness of 1 1/2” at the centerline of bearing, and a minimum thickness of 1” at the edge. Plain fixed pads shall not be tapered. At integral end bents where girder slope is greater than 1/8”, use laminated fixed pads. Laminated bearing taper is provided by tapering the top shim to match the slope of the girder to the nearest 1/8” total difference in thickness. Thickness of shims shall be a minimum of 1/8” and a maximum of 1/2”. For excessive girder slopes it may be necessary to taper the top two shims with a maximum combined taper of the bearing of 3/4 inch. Tapered layers of elastomer are not permitted.
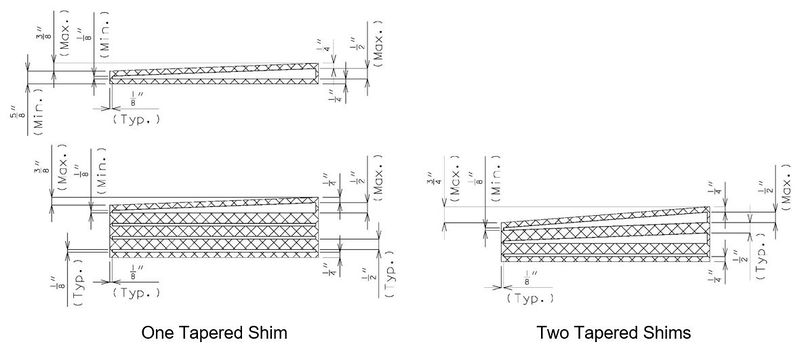
Anchor Bolts
Check with Structural Project Manager or Liaison before using anchor bolts other than ASTM F1554. When anchor bolts are used for laminated fixed for steel girders or laminated expansion for steel and P/S I-girders, they should be designed for a minimum horizontal force equal to 25% of the maximum dead load applied to the bearing. With SPM approval for rehab superstructure job designer may design anchor bolt for a minimum horizontal force equal to 15% of the maximum dead load applied to the bearing. Designer may ignore live load in horizontal force computation. Anchor bolts shall be ASTM F1554 Grade 55 unless higher grade anchor bolts are required to meet design requirements. Grade 105 bolts shall not be used in applications where welding to the bolt is required. (Revise anchor bolt notes in EPG 751.50 Standard Detailing Notes for plans with different grade and nuts, e.g. “ASTM F1554 Grade 55” to “ASTM F1554 Grade 105” and “ASTM A563 Grade A Heavy Hex nuts” to “ASTM A563 Grade DH Heavy Hex nuts”.)
Bolt properties (Updated in 2022) | ||||||||||
---|---|---|---|---|---|---|---|---|---|---|
Bolt Type | Nominal Bolt Diameter (in.) |
Min. Tensile Strength (ksi) |
Min. Yield Strength (ksi) |
Comments | ||||||
ASTM F1554 (Grade 36) | ½” to 4” | 58 | 36 | Preferred specification for structural supports anchored into concrete. | ||||||
ASTM F1554 (Grade 55) | ½” to 4” | 75 | 55 | |||||||
ASTM F1554 (Grade 105) | ½” to 3” | 125 | 105 | |||||||
ASTM A449 Type 1 Type 3 (weathering) |
¼” to 1” | 120 | 92 | Material properties are applicable for old A325 bolts (Pre-2016). May be manufactured as a threaded rod. | ||||||
over 1” to 1 ½” | 105 | 81 | ||||||||
1 ¾” to 3” | 90 | 58 | Typically used for larger diameter headed anchors for bearings in girder shelves. | |||||||
ASTM A307 | ¼” to 4” | 60 | NA | Typically used for regular strength steel connections. Should not be used for applications that require significant tensile or flexural forces on the bolt. | ||||||
ASTM F3125 Grade A325 Type 1 Type 3 (weathering) |
½” to 1 ½” | 120 | 92 | Typically used as high strength fasteners, but also used as headed anchors for bearings in girder shelves. | ||||||
ASTM F3125 Grade A490 Type 1 Type 3 (weathering) |
½” to 1 ½” | 150 | 130 | Typically used as high-strength fastener. Galvanization is not allowed. | ||||||
Note: The above table is a comprehensive list for bolts typically used in structural applications on MoDOT projects. These values will aid designers when substitutions need to be made for similar design applications. |
Anchor bolts are used on bearings with sole plates. For bridges that require seismic details only, design anchor bolts for flexure and shear induced from horizontal seismic forces and design for tension due to uplift forces if present. For bridges that require a seismic analysis, design anchor bolts for flexure induced from horizontal seismic forces and separately design for the effects of combined tension and shear.
Limit the number of bolts per bearing to four. Concrete Shear blocks shall be used when anchor bolts cannot be designed to resist earthquake loading. For shear blocks details for P/S girder see, EPG 751.22.3.13 Concrete Shear Blocks. Use similar details for shear blocks for steel girder.
Bearing details are shown in EPG 751.11.3 Details for two 1 ½”, 2” and 2 ½“ diameter anchor bolts. Consult Structural Project Manager before using bolt diameters larger than 2 1/2". Revise bearing details if four anchor bolts are required by design. For larger than 2 ½” diameter anchor bolt revise details in EPG 751.11.3.5 Anchor Bolts, bearing details and anchor bolt notes in EPG 751.50 Standard Detailing Notes.
For seismic details only (strength limit states)
Anchorage shall be adequate to resist lateral loads.
Horizontal factored shear force, in kips per girder
For expansion bearings, transverse FT = max (As, 0.25)(DL) per girder & longitudinal FL = 0.
Where DL = unfactored dead load reaction at the bent, kips
- As = Acceleration Coefficient (effective peak ground acceleration coefficient)
For fixed bearings, transverse FT = max (As, 0.25)(DL) per girder and Longitudinal FL = max (As, 0.25)(segment weight)/(# of girders)
Segment weight includes the full width of superstructure and should be distributed appropriately among fixed bents.
When centrifugal forces are present, they should be checked independently (not combined with seismic loads shown above or below). Use a 1.75 load factor with the centrifugal force and check resistance at the Strength Limit state as described below.
For complete seismic analysis
Anchor bolt designs must meet requirements for strength limit states from above as well as seismic forces from seismic analysis. Anchorage shall be adequate to resist lateral loads as well as uplift force from seismic analysis.
At Intermediate bent,
where: FH = horizontal seismic force per girder, kips
- If columns are designed for plastic hinging, use the plastic hinging shear.
= summation of top of column longitudinal shears at the bent
= summation of top of column transverse shears at the bent
NG = number of girders at the bent
At end bents
Use the same formula as above, except substitute the abutment shears in place of the top of column shears.
Pu = horizontal factored shear force per bolt, kips
nb = the number of bolts per girder
For intermediate bent, R = 1.0
For end bent, R = 1.0 for seismic category A & B and 0.8 for seismic category C & D.
Flexural Resistance
Factored flexural stress shall be less than or equal to the nominal flexural resistance. Assume the bolt is restrained from rotation by the sole plate, but free to translate.
M = Pu x L/2 = maximum moment per bolt, inch-kips
L = moment arm from center of sole plate to top of the beam cap, inches
S = section modulus for the bolt , cubic inches.
D = minimum body diameter, inches. For F1554 bolts use D = 0.92 x nominal bolt diameter. Alternately, the minimum body diameter can be retrieved from ASTM F1554 Table 4. For all other bolt types the nominal bolt diameter may be used because the bolt is unthreaded in the flexural zone and the minimum body diameter is similar to the nominal diameter.
Where:
∅f = 1.0 resistance factor for seismic details only (strength limit states) and for complete seismic analysis
Yield strength of the anchor bolt, FY = 55 ksi for Grade 55 and FY = 105 ksi for Grade 105
Shear Resistance
Factored shear force shall be less than or equal to the nominal shear resistance.
where:
∅s = 0.75 resistance for seismic details only (strength limit states) and 1.0 for complete seismic analysis
Nominal shear resistance of an F1554 anchor bolt, Rn = 0.5AbFubNs LRFD 6.13.2.12-1, C6.13.2.7 and 14.8.3
Note: ASTM F1554 allows the body diameter of the bolt to be reduced to provide an area not less than the stress area of the threaded portion of the bolt. For this reason, there are no differences in calculation for threads beings included or excluded from the shear plane. If another type of bolt is used for any reason the nominal shear resistance should be determined from LRFD Eq. 6.13.2.7-1 or 2.
Ab = nominal area of the anchor bolt, square inches
Fub = minimum tensile strength of the anchor bolt, ksi
- = 75 ksi for Grade 55, 125 ksi for Grade 105
Ns = number of shear plane per anchor bolt = 1
D = nominal bolt diameter, inches
Tensile Resistance
Factored tensile force shall be less than or equal to the nominal tensile resistance.
T = the maximum seismic tensile (uplift) force (DL ± EQ) per girder from the seismic analysis, kips. If (DL+EQ) and (DL-EQ) are both compressive, then there is no need to design the bolts for tensile force.
Where:
∅t = 0.8 resistance factor for seismic details only (strength limit states) and 1.0 for complete seismic analysis
nb = the number of bolts per girder
Nominal tensile resistance of the anchor bolt, Tn = 0.76AbFub LRFD 6.13.2.10.2-1 and 14.8.3
- where:
- Ab = nominal area of the anchor bolt, square inches
- Fub = minimum tensile strength of the anchor bolt, ksi
- = 75 ksi for Grade 55, 125 ksi for Grade 105
Combined Tension and Shear Resistance
The resistance of anchor bolts for combined tension and shear force shall be determined in accordance with LRFD 6.13.2.11.
If , then Tn = 0.76AbFub LRFD 6.13.2.11-1
Otherwise
- LRFD 6.13.2.11-2
Strength Limit States and Seismic Details only
Maximum horizontal factored shear force reaction, FH for given anchor bolts and total thickness of bearing including steel shims:
Max. shear deformation of the pad, ∆s, in. | 1/4 | 1/2 | 3/4 | 1 | 1 1/4 | 1 1/2 | 1 3/4 | 2 | 2 1/4 | ||
---|---|---|---|---|---|---|---|---|---|---|---|
Total thick. of bearing including steel shims, C in. | 1 1/4 | 1 7/8 | 2 1/2 | 3 1/8 | 3 3/4 | 4 3/8 | 5 | 5 5/8 | 6 1/4 | ||
Anchor Bolt Type | No. of Anchor Bolt |
Nominal dia. of anchor bolt, in. | Maximum horizontal factored shear force reaction, FH | ||||||||
ASTM F1554 Grade 55 |
2 | 1.5 | 28 | 22 | 17 | 15 | 13 | 11 | 10 | 9 | 8 |
2 | 67 | 51 | 41 | 35 | 30 | 26 | 23 | 21 | 19 | ||
2.5 | 131 | 100 | 81 | 68 | 58 | 51 | 46 | 41 | 38 | ||
4 | 1.5 | 57 | 43 | 35 | 29 | 25 | 22 | 20 | 18 | 16 | |
2 | 135 | 103 | 83 | 69 | 60 | 53 | 47 | 42 | 38 | ||
2.5 | 263 | 200 | 162 | 136 | 117 | 103 | 91 | 82 | 75 | ||
ASTM F1554 Grade 105 |
2 | 1.5 | 54 | 41 | 33 | 28 | 24 | 21 | 19 | 17 | 15 |
2 | 128 | 98 | 79 | 66 | 57 | 50 | 45 | 40 | 37 | ||
2.5 | 251 | 191 | 154 | 129 | 111 | 98 | 87 | 79 | 72 | ||
4 | 1.5 | 108 | 83 | 67 | 56 | 48 | 42 | 38 | 34 | 31 | |
2 | 257 | 196 | 158 | 133 | 114 | 100 | 89 | 81 | 73 | ||
2.5 | 502 | 382 | 309 | 259 | 223 | 196 | 174 | 157 | 143 | ||
Notes: | Calculations were based on 1-1/2" thick sole plate at centerline of bearing. Flexural resistance calculations were based on minimum body diameter of the anchor bolt. For centrifugal forces, check anchor bolts for separate load. For complete seismic analysis case, design anchor bolts as explained above. |
751.22.2.7 Dowel Bars
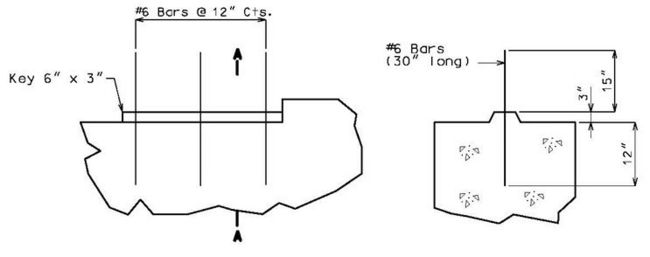
PART ELEVATION (FIXED BENT) |
SECTION A-A |
- Dowel bars shall be used for all fixed intermediate bents under prestressed superstructures. Generally, for typical bridges that require seismic details only (strength limit states), shear resistance from shear key is not considered.
Dowel bars connect standard concrete diaphragms and beams on concrete girder bridges (standard fixed diaphragms are those with beam stirrups NOT extending up into the diaphragm). For a calculated seismic vertical reaction or an anticipated foundation settlement resulting in a net tensile reaction, use the development length of dowel bars into beam and into diaphragm based on dowel bar size. If the dowel bars are not exposed to net tension a 15-inch embedment shall be used regardless of bar size. Dowel bars size and spacing shall be determined by shear design of the bars. (Minimum #6 Bars @ 12" cts.). Dowel bars should be designed for a minimum horizontal force equal to 25% of the maximum dead load applied to the bearing. Live load is ignored in horizontal force computation. For seismic design category SDC B, C and D, dowel bars shall develop minimum Ld into diaphragm but shall not extend into slab and develop minimum Ld into beam but 3” minimum clear from bottom face of the beam. Dowel bars shall not be hooked to meet development requirements.
- The number of dowels must also fit into the space available on the key:
- min. bar size = #6; max. bar size = #11
- min. spacing = 6"; max. spacing = 12"
- min. end distance = 3"; max. end distance = 6" (≤ half the spacing)
For seismic details only (strength limit states)
Horizontal factored shear force, in kips
For expansion bearings, transverse FT = max (As, 0.25)(DL) & longitudinal FL = 0 per girder.
- Where DL = unfactored dead load reaction at the bent, kips
- As = Acceleration Coefficient (effective peak ground acceleration coefficient)
For fixed bearings, Transverse FT = max (As, 0.25)(DL) and Longitudinal FL = max (As, 0.25)(segment weight) at bent.
- Segment weight includes the full width of superstructure and should be distributed appropriately among fixed bents.
For complete seismic analysis
Dowel bar designs must meet requirements for strength limit states from above as well as seismic force demand from seismic analysis.
- At Intermediate bent,
- where:
- FH = horizontal seismic force per bent, kips
- If columns are designed for plastic hinging, use the plastic hinging shear.
- ∑VL = summation of top of column longitudinal shears at the bent
- ∑VT = summation of top of column transverse shears at the bent
- Pu = Horizontal factored shear force per dowel bar, kips
- nd = number of dowel bars
Shear Resistance
Factored shear force shall be less than or equal to the nominal shear resistance.
- Pu ≤ ∅s x Rn
- where:
- ∅s = 0.75 resistance for seismic details only (strength limit states) and 1.0 for complete seismic analysis
- Nominal shear resistance of the dowel bar, Rn = 0.625 AbFub, kips
- Note: Since there is no reduced areas as seen in bolts and there is no reduction for bolted connection length, use 0.625 instead of 0.5.
- Ab = = area of the dowel bar, square inches
- Fub = minimum tensile strength of the dowel bar, ksi
- Fub = 80 ksi for Grade 60
- D = diameter of the dowel bar, inch
Tensile Resistance
Factored tensile force shall be less than or equal to the nominal tensile resistance.
- T = the maximum seismic tensile (uplift) force (DL ± EQ) from the seismic analysis, kips. If (DL+EQ) and (DL-EQ) are both compressive, then there is no need to design the dowel for tensile force.
- where:
- ∅t= 0.8 resistance factor for seismic details only (strength limit states) and 1.0 for complete seismic analysis
- nd = the number of dowel bars
- Nominal tensile resistance of the dowel bar, Tn = AbFub Kips
- Note: Since there is no pretension or reduced areas as seen for bolts, the 0.76 factor is not warranted.
- Ab = area of the dowel bar, square inches
- Fub = minimum tensile strength of the dowel bar, ksi
- Fub = 80 ksi for Grade 60
Combined Tension and Shear Resistance
The resistance of dowel bars for combined tension and shear force shall be determined in accordance with LRFD 6.13.2.11.
- Note: Since there is no pretension or reduced areas as seen for bolts, the 0.76 factor is not warranted.
- If , then Tn = AbFub
- Otherwise
- Otherwise
751.31.1.2 Rigid Frame- No Tie or Web Beam

Beam
- A = Length to be determined by the superstructure requirements or the minimum support length required for earthquake criteria, to the
- nearest 1”. Use square ends.
- B = Width to be determined by the minimum of: superstructure requirements, minimum support length required for earthquake criteria, or
- column diameter + 6”. (6” increments) (*)
- C = Depth as required by design. 2’-6” minimum and no less than the column diameter. (3” increments) (*)
- * For SDC A ratio of beam width to beam depth, B/C, shall be ≤ 1.25. For SDC B, C and D, beam depth shall be proportioned to D ≤ C ≤ 1.25 D. SGS 8.13.5-1
Columns
- D = Column diameter. 2’-6” minimum. Use 3’-0” minimum when the beam depth exceeds 3’-6”. (6” increments)
- D' = Beam width overhang. Controlled by one of the following:
- 1) Beam width controlled by superstructure requirements
- 3” ≤ D' ≤ 6”
- 2) Beam width controlled by minimum support length required for earthquake criteria.
- 3” ≤ D' ≤ 15”
- 2) Beam width controlled by minimum support length required for earthquake criteria.
- L = Spacing as determined by design, with no limit. (1” increments)
- G = Overhang as determined by design, with no limits.
- H = Column height as required by grade and footing elevations. Use construction joint in column when H exceeds 35’-0”.
- NOTE: Try to keep columns and beams the same size where possible for economy of construction.
751.31.1.3 Web Beam – Web Supporting Beam
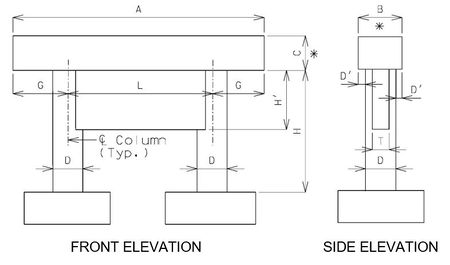
Beam
- A = Length to be determined by the superstructure requirements or the minimum support length required for earthquake criteria, to the
- nearest 1”. Use square ends.
- B = Width to be determined by the minimum of: superstructure requirements, minimum support length required for earthquake criteria, or
- column diameter + 6”. (6” increments) (*)
- C = Depth as required by design. 2’-6” minimum and no less than the column diameter. (3” increments) (*)
- * For SDC A ratio of beam width to beam depth, B/C, shall be ≤ 1.25. For SDC B, C and D, beam depth shall be proportioned to D ≤ C ≤ 1.25 D. SGS 8.13.5-1
Columns
- D = Column diameter. 3’-0” minimum. (6” increments)
- D' = Beam width overhang. Controlled by one of the following:
- 1) Beam width controlled by superstructure requirements
- 3” ≤ D' ≤ 6”
- 2) Beam width controlled by minimum support length required for earthquake criteria.
- 3” ≤ D' ≤ 15”
- 2) Beam width controlled by minimum support length required for earthquake criteria.
- L = Spacing as determined by design, with 35'-0" maximum. (1” increments)
- G = Overhang as determined by design, with no limits.
- H = Column height as required by grade and footing elevations.
Webs
- T = Web thickness. For a 3’-0” column diameter, use T = column diameter. For column diameters ≥ 3’-6”, use T = 0.5 x (column diameter).
- H' = See bottom elevations of web given on the Design Layout.
- NOTE: Try to keep columns and beams the same size where possible for economy of construction.
751.31.1.4 Tie Beam
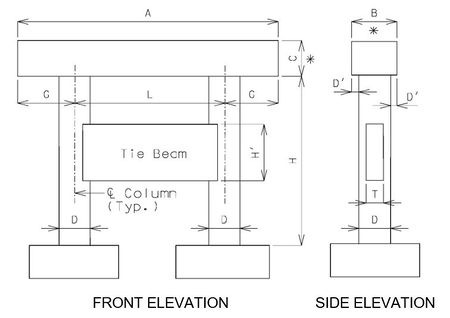
Beam
- A = Length to be determined by the superstructure requirements or the minimum support length required for earthquake criteria, to the
- nearest 1”. Use square ends.
- B = Width to be determined by the minimum of: superstructure requirements, minimum support length required for earthquake criteria, or
- column diameter + 6”. (6” increments) (*)
- C = Depth as required by design. 2’-6” minimum and no less than the column diameter. (3” increments) (*)
- * For SDC A ratio of beam width to beam depth, B/C, shall be ≤ 1.25. For SDC B, C and D, beam depth shall be proportioned to D ≤ C ≤ 1.25 D. SGS 8.13.5-1
Columns
- D = Column diameter. 3’-0” minimum. (6” increments)
- D' = Beam width overhang. Controlled by one of the following:
- 1) Beam width controlled by superstructure requirements
- 3” ≤ D' ≤ 6”
- 2) Beam width controlled by minimum support length required for earthquake criteria.
- 3” ≤ D' ≤ 15”
- 2) Beam width controlled by minimum support length required for earthquake criteria.
- L = Spacing as determined by design, with 30'-0" maximum. (1” increments)
- G = Overhang as determined by design, with no limits.
- H = Column height as required by grade and footing elevations.
Tie Beam
- T = Tie beam thickness. Minimum T = 0.5 x (column diameter).
- H' = See bottom elevations of tie beam given on the Design Layout. Minimum H' = 2 x T (round to the next foot higher).
- NOTE: Try to keep columns and beams the same size where possible for economy of construction.
751.31.1.5 Tie Beam with Change in Column Diameter
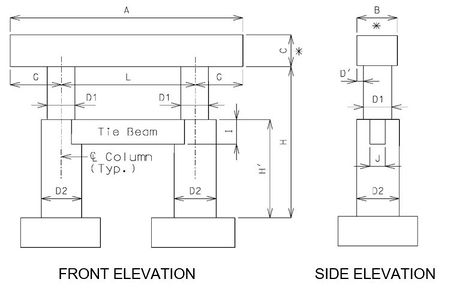
Beam
- A = Length to be determined by the superstructure requirements or the minimum support length required for earthquake criteria, to the
- nearest 1”. Use square ends.
- B = Width to be determined by the minimum of: superstructure requirements, minimum support length required for earthquake criteria, or
- column diameter + 6”. (6” increments) (*)
- C = Depth as required by design. 2’-6” minimum and no less than the column diameter. (3” increments) (*)
- * For SDC A ratio of beam width to beam depth, B/C, shall be ≤ 1.25. For SDC B, C and D, beam depth shall be proportioned to D1 ≤ C ≤ 1.25 D1. SGS 8.13.5-1
Columns
- D1 = Column diameter. 3’-0” minimum. (6” increments)
- D2 = Column diameter, Minimum of (D1 + 6”). Check lap of vertical reinforcement required. See Structural Project Manager.
- D' = Beam width overhang. Controlled by one of the following:
- 1) Beam width controlled by superstructure requirements
- 3” ≤ D' ≤ 6”
- 2) Beam width controlled by minimum support length required for earthquake criteria.
- 3” ≤ D' ≤ 15”
- 2) Beam width controlled by minimum support length required for earthquake criteria.
- L = Spacing as determined by design, with a 30’-0” maximum with tie beams and no limit without tie beams. (1” increments)
- G = Overhang as determined by design, with no limits.
- H = Column height as required by grade and footing elevations.
- H' = Approximately 0.5 x H. Top of tie beam should be at the same elevation as the top of the larger diameter columns in order to
- minimize the number of construction joints. Top of tie beam may be located on the Design Layout.
Tie Beam
- I = Depth as required by design. Minimum of 3’-0” (3” increments).
- J = Width as required by design. Minimum of (0.5 x D1).
- NOTE: Try to keep columns and beams the same size where possible for economy of construction.
751.31.2.3 General Design Assumptions
* Use only if specified on the Design Layout or as stated by the guidelines in this article.
** For column spacings greater than 30'-0", tie beams are not to be used, unless the web supports the beam.
Elevations for General Intermediate Bent
General
- The following are general design guidelines for the design of intermediate bents.
- Rigid frame design is to be used for designing Intermediate Bents and Piers.
- The joint between the beam and column, and web or tie beam and column, shall be assumed to be integral for all phases of design and must be analyzed for reinforcement requirements as a “Rigid Frame”.
- The joint between the column and footing is assumed to be “fixed”, unless foundation flexibility needs to be considered as required by the Structural Project Manager.
Beam
- Beams shall be designed for vertical loads, including a dynamic load allowance (impact) and components of horizontal forces.
- The gross concrete section, without contribution from reinforcement, shall not rupture under service dead loads. In addition, longitudinal reinforcement shall be distributed to control cracking at the Service-I limit state.
- Fatigue design should not control the size of reinforcement in the beam. LRFD 5.5.3.2 may be ignored for open concrete intermediate bents.
- The minimum reinforcement shall be such that the factored flexural resistance, Mr, is greater than or equal to the lesser of:
- Minimum Tensile Reinforcement
- The amount of tensile reinforcement shall be adequate to develop a factored flexural resistance, Mr, at least equal to the lesser of either:
- 1) Mcr = cracking moment LRFD Eq. 5.7.3.3.2-1
- 2) 1.33 times the factored moment required by the applicable strength load combinations specified in LRFD Table 3.4.1-1.
- Additional reinforcement is required in the sides of the beam. The following table gives adequate steel for both temperature and shrinkage (LRFD 5.10.8), and skin reinforcement (LRFD 5.7.3.4).
Beam Height, H | Number – Bar Size |
H ≤ 36” | 4 - #6 |
36” < H < 54” | 5 - #6 |
54” ≤ H ≤ 72” | 6 - #6 |
H > 72” | By Design (LRFD 5.7.3.4) |
Tie Beam
- Use a tie beam when specified on the Design Layout or by the Structural Project Manager or when the unsupported height exceeds 30 feet, except as noted
- Do not use tie beams on grade separations.
- Do not use tie beams when column spacing exceeds 30 feet. For this situation, use a minimum column diameter of in lieu of a tie beam.
- Additional side reinforcement shall be designed for temperature and shrinkage (LRFD 5.10.8), and skin reinforcement (LRFD 5.7.3.4).
Unsupported Height
- The unsupported height is the distance from the bottom of the beam to the top of the footing. If the distance from the ground line to the top of footing is 10 feet, the unsupported height and the fixed point may be measured from the bottom of the beam to the ground line plus 1/2 the distance from the ground line to the top of the footing.
- For single column intermediate bents, the column shall be considered “fixed” at the top of footing for all conditions.
Columns
- Use round columns for all bridges, unless otherwise specified on the Design Layout.
- Tops of column shall be designed for vertical loads with consideration of dynamic load allowance (impact) and maximum components of horizontal forces. Bottom of columns do not require impact forces to be included.
- The minimum area of reinforcement, As, shall be taken as the greater of:
- LRFD 5.7.4.2
- Where:
- = gross area of section. (in.²)
- For typical columns with f’c = 3 ksi, the 1% of column gross area will control. MoDOT prefers to follow ACI 10.9 and recognize LRFD 5.7.4.2 when it would control. (The minimum area of reinforcement based on LRFD is significantly less than ACI for f’c = 3 ksi).
Minimum Allowable Bars for Column Reinforcement Design Column Diameter Vertical Reinforcement
(Assuming 1% of Column Gross Area)2’-6” 9 - #8 3’-0” 13 - #8 3’-6” 18 - #8 4’-0” 23 - #8 4’-6” 29 - #8 5’-0” 29 - #9 5’-6” 35 - #9 6’-0” 41 - #9
- The maximum reinforcement shall be limited by the following requirements:
SGS 8.8.1
- (Preferred max for seismic design.)
- (Absolute max, LRFD 5.7.4.2)
- Spacing limitations given in this article.
Maximum Allowable Number of Bars for the Given Bar Sizes Column Diameter Maximum Number of Bars #8 #9 #10 #11 2’-6” 18 18 17 15 3’-0” 22 22 21 18 3’-6” 26 26 26 22 4’-0” 30 30 30 25 4’-6” 34 34 34 29 5’-0” 38 38 32 5’-6” 43 42 36 6’-0” 47 46 40
- Above table is applicable for standard dowel bar arrangments, see EPG 751.31.3.2.
- A preliminary economic analysis should be conducted before determining the number of columns and column spacing. For the analysis, assume the rates for Concrete, Class 1 and Class 2 Excavation, and Piles. Omit reinforcing bars in the cost analysis.
Column Spacing
- Columns, with the exception of web supporting beam type bents, shall be spaced, to the nearest 1”, in which balanced positive and negative beam moments are produced. A positive beam moment up to 10% larger than the negative beam moment is acceptable. Strength Limit State Load Combinations shall be used to determine column spacing.
- To estimate centerline-to-centerline spacing for a two column bent, use 72% of the distance from centerline of outside girder to centerline of outside girder. For a three column bent, use 44% of the centerline-to-centerline distance of outside girders.
Footings
- Footings shall be designed for vertical loads and maximum normal and parallel components of the horizontal forces.
Elevations for Intermediate Bent with Web Beam
Web Supporting Beam
- In analysis, web beams shall be modeled as plate elements. If the ability to model a web beam as a plate element is unavailable, the following may be considered:
Simplified Model
- The web itself is made up of several tie beams (typically 4 tie beams). The moment of inertia of an individual tie beam is equal to the moment of inertia of the web in the bent’s out-of-plane direction divided by the total number of tie beams.
- Any column segment which is connected to the web is treated as a prismatic member with moment of inertia in the bent’s out-of-plane direction equal to the actual column moment of inertia in that direction, and with the moment of inertia in the bent’s in-plane direction equal to the total moment of inertia of web in the bent’s in-plane direction divided by the total number of columns plus the moment of inertia of the column itself. The equivalent column diameter is assumed to be .
Section Views for an Intermediate Bent with Web Beam
In the above example, the moment of inertia of the column in the bent’s in-plane and out-of-plane directions can be calculated as:
Out-of-plane-> | |
In-plane-> |
The equivalent column diameter is then assumed to be .
Thus, the column can be treated as a telescoping column and then the moment magnifier or P-δ slenderness effects can be calculated.
Since the web is made up of 4 tie beams, the moment of inertia of the tie beams in the bent’s out-of-plane direction is:
Reinforcement
- Additional side reinforcement shall be designed for temperature and shrinkage (LRFD 5.10.8), and skin reinforcement (LRFD 5.7.3.4).
Column Spacing
- Columns shall be spaced so that the negative moment in the beam over the outside columns requires a minimum beam depth of 3.0 FT. No attempt should be made to use a column spacing that produces equal positive and negative beam moments. The negative moment is to be determined at the face of the column (for round columns, check moment at the face of an equivalent area square column).
* Use a tie beam if specified on the Design Layout or if the design calls for one.
** For column spacing > 30’, tie beams are not to be used unless the web supports the beam
Elevations for Intermediate Bent with Tie Beam
Change in Column Diameter
- Use rigid frame design.
- If H’ ≤ 0.5H and no tie beam is used, the design may be done assuming the entire column to have the smaller diameter. This will result in a very small error.
Columns
- Use round columns for all bridges, unless otherwise specified on the Design Layout.
- Use two or more columns, as required for the more economical design.
Column Spacing
- Column spacing (to the nearest 1”) should be that which produces balanced positive and negative moments. A positive beam moment up to 10% larger than the negative beam moment is acceptable. Strength Limit State Load Combinations shall be used to determine column spacing.
Reinforcement
- Reinforcement in the beams, column and tie beams for the moments at the joints shall be based on the moment at the face of the column, beam, or tie beam (equivalent square, based on areas, for round columns).
Elevations for Hammer Head Intermediate Bent
Hammer Head Type Intermediate Bent
- Hammer Head type intermediate bents shall be designed according to the applicable provisions listed under the design assumptions for the General intermediate bent guidelines except as follows:
Reinforcement
- Additional side reinforcement shall be designed for temperature and shrinkage (LRFD 5.10.8), and skin reinforcement (LRFD 5.7.3.4).
751.31.2.4 Column Analysis
Refer to this article to check slenderness effects in column and the moment magnifier method of column design. See Structural Project Manager for use of P Delta Analysis.
Transverse Reinforcement
Seismic Design Category (SDC) A
- Columns shall be analyzed as “Tied Columns”. Unless excessive reinforcement is required, in which case spirals shall be used.
Bi-Axial Bending
Use the resultant of longitudinal and transverse moments.
Slenderness effects in Columns
The slenderness effects shall be considered when:
Where:
= unsupported length of column
= radius of gyration of column cross section
= effective length factor
Effects should be investigated by using either the rigorous P-∆ analysis or the Moment Magnifier Method with consideration of bracing and non-bracing effects. Use of the moment magnifier method is limited to members with Klu/r ≤ 100, or the diameter of a round column must be ≥ Klu/25. A maximum value of 2.5 for moment magnifier is desirable for efficiency of design. Increase column diameter to reduce the magnifier, if necessary.
When a compression member is subjected to bending in both principal directions, the effects of slenderness should be considered in each direction independently. Instead of calculating two moment magnifiers, db and ds, and performing two analyses for M2b and M2s as described in LRFD 4.5.3.2.2b, the following conservative, simplified moment magnification method in which only a moment magnifier due to sidesway, δs, analysis is required:
General Procedure for Bending in a Principal Direction
- Mc = δsM2
- Where:
- Mc = Magnified column moment about the axis under investigation.
- M2 = value of larger column moment about the axis under investigation due to LRFD Load Combinations.
- δs = moment magnification factor for sidesway about the axis under investigation
Where:
= | summation of individual column factored axial loads for a specific Load Combination (kip) | |
= | stiffness reduction factor for concrete = 0.75 | |
= | summation of individual column Euler buckling loads |
Where:
= effective length factor = 1.2 min. (see the following figure showing boundary conditions for columns)
= unsupported lenth of column (in.)
Where:
= concrete modulus of elasticity as defined in EPG 751.31.1.1 (ksi)
= moment of inertia of gross concrete section about the axis under investigation
= ratio of maximum factored permanent load moments to maximum factored total load moment: always positive
Column Moment Parallel to Bent In-Plane Direction
= top of footing to top of beam cap
Column Moment Normal to Bent In-Plane Direction
= top of footing to bottom of beam cap or tie beam and/or top of tie beam to bottom of beam cap
Out-of-plane bending Non-integral Bent |
![]() |
Out-of-plane bending Integral Bent |
In-plane bending | ![]() |
Boundary Conditions for Columns
For telescoping columns, the equivalent moment of inertia, I, and equivalent effective length factor, K, can be estimated as follows:
Telescoping Columns
Where:
= length of column segment
= moment of inertia of column segment
= total length of telescoping column
Equivalent Effective Length Factor
Where:
= modulus of elasticity of column
= equivalent moment of inertia of column
= total length of telescoping column
=elastic buckling load solved from the equations given by the following boundary conditions:
Fixed- Fixed Condition
Hinged-Fixed Condition
Where:
and are defined in the previous equations.
Fixed-Fixed with Lateral Movement Condition
Where:
and are defined in the previous equations.
Fixed-Free with Lateral Movement Condition
Where:
and are defined in the previous equations.
751.31.3 ReinforcementFor Seismic detail requirements for seismic design category, SDC B, C and D, See EPG 751.9.1.2 LRFD Seismic Details. 751.31.3.2 Column
751.37.1.6 Drilled Shaft General Detail ConsiderationsFor Seismic detail requirements for seismic design category, SDC B, C and D, See EPG 751.9.1.2 LRFD Seismic Details. ![]() Pay items shown in above table are for example only, show actual pay items and quantities in plan details for specific project. Notes:
751.37.6.1 Reinforcement DesignDrilled shaft structural resistance shall be designed similarly to reinforced concrete columns. The Strength Limit State and applicable Extreme Event Limit State load combinations shall be used in the reinforcement design. Longitudinal reinforcing steel shall extend below the point of fixity of the drilled shaft at least 10 ft. in accordance with LRFD 10.8.3.9.3 or the required bar development length whichever is larger. If permanent casing is used, and the shell consists of smooth pipe greater than 0.12 in. thick, it may be considered load carrying. An 1/8" shall be subtracted off of the shell thickness to account for corrosion. Casing could also be corrugated metal pipe. If casing is assumed to contribute to the structural resistance, the plans should indicate the minimum thickness and type of casing required. Minimum clear spacing between longitudinal bars as well as between transverse bars shall not be less than five times the maximum aggregate size or 5 in. (LRFD 10.8.3.9.3). For minimum concrete cover for drilled shaft, see Sec 701.4.12.1. If drilled shaft diameter does not match Sec 701.4.12.1 then use concrete cover for the next greater diameter drilled shaft. For rock sockets use 3” min. clear cover. For longitudinal reinforcement, splicing shall be in accordance with LRFD 5.10.8.4. For transverse reinforcement, lap splices for closed circular stirrups/ties shall be provided and staggered in accordance with LRFD 5.10.4.3. Lap length of 1.3 ld (Class B) for closed stirrups/ties shall be provided in accordance with LRFD 5.10.8.2.6d. For lap length, see EPG 751.5.9.2.8.1 Development and Lap Splice General.
751.37.6.2 Longitudinal ReinforcementLongitudinal reinforcement shall be designed to resist bending in the shaft due to lateral loads. The cross-sectional area for longitudinal reinforcement shall fall within the following limits:
where:
MoDOT prefers to follow LRFD 5.7.4.2 for drilled shafts since for typical cases, the potential exists for load transfer between the concrete and steel casing. (The minimum area of reinforcement based on LRFD is 10 percent less than ACI for f’c = 4 ksi).
751.37.6.4 Transverse ReinforcementMinimum transverse reinforcement shall be designed to resist the potential of diagonal cracking and improve ductility, and to control the stability of the reinforcement cage. Follow the four-step procedure, below for seismic design category SDC A. For Seismic detail requirements for seismic design category, SDC B, C and D, See EPG 751.9.1.2 LRFD Seismic Details. No. 1. Determine if Transverse Reinforcement is Required for Loading
No. 4. Determine Maximum Transverse Shaft Reinforcement Spacing at the Anchorage of Column Reinforcement:
751.38.8.3.1 Spread Footing Reinforcement
751.39.1 DimensionsLong, narrow footings (length to width ratio ≥ 2.0) supporting individual columns are not desirable, and care should be taken to avoid their use unless space constraints or eccentric loading dictate otherwise.
* The maximum pile spacing is 4'-0". ** 3'-0" (Min.) & 6'-0" (Max.) for steel HP piles, 14" CIP piles. 3D (Min.) and 6D (Max.) for 16”, 20" and 24" CIP piles. (D = pile diameter)
751.39.5 ReinforcementUnreinforced Footing - Use only in Seismic Design Category A The term “unreinforced footing” is used for footings where only #6 hairpin bars are required. Do not use unreinforced footing if SDC A, SD1 ≥ 0.1 for applicable routes per Bridge Seismic Design Flowchart. Unreinforced footings shall only be used when the shear line for all piles is within the column projected, or where additional flexural steel is not required by design (not typical).
* See EPG 751.5.9.2.8.2. Notes: Use Class B lap splice of deformed bars in tension.
If SDC A, SD1 ≥ 0.1, provide seismic details similar to SDC B for applicable routes per Bridge Seismic Design Flowchart.
* See See EPG 751.5.9.2.8.2. Notes: Use Class B lap splice of deformed bars in tension.
For anchorage of piles for seismic details for SDC B, C and D, see EPG 751.36.4 Anchorage of Piles for Seismic Details. * For reinforcement in top of the footing and bottom of footing, See EPG 751.5.9.2.8.2 for lap splice.
**Place the top reinforcement uniformly outside the column reinforcement. Use same area of steel in the top of the footing as is required for the bottom. For pile footing joint shear reinforcement requirement for SDC C and D, see EPG 751.9.1.2.4.2 Footing (Spread Footing and Pile Cap Footing) Joint Shear Reinforcement.
G1. Concrete BentsExpansion Device at End Bents (G1.1 and G1.1.1) (G1.1)
(G1.1.1)
(G1.2)
(G1.3)
(G1.5) Use for Non-Integral End Bents only.
(G1.6) Add to sheet showing the typical section thru wing detail.
(G1.7) Place with part plan of end bent, second F bar required for skewed bents.
(G1.7.1) Use for skewed bents. Place with plan of beam showing reinforcement and part plan of end bent, V bars not required with part plan of end bent.
(G1.8) Place with part plan of end bent.
P/S Structures (G1.9 and G1.9.1). place with part plan of end bent. (G1.9)
(G1.9.1) Use appropriate girder sheet number.
(G1.10) Use for steel structures without steel diaphragms at end bents.
(G1.11)
All Substructure Sheets with Anchor Bolts (G1.15A)
(G1.15B) Use unless only anchor bolt wells are preferred, i.e. uplift, congested reinforcement, etc.
(G1.16)
(G1.17) Use for P/S structures and for steel structures when the chair material is not the pay item material.
(G1.18) Use for structures with steel beam or girder pay items. Place below the substructure quantity box of all bents with chairs using the same pay item for (a) as used in Note G1.16.
(G1.19) Place with the other bent notes. Second sentence is required when the chair details are located with other bent details. Reinforcing steel shall be shifted to clear chairs. For details of chairs, see Sheet No. . Pile Cap Bents. (G1.20) Place with plan showing reinforcement.
Vertical Drains at End Bents. (G1.25) Place with part plan of end bent.
Bridge Approach Slab. (G1.30) Place with part plan of end bent.
(G1.40) Use the following note at all fixed intermediate bents on prestressed girder bridges with steps of 2" or more. Place with plan of beam.
(G1.41a) Use the following note when vertical column steel is hooked into the bent beam for seismic category A.
(G1.41b) Use the following note when vertical column steel is hooked into the bent beam for seismic category B, C or D.
(G1.42) Place the following note on plans when using Optional Section for Column-Web beam joints.
(G1.43) Place the following note on plans when you have adjoining twin bridges.
(G1.44) Use with column closed circular stirrup/tie bar detail.
(G1.45) Use when mechanical bar splices (MBS) are to be specified on the plans for column and drilled shaft vertical reinforcement.
REVISION REQUEST 4034!!! Only replace first part of 751.9.1 up to 751.9.1.1 !!! 751.9.1 Seismic Analysis and Design SpecificationsAll new or replacement bridges on the state system shall include seismic design and/or detailing to resist an expected seismic event per the Bridge Seismic Design Flowchart. For example, for a bridge in Seismic Design Categories A, B, C or D, complete seismic analysis or seismic detailing only may be determined as per “Bridge Seismic Design Flowchart”. Missouri is divided into four Seismic Design Categories. Most of the state is SDC A which requires minimal seismic design and/or detailing in accordance with SGS (Seismic Zone 1 of LRFD) and “Bridge Seismic Design Flowchart”. The other seismic design categories will require a greater amount of seismic design and/or detailing. For seismic detailing only: When AS is greater than 0.75 then use AS = 0.75 for abutment design where required per “Bridge Seismic Design Flowchart” and SEG 24-01 For complete seismic analysis: When AS is greater than 0.75 then use AS = 0.75 at zero second for seismic analysis and response spectrum curve. See Example 1_SDC_Response_Spectra. The other data points on the response spectrum curve shall not be modified. When existing bridges are identified as needing repairs or maintenance, a decision on whether to include seismic retrofitting in the scope of the project shall be determined per the “Bridge Seismic Retrofit Flowchart”, the extent of the rehabilitation work and the expected life of the bridge after the work. For example, if the bridge needs painting or deck patching, no retrofitting is recommended. However, redecking or widening the bridge indicates that MoDOT is planning to keep the bridge in the state system with an expected life of at least 30 more years. In these instances, the project core team should consider cost effective methods of retrofitting the existing bridge. Superstructure replacement requires a good substructure and the core team shall decide whether there is sufficient seismic capacity. Follow the design procedures for new or replacement bridges in forming logical comparisons and assessing risk in a rational determination of the scope of a superstructure replacement project specific to the substructure. For example, based on SPC and route, retrofit of the substructure could include seismic detailing only or a complete seismic analysis may be required determine sufficient seismic capacity. Economic analysis should be considered as part of the decision to re-use and retrofit, or re-build. Where practical, make end bents integral and eliminate expansion joints. Seismic isolation systems shall conform to AASHTO Guide Specifications for Seismic Isolation Design 4th Ed. 2023. Bridge seismic retrofit for widenings shall be in accordance with Bridge Seismic Retrofit Flowchart. Seismic details should only be considered for widenings where they can be practically implemented and where they can be uniformly implemented as not to create significant stress redistribution in the structure. When a complete seismic analysis is required for widenings the existing structure shall be retrofitted and the new structural elements shall be detailed to resist seismic demand.
751.40.3.2 Bent Cap Shear Strengthening using FRP Wrap
Fiber Reinforced Polymer (FRP) wrap may be used for Bent Cap Shear Strengthening. FRP wrap may also be used for seismic retrofit of existing columns, but that procedure is not discussed herein (see EPG 751.9.1 Seismic Analysis and Design Specifications). When to strengthen: When increased shear loading on an existing bent cap is required and a structural analysis shows insufficient bent cap shear resistance, bent cap shear strengthening is an option. An example of when strengthening a bent cap may be required: removing existing girder hinges and making girders continuous will draw significantly more force to the adjacent bent. An example of when strengthening a bent cap is not required: redecking a bridge where analysis shows that the existing bent cap cannot meet capacity for an HS20 truck loading, and the new deck is similar to the old deck and the existing beam is in good shape. How to strengthen: Using FRP systems for shear strengthening follows from the guidelines set forth in NCHRP Report 678, Design of FRP System for Strengthening Concrete Girders in Shear. The method of strengthening, using either discrete strips or continuous sheets, is made optional for the contractor in accordance with NCHRP Report 678. A Bridge Standard Drawing and Bridge Special Provision have been prepared for including this work on jobs. They can be revised to specify a preferred method of strengthening if desired, strips or continuous sheet. What condition of existing bent cap required for strengthening: If a cap is in poor shape where replacement should be considered, FRP should not be used. Otherwise, the cap beam can be repaired before applying FRP. Perform a minimum load check using (1.1DL + 0.75(LL+I))* on the existing cap beam to prevent catastrophic failure of the beam if the FRP fails (ACI 440.2R, Guide for the Design and Construction of Externally Bonded FRP, Sections 9.2 and 9.3.3). If the factored shear resistance of the cap beam is insufficient for meeting the factored minimum load check, then FRP strengthening should not be used.
Design force (net shear strength loading): Strengthening a bent cap requires determining the net factored shear loading that the cap beam must carry in excess of its unstrengthened factored shear capacity, or resistance. The FRP system is then designed by the manufacturer to meet this net factored shear load, or design force. The design force for a bent cap strengthening is calculated considering AASHTO LFD where the factored load is the standard Load Factor Group I load case. To determine design force that the FRP must carry alone, the factored strength of the bent cap, which is 0.85 x nominal strength according to LFD design, is subtracted out to give the net factored shear load that the FRP must resist by itself. NCHRP Report 678 is referenced in the special provisions as guidelines for the contractor and the manufacturer to follow. The report and its examples use AASHTO LRFD. Regardless, the load factor case is given and it is left to the manufacturer to provide for a satisfactory factor of safety based on their FRP system. Other References:
I5. Fiber Reinforced Polymer (FRP) Wrap – Intermediate Bent Column Strengthening for Seismic Details for Widening. Report following notes on Intermediate bent plan details.(I5.1)
(I5.2)
REVISION REQUEST 4036106.3.2.93.1 Means of Evaluating Aggregate Alkali Carbonate Reactivity1. Chemical Analysis The chemical analysis of aggregate reactivity is an objective, quantifiable and repeatable test. MoDOT will perform the chemical analysis per the process identified in ASTM C 25 for determining the aggregate composition. The analysis determines the calcium oxide (CaO), magnesium oxide (MgO), and aluminum oxide (Al2O3) content of the aggregate. The chemical compositions are then plotted on a chart with the CaO/MgO ratio on the y-axis and Al2O3 percentage on the x-axis per Fig. 2 in AASHTO R 80. Aggregates are considered potentially reactive if the Al2O3 content is greater than or equal to 1.0% and the CaO/MgO ratio is either greater than or equal to 3.0 or less than or equal to 10.0 (see chart below). See flow charts in 106.3.2.93.2 for approval hierarchy. CaO, MgO and Al2O3 shall be analyzed by instrumental analysis only. * MoDOT’s upper and lower limits of potentially reactive (shaded area) aggregates. 2. Petrographic Examination A petrographic examination is another means of determining alkali carbonate reactivity. The sample aggregate for petrographic analysis will be obtained at the same time as the source sample. MoDOT personnel shall be present at the time of sample. The petrographic sample shall be placed in an approved tamper-evident container (provided by the quarry) for shipment to petrographer. Per ASTM C 295, a petrographic examination is to be performed by a petrographer with at least 5 years of experience in petrographic examinations of concrete aggregate including, but not limited to, identification of minerals in aggregate, classification of rock types, and categorizing physical and chemical properties of rocks and minerals. The petrographer will have completed college level course work in mineralogy, petrography, or optical mineralogy. MoDOT does not accept on-the-job training by a non-degreed petrographer as qualified to perform petrographical examinations. MoDOT may request petrographer’s qualifications in addition to the petrographic report. The procedures in C 295 shall be used to perform the petrographic examination. The petrographic examination report to MoDOT shall include at a minimum:
See flow charts in EPG 106.3.2.93.2 for the approval hierarchy. See EPG 106.3.2.93.3 for petrographic examination submittals. No direct payment will be made by the Commission for shipping the petrographic analysis sample to petrographer, or for the petrographic analysis performed by the petrographer. 3. Concrete Prism/Beam Test ASTM C 1105 is yet another means for determining the potential expansion of alkali carbonate reactivity in concrete aggregate. MoDOT will perform this test per C 1105 at its Central Laboratory. Concrete specimen expansion will be measured at 3, 6, 9, and 12 months. The test specimens will be considered alkali carbonate reactive (expansive) if the specimens expand greater than 0.015% at 3 months, 0.025% at 6 months, or 0.030% at 12 months. See flow chart in EPG 106.3.2.93.2 for the approval hierarchy.
REVISION REQUEST 40381018.5 Laboratory Procedures for Sec 10181018.5.1 Sample PreparationPrior to testing, the sample should be thoroughly mixed, passed through a No.20 [850 mm] sieve, and brought to room temperature. All foreign matter and lumps that do not pulverize easily in the fingers must be discarded. 1018.5.2 ProcedureChemical analysis is to be conducted according to ASTM C114 and MoDOT Test Methods T46 and T91. Original test data and calculations are to be recorded in Laboratory workbooks. Test results are to be recorded through AWP and retained on file in the Laboratory. Physical tests on the following are to be conducted in accordance with ASTM C311.
Original test data and calculations are to be recorded in Laboratory workbooks. Test results are to be recorded through AWP and retained on file in the Laboratory. 1018.5.3 Source AcceptanceSamples are to be taken by the manufacturer in accordance with ASTM C311 from the conveyor, after exiting the precipitator collector and prior to entry into the designated storage silo, or where designated by the engineer. Ash, that is manually sampled and tested every 400 tons, is to be held until the required tests have been run and the results are properly certified and are available for pick up by MoDOT personnel prior to shipment. Ash, that is continually sampled and tested at a frequency and duration acceptable to the engineer, can be continuously shipped direct from a generating station silo, provided the following minimum criteria are met:
1018.5.4 Plant InspectionQualified fly ash manufacturers and terminals shipping material by certification to Department projects shall be inspected on a regular basis by a representative of the Laboratory. This inspection shall include a review of plant facilities for producing a quality product; plant testing procedures; frequency of tests; plant records of daily test results and shipping information; company certification procedures of silos, bins, and/or shipments; and a discussion of items of mutual interest between the plant and the Department. The Laboratory representative shall coordinate test results and test procedures between the Laboratory and the respective plant laboratory, and investigate associated problems. All silo or bin certifications and results of complete physical and chemical tests received in the Laboratory are to be checked for specification compliance and to determine if the required certifications have been furnished. 1018.5.5 Sample RecordThe sample record shall be completed in AASHTOWARE Project (AWP) in accordance with AWP MA Sample Record, General, and shall indicate acceptance, qualified acceptance, or rejection. Appropriate remarks, as described in EPG 106.20 Reporting, are to be included in the remarks to clarify conditions of acceptance or rejections. Test results shall be reported on the appropriate templates under the Tests tab.
REVISION REQUEST 4041751.31.2.4 Column AnalysisRefer to this article to check slenderness effects in column and the moment magnifier method of column design. See Structural Project Manager for use of P Delta Analysis.
Seismic Design Category (SDC) A
Bi-Axial Bending Use the resultant of longitudinal and transverse moments. Slenderness effects in Columns The slenderness effects shall be considered when:
Where: = unsupported length of column = radius of gyration of column cross section = effective length factor Effects should be investigated by using either the rigorous P-∆ analysis or the Moment Magnifier Method with consideration of bracing and non-bracing effects. Use of the moment magnifier method is limited to members with Klu/r ≤ 100, or the diameter of a round column must be ≥ Klu/25. A maximum value of 2.5 for moment magnifier is desirable for efficiency of design. Increase column diameter to reduce the magnifier, if necessary. When a compression member is subjected to bending in both principal directions, the effects of slenderness should be considered in each direction independently. Instead of calculating two moment magnifiers, and , and performing two analyses for M2b and M2s as described in LRFD 4.5.3.2.2b, the following conservative, simplified moment magnification method in which only a moment magnifier due to sidesway, δs, analysis is required:
Where:
Where: = effective length factor = 1.2 min. (see the following figure showing boundary conditions for columns) = unsupported length of column (in.)
Where: = concrete modulus of elasticity as defined in EPG 751.31.1.1 (ksi) = moment of inertia of gross concrete section about the axis under investigation = ratio of maximum factored permanent load moments to maximum factored total load moment: always positive
= top of footing to top of beam cap
= top of footing to bottom of beam cap or tie beam and/or top of tie beam to bottom of beam cap
For telescoping columns, the equivalent moment of inertia, I, and equivalent effective length factor, K, can be estimated as follows:
Where: = length of column segment = moment of inertia of column segment = total length of telescoping column
Where: = modulus of elasticity of column = equivalent moment of inertia of column = total length of telescoping column =elastic buckling load solved from the equations given by the following boundary conditions: Warning: The following equations were developed assuming equal column segment lengths. When the segment lengths become disproportionate other methods should be used to verify Pc.
Fixed-Fixed Condition
Where: and are defined in the previous equations.
Fixed-Fixed with Lateral Movement Condition Where: and are defined in the previous equations.
Fixed-Free with Lateral Movement Condition Where:
The following procedure may be used to reduce the effective length factor for column or pile bents where the beam cap is doweled into a concrete superstructure diaphragm. This procedure is applicable for out-of-plane bending only. The less stiff the substructure the larger the benefit expected from this procedure. The equation for rotational stiffness assumes the dowel bars are fully bonded in the superstructure and beam. To utilize this procedure the dowel bars shall be developed ld min into diaphragm and beam but shall not extend into slab and shall clear bottom of beam by 3 inches minimum. Dowel bars shall not be hooked to meet development requirements.
The following procedure is developed for the most common substructure type (columns on drilled shafts). This procedure is greatly simplified for non-telescoping column bents and pile bents. Step 1 – Determine the rotational stiffness at top of bent per ft length of diaphragm,
Where:
Step 2 – Determine the rotational stiffness at top of column, To determine the rotational stiffness at top of column, the rotational stiffness at top of bent, , shall be multiplied by the beam cap length and divided by the number of columns. The beam cap length is substituted for the diaphragm length to simplify the calculations and has a marginal affect on the final result. Step 3 – Determine the buckling load assuming no rotational stiffness at top, For a non-telescoping column on footing or pile with in-ground point of fixity: Note: this step is not required for a non-telescoping column or pile bent but shown here for completeness. Where:
For a telescoping column: As noted above the equations provided for determining the buckling load of telescoping columns are not accurate for diverging segment lengths. The following equation is provided and may be used for the fixed-free with lateral movement condition. Where: Step 4 – Determine the equivalent moment of inertia for a non-telescoping column using Note: This step is only required for telescoping columns. Step 5 – Determine ideal k A bilinear approximation is used to determine the ideal effective length factor for out-of-plane bending, . Note: for non-telescoping columns or piles ![]() Step 6 – Adjust for design The effective length factor for out-of-plane bending requires an adjustment for design conditions. K=2.1k/2.0 Step 7 – Determine refined buckling load The buckling load can be calculated using the equivalent non-telescoping column moment of inertia.
REVISION REQUEST 4042REVISION REQUEST 4043Federal regulations require MoDOT to submit a certification, upon completion and acceptance of a project, stating that the materials incorporated into the work substantially met the requirements of the contract. In addition, MoDOT is required to cite any shortages of material inspection or circumstances of acceptance of materials, which did not receive normal inspection. Materials summaries are required for all federal and state contracts, except job order contracts (JOCs). The Construction and Materials Division has been designated by the department to be the certifying agent. It is the intent of the specifications that all materials be properly inspected and reported for a specific project. However, it is realized that the total inspected quantity of a specific material might not always be attained. These instances should normally be rare. If shortages of inspected and reported quantities occur, the District Construction and Materials Engineer should determine if substantial compliance has been met. Substantial compliance indicates that there is a reasonable tolerance that could be applied. It has been determined that the reasonable tolerance would be a maximum of 10 percent, however, this tolerance should be used judicially, dependent upon the type and quantity of material represented. To comply with the requirements of the Federal Highway Administration and to ascertain that the materials have been properly inspected and reported, the procedures set forth in this article should be followed. 106.21.1 ProcedureUpon completion of a project, a statement attesting that all materials incorporated into the project were properly and adequately inspected is to be submitted to Central Office Construction and Materials. The statement shall include any exceptions as to material shortages or lack of inspection. A copy of the desired statement is shown as Figure 106.21.1 and is to be signed by the District Engineer or District Construction and Materials Engineer, or another individual as assigned by the District Construction and Materials Engineer. Central Office Construction and Materials is to be notified in writing of the individuals given this responsibility. The signature indicates that all data submitted has been reviewed by individuals reasonably familiar with the project and the data is correct and complete. This statement is to be accompanied by a Summary Packet. These documents should be completed and forwarded within four weeks for small projects or six weeks for large projects, from the date final quantities for the project have been established. A small contract is defined as having fewer than 40 bid items and an original bid amount of less than $1,000,000.00. If for some reason the summary cannot be completed and forwarded within this time frame, Central Office Construction and Materials should be notified. The Resident Engineer’s staff or the district final plans processor will enter an Informational Date 030 Project Data Ready for Materials Summary (MCF) to indicate that data required for the summary is ready for use and that no additional changes are anticipated. This Informational Date will start the four- or six-week period. 106.21.1.1 Summary Packet of Materials InspectedThe summary packet, as prepared through AWP and Cognos, is to include the following components:
Attachment Page(s), any supporting information relative to shortages or exceptions to standard policy. 106.21.1.2 Combination ProjectsCombination projects may be shown on the same summary providing each project is finaled within the four- or six-week period. A summary on one project should not be significantly delayed until another project is finished. When summary cover letters or statements are submitted in combination, any notations of shortages or exceptions should specify affected project(s). Status of 2AA sheets should be stated for individual projects when submitted in combination. 106.21.2 DistributionThe statement, summary of materials inspected packet and substantiating documents shall be saved electronically to eProjects with the Content Type of “CM Materials - Materials Summary”. The Actual Date for the Informational Date “080 Materials Summary Submitted to HQ” in AASHTOWARE Project (AWP) shall also be entered. An email with a link to the eProjects Materials Summary documents shall be sent to Bethany Evers Administrative Technician notifying her of the completion of the materials summary. CM Division will populate the Actual Date field for the AWP Informational “095 Materials Summary Approved by HQ”. Figures![]() ![]() ![]() ![]() ![]() ![]()
|